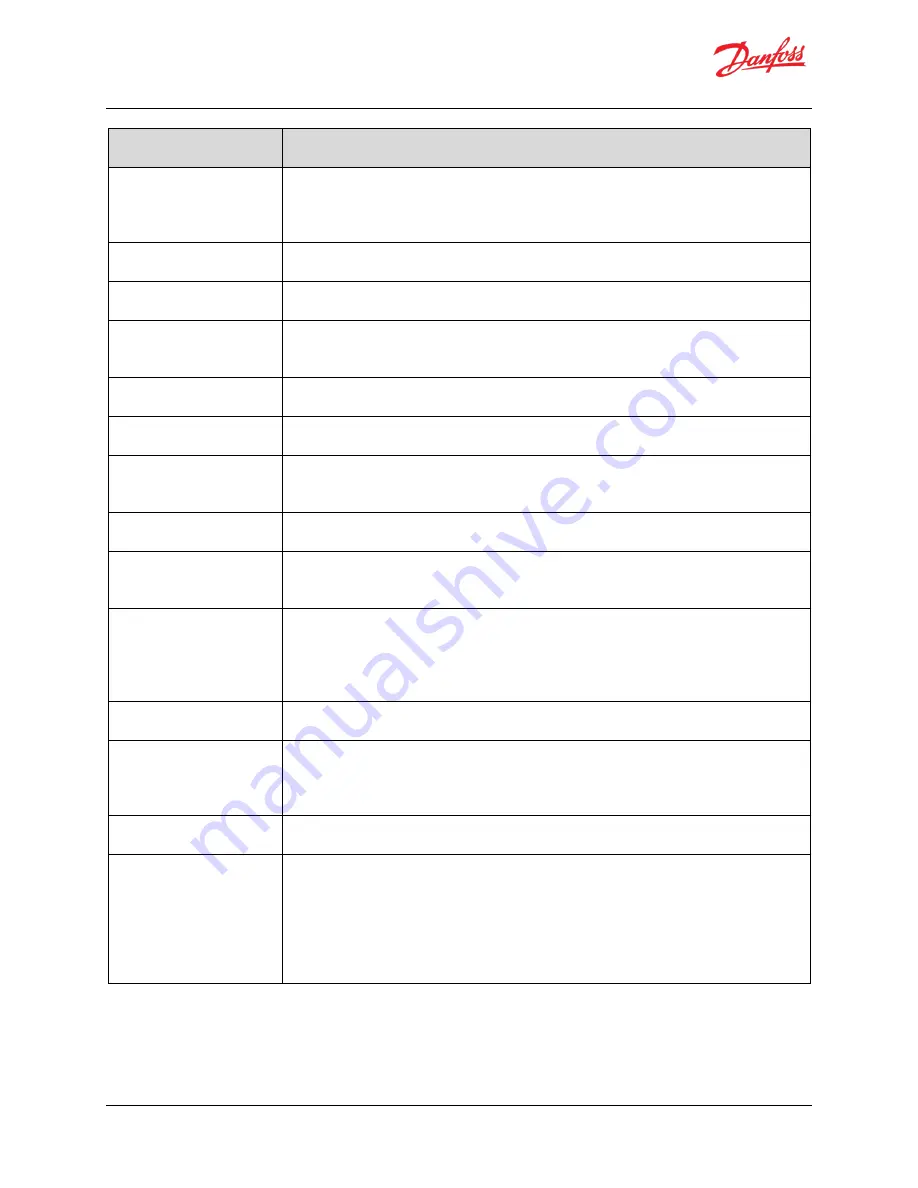
Installation and Operation Guide
ED-DT318B
Drive Train Systems with Traction Control, Inverter/Controller, and Motor with 2 Speed Transmission
BC353060341319en-000101
Revision D
© Danfoss | November 2020 | 137
Classified as Business
Column Label
Description
Motor Direction
The direction of the motor. 1 is “Forward” and –1 is “Reverse.” This value
multiplied by either Speed or FilteredSpeed provides signed speed values like
those available through CANbus.
Stator Temp (ºC)
The measured temperature of the stator of the motor in degrees Celsius.
Rotor Temp (ºC)
The measured temperature of the rotor of the motor in degrees Celsius.
Inverter Temp (ºC)
The measured temperature of the controller at its cooling block in degrees
Celsius.
Bus Voltage (V)
The measured bus voltage in volts.
Bus Current (A)
The measured bus current in amperes.
Elec Power (W)
The electrical power in watts as calculated by the controller from the bus voltage
and current.
Leg Current (A)
The measured envelope of the current motor’s phase legs.
Acceleration (RPM/sec)
The calculated rate of acceleration of the Danfoss Power Solutions motor. The
maximum acceleration rate can be controlled by the .
Stall Percentage
The stall percentage value counts up from 0 to 100 as the motor approaches stall
conditions. When the count reaches 100, a stall condition is detected, and the
motor will limit torque to 10% of rated output for 30 seconds. For more
information on stall conditions, please refer to
Section 5.3.3
RevCounter
Positive integer number of motor revolutions since the inverter was power up
AngularDistance
Total angular distance the motor has traveled since the inverter was powered up
(1 count = 3.75°). Travel in the Forward direction is positive. Travel in the Reverse
direction is negative.
Desired Direction
The requested direction of the motor. A 1 is “Forward” and –1 is “Reverse.”
Requested Torque
(Nm)
This is the amount of torque requested by the user, in Newton meters. The values
reported in this column come directly from the received CAN torque commands.
This is useful in debugging because it allows the user to check whether the CAN
commands contained the correct values and were received by the controller. In
contrast, the
Desired Torque
column reports the torque that the controller intends
to produce, after applying safeties and limits to the requested torque.
Содержание ED-DT318B
Страница 185: ......