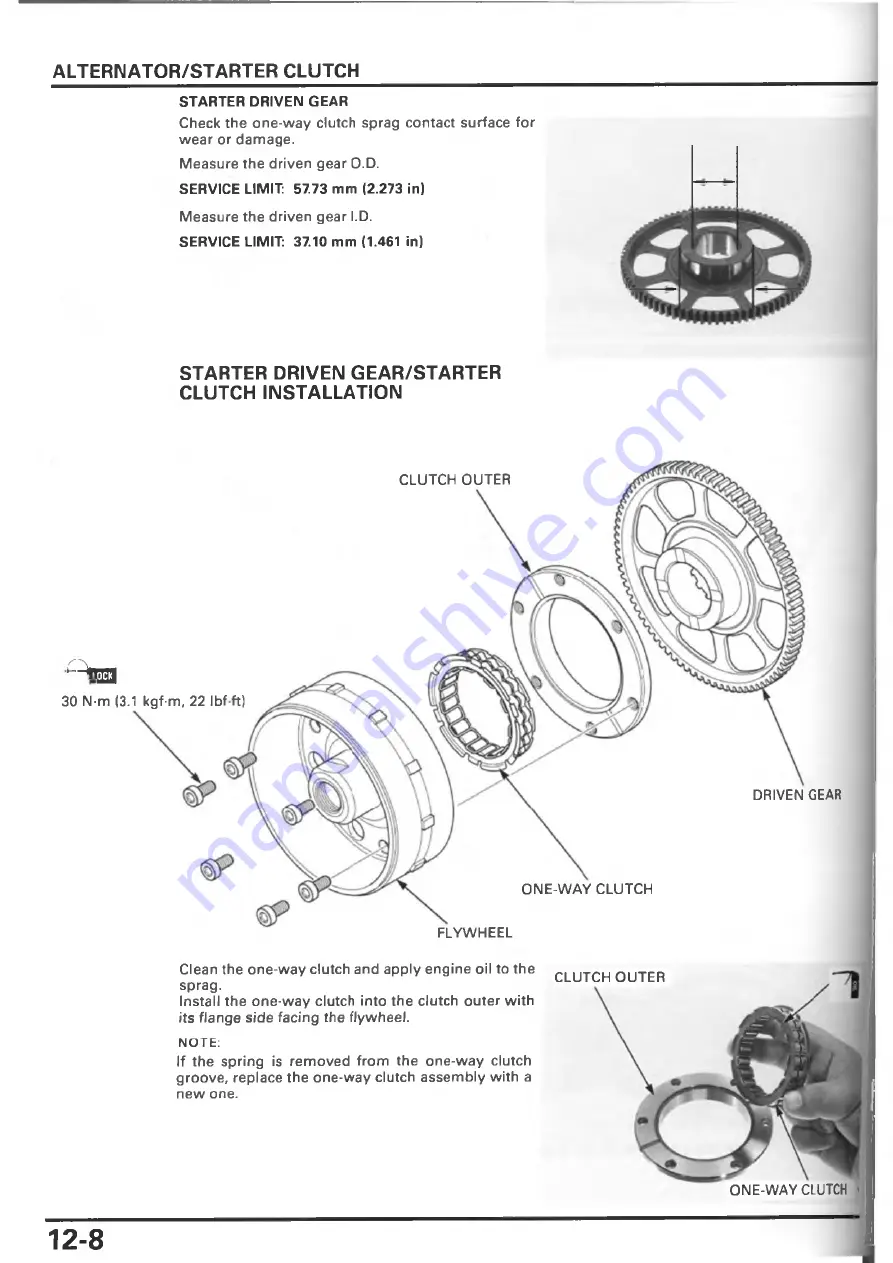
ALTERNATOR/STARTER CLUTCH
S T A R T E R D R IV E N G E A R
Check the one-way clutch sprag contact surface for
wear or damage.
Measure the driven gear O.D.
S E R V IC E LIMIT: 57.73 mm (2.273 in)
Measure the driven gear I.D.
S E R V IC E LIMIT: 37.10 mm (1.461 in)
STARTER DRIVEN GEAR/STARTER
CLUTCH INSTALLATION
CLUTCH OUTER
DRIVEN GEAR
ONE-WAY CLUTCH
FLYWHEEL
r\am
30 N-m (3.1 kgf-m, 22 Ibf ft)
Clean the one-way clutch and apply engine oil to the
sprag.
Install the one-way clutch into the clutch outer with
it s f la n g e s id e f a c in g t h e
flywheel.
NOTE:
If the spring is removed from the one-way clutch
groove, replace the one-way clutch assembly w ith a
new one.
ONE-WAY CLUTCH *
CLUTCH OUTER
12-8
Summary of Contents for NSA700A DN-1 2009
Page 1: ...7 2009...
Page 9: ...GENERAL INFORMATION EMISSION CONTROL INFORMATION LABEL...
Page 25: ...GENERAL INFORMATION 1 21...
Page 30: ...GENERAL INFORMATION FUEL TANK BREATHER HOSE FUEL TANK DRAIN HOSE FUEL HOSk t UPPER SIDE...
Page 31: ...GENERAL INFORMATION FUEL HOSE FUEL TANK DRAIN HOSE FUEL TANK BREATHER HOSE UPPER SIDE FUEL...
Page 32: ...GENERAL INFORMATION EXCEPT CALIFORNIA TYPE CALIFORNIA TYPE FUEL TANK 1 28...
Page 36: ...GENERAL INFORMATION 1 32...
Page 44: ...2 TECHNICAL FEATURE 2 HFT 2 2 2 1...
Page 127: ...FUEL SYSTEM PGM FI _________ COMPONENT LOCATION 6 2...
Page 203: ...COOLING SYSTEM SYSTEM FLOW PATTERN RESERVE TANK RADIATOR CAP RADIATOR WATER PUMP 7 2...
Page 221: ...ENGINE REMOVAL INSTALLATION COMPONENT LOCATION...
Page 234: ...CYLINDER HEAD VALVE________ COMPONENT LOCATION 23 N m 2 3 kgf m 17 Ibf ft...
Page 267: ...CYLINDER PISTON_____________ COMPONENT LOCATION...
Page 278: ...HFT COMPONENT LOCATION 11 2...
Page 279: ......
Page 395: ...ALTERNATOR STARTER CLUTCH COMPONENT LOCATION...
Page 425: ...FINAL DRIVE__________________ COMPONENT LOCATION 14 2...
Page 426: ...FINAL DRIVE...
Page 469: ...FRONT WHEEL SUSPENSION STEERING COMPONENT LOCATION 15 2...
Page 500: ...REAR WHEEL SUSPENSION...
Page 512: ...HYDRAULIC BRAKE COMPONENT LOCATION FRONT...
Page 513: ...HYDRAULIC BRAKE REAR 45 N m 4 6 kgf m 33 lbf ft PARKING 23 lbf ft 17 3...
Page 583: ...BATTERY CHARGING SYSTEM COMPONENT LOCATION REGULATOR RECTIFIER SYSTEM DIAGRAM MAIN FUSE 4 0 A...
Page 602: ...ELECTRIC STARTER COMPONENT LOCATION ENGINE STOP SWITCH SYSTEM DIAGRAM 21 2...
Page 619: ...LIGHTS METERS SWITCHES COMPONENT LOCATION RIGHT 22 2...