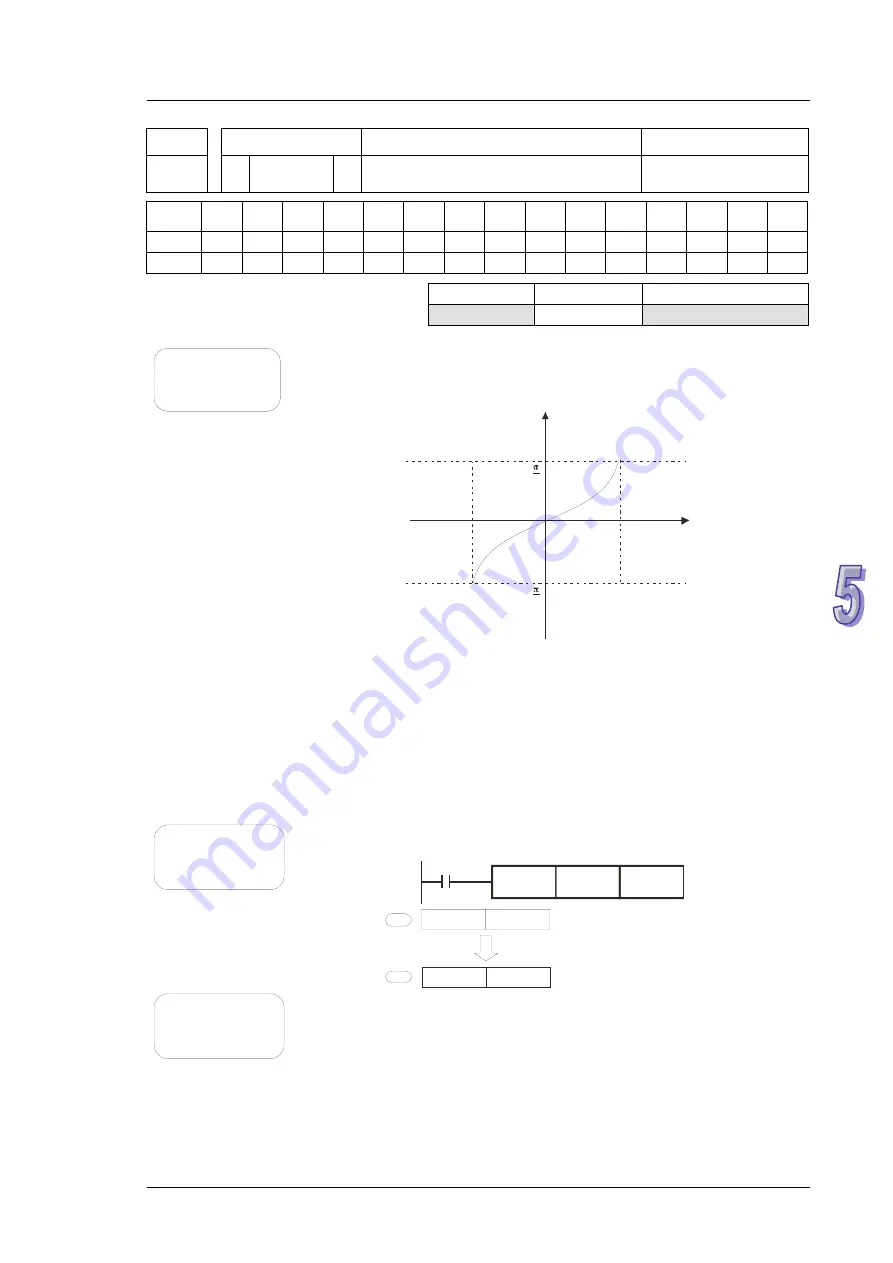
C h a p t e r 5 A p p l i e d I n s t r u c t i o n s
5 - 9 7
API
Instruction code
Operand
Function
133
D
ASIN
P
S, D
Arcsine of a binary
floating-point number
Device
X
Y
M
S
K
16#
F
KnM KnS
D
W
T
C
V
Z
S
D
Pulse instruction 16-bit instruction 32-bit instruction (6 steps)
–
E xp la nat io n
Arcsine
value=sin
-1
S
: Source value (binary floating-point value);
D
: Arcsine value
The relation between sine values and arcsine values is shown below.
R
S
2
2
-
0
1 ,0
-1 ,0
S: Sine va lu e
R: Arc sine v alue
The decimal floating-point value into which the sine value in
S
is
converted can only be in the range of -1.0 to +1.0. If it is not in the range,
the instruction will not be executed, an operation error flag will be ON,
and the error code 16#0E19 will appear.
If a conversion result is 0, a zero flag will be ON.
SM1064 is the zero flag in an Ox motion subroutine, and SM968 is the
zero flag in O100.
SM1049 is the operation error flag in an Ox motion subroutine, and
SM953 is the operation error flag in O100.
E xa mple
When X0.0 is ON, the arcsine of the binary floating-point value in (D1,
D0) is stored in (D11, D10).
X0.0
DASI N
D0
D10
Binary floating- point value
Binary floating- point value
D 1
D 0
S
D
D 11
D 10
Ar csine v alue
A dditio nal
re m ark
Please refer to section 5.3 for more information about performing
operations on floating-point numbers.
Summary of Contents for AH500
Page 9: ...viii...
Page 53: ...AH500 Motion Control Module Manual Wiring AH10PM 5A and a Yaskawa servo drive 2 32...
Page 55: ...AH500 Motion Control Module Manual Wiring AH10PM 5A and a Fuji servo drive 2 34...
Page 115: ...AH500 Motion Control Module Manual 4 16 MEMO...
Page 375: ...AH500 Motion Control Module Manual 5 260 MEMO...
Page 383: ...AH500 Motion Control Module Manual 6 8 MEMO...
Page 419: ...AH500 Motion Control Module Manual 7 36 MEMO...
Page 436: ...Chapter 8 Electronic Cam 8 17...
Page 483: ...AH500 Motion Control Module Manual 10 8 MEMO...
Page 505: ...AH500 Motion Control Module Manual 12 8 MEMO...
Page 515: ...AH500 Motion Control Module Manual 13 10 MEMO...
Page 544: ...Appendix A Error Code Table Table of Contents A 1 Error Code Table A 2 A 1...