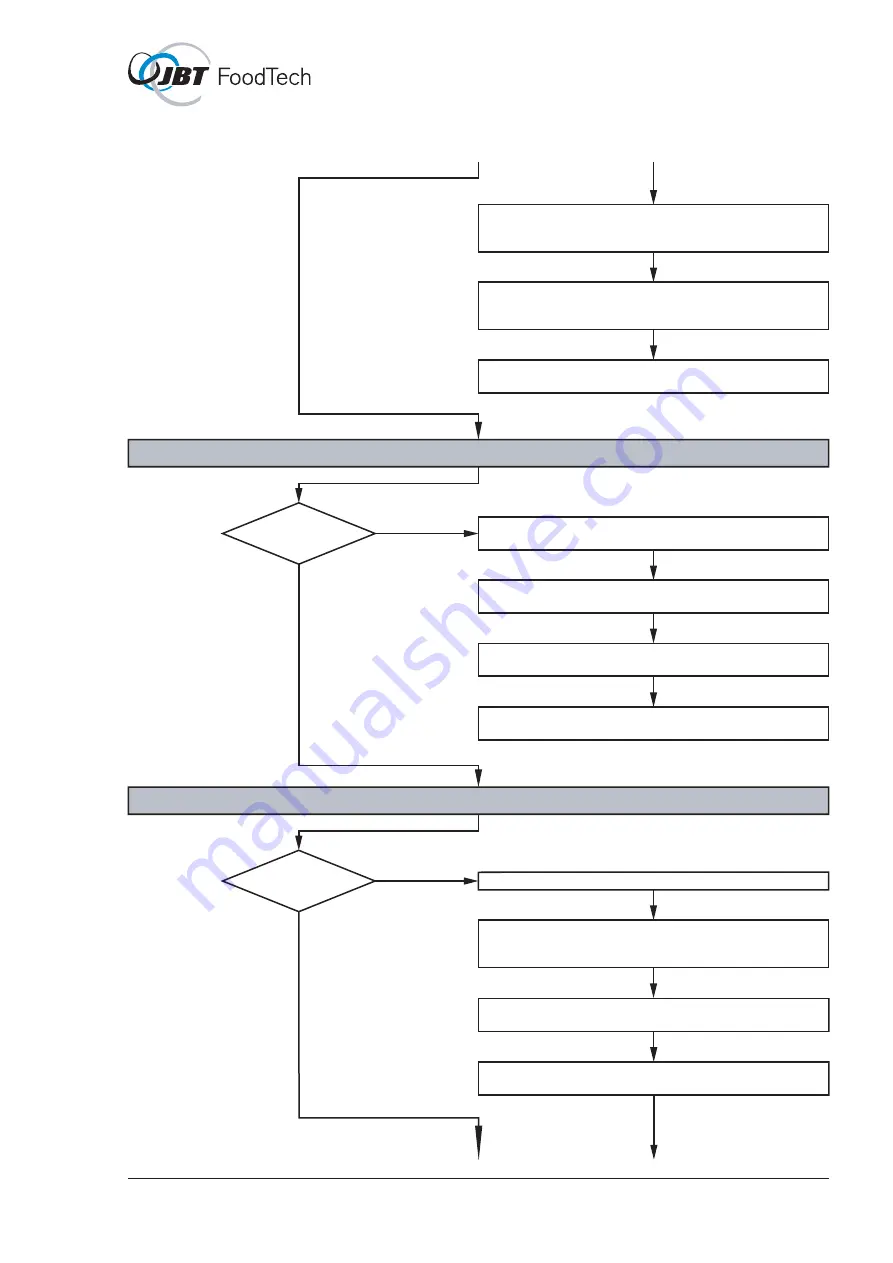
3
1000-07-01GB-25-01
INSTALLATION
INSTALLATION MANUAL
Check all the connections in the lubrication pump and in the
control panel.
Cable number = Page number in the drawings.
6. Limit switches
OK?
No
Yes
Check all the inputs on the PLC.
(The light is on if it is functioning OK.)
Check all the connections in the junction boxes and in
the control panel.
Look for loose wires on the relays and on the terminal blocks.
Cable number = Page number in the drawings.
If none of the above examples solved the problem:
Contact El-design support
7. Door heaters according to service info 221
OK?
No
Yes
Check the "pressure switch" by watching the input on
the PLC when the pump starts. When the pressure is correct,
the input light must be on.
If none of the above examples solved the problem:
Contact El-design support
Check that all the fuses are ON.
Check all the connections in the heater, junction boxes
and in the control panel.
Cable number = Page number in the drawings.
Check the air-temperature.
The heating must start at approxi7 ˚C.
If none of the above examples solved the problem:
Contact El-design support
Содержание FoodTech Frigoscandia GYRoCOMPACT M7
Страница 1: ...0 INSTALLATION MANUAL Frigoscandia GYRoCOMPACT M7 Spiral Freezer...
Страница 2: ...N...
Страница 4: ...INSTALLATION 2 2 INTRODUCTION 02 INSTALLATION MANUAL...
Страница 6: ...2 2 0000 07 01 01 00 INSTALLATION MANUAL INSTALLATION...
Страница 8: ...2 2 0000 07 01 02 00 INSTALLATION MANUAL INSTALLATION...
Страница 16: ...10 0000 00 01GB 11 24 SAFETY...
Страница 20: ...SAFETY 4 1000 07 01GB 02 03...
Страница 34: ...6 INSTALLATION PREPARATIONS 1000 07 01GB 05 03...
Страница 42: ...8 DELIVERY INFORMATION 0000 03 01GB 11 09...
Страница 44: ...2 INSTALLATION 1000 07 01GB 07 01 INSTALLATION MANUAL...
Страница 48: ...2 INSTALLATION 1000 07 01GB 09 03 INSTALLATION MANUAL...
Страница 54: ...2 INSTALLATION 1000 07 01GB 12 00 INSTALLATION MANUAL...
Страница 58: ...4 INSTALLATION 1000 07 01GB 13 01 INSTALLATION MANUAL...
Страница 62: ...2 INSTALLATION 1000 07 01GB 15 00 INSTALLATION MANUAL...
Страница 70: ...2 INSTALLATION INSTALLATION MANUAL 1000 07 01GB 18 01...
Страница 72: ...2 INSTALLATION 1000 07 01GB 20 00 INSTALLATION MANUAL...
Страница 78: ...6 INSTALLATION 1000 07 01GB 22 03 INSTALLATION MANUAL...
Страница 90: ...4 INSTALLATION 1000 07 01GB 29 00 INSTALLATION MANUAL...
Страница 110: ...6 INSTALLATION 1000 07 01GB 25 01 INSTALLATION MANUAL...
Страница 128: ...18 INSTALLATION 1000 07 01GB 26 06...
Страница 144: ...2 INSTALLATION 1000 07 01GB 19 00 INSTALLATION MANUAL...
Страница 152: ...2 INSTALLATION 1000 07 01GB 36 00 INSTALLATION MANUAL...
Страница 188: ...SERVICE INFORMATION SERVICE INFO NUMBER 127 EQUIPMENT GENERAL REVISED BY LAR REVISION DATE MAY 2012 14 127 01GB 04...
Страница 194: ...10 221 01GB 03 SERVICE INFO...
Страница 200: ...10 171 01GB 02 SERVICE INFO...
Страница 222: ...172 347 01GB 00 SERVICE INFO...
Страница 230: ...10 039 01GB 03 SERVICE INFORMATION...
Страница 256: ...172 CORRECTIVEMAINTENANCE 1000 06 01GB 10 11...
Страница 269: ...Automatic Pump Station PZC M1 PZE M2 CIP M3 Directions for use 3 19 EN...
Страница 277: ...9 ALTO Danmark A S...
Страница 288: ...2004 All rights reserved ALTO Danmark A S Blyt kkervej 2 DK 9100 Aalborg No 0617563C May 2004 Printed in Denmark...