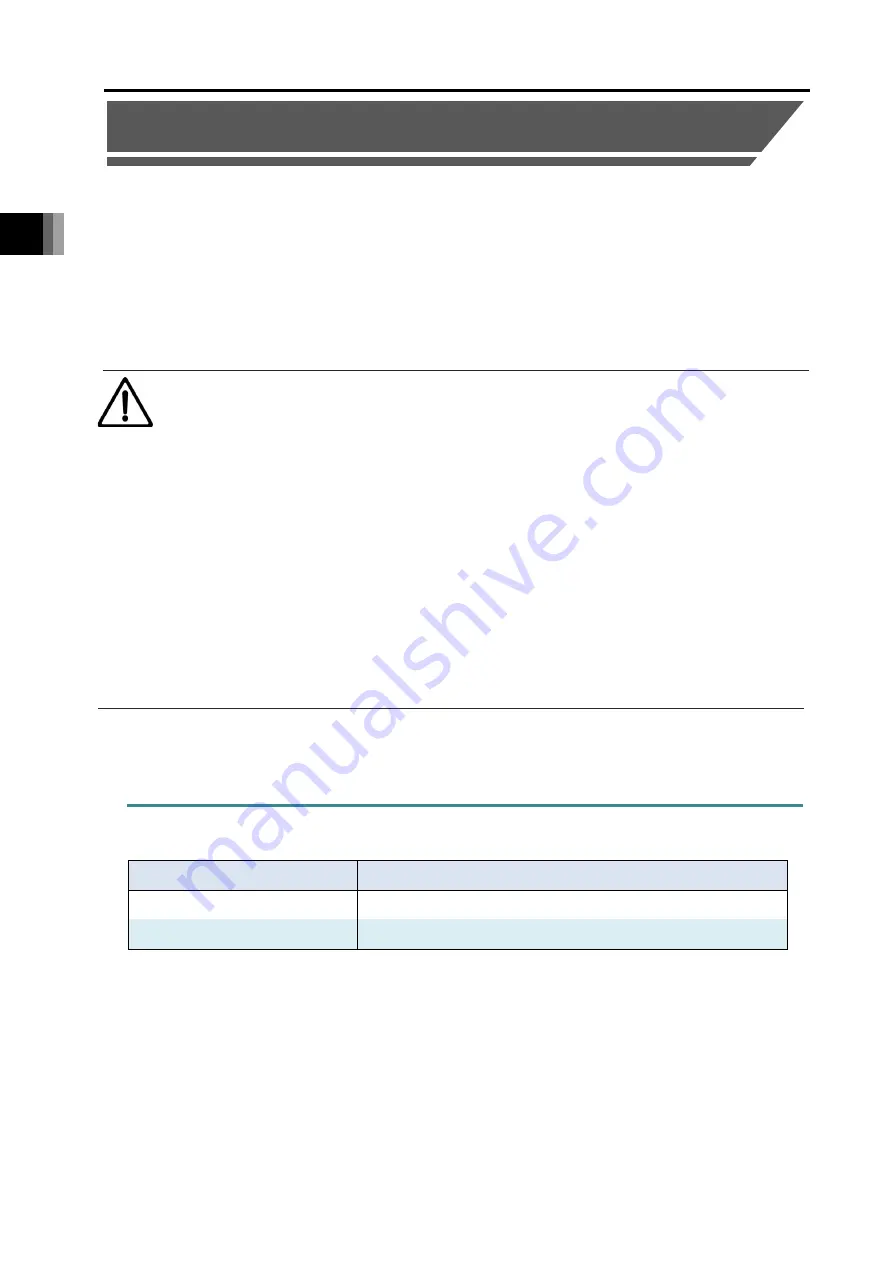
Chapter 2 System Configuration and Power Specifications
2.6
Drive-Source Cutoff
2-26
ME0392-4C
2.6 Drive-Source Cutoff
Although RSEL System is to get the motor power supplied from the SEL unit and the 200V power
supply unit, the drive cutoff circuit is installed in the driver unit.
Each driver unit possesses a drive cutoff circuit by the semiconductor. The motor power supply
should be cut off by STOP Signal. The drive source cutoff circuit via semiconductor has a high-
side overcurrent detection function and an inrush current restriction function.
Caution
●
The drive cutoff semiconductor relay mounted on IAI controllers is assumed in
frequency of only limited use such as the case that an emergency stop of the device is
needed, thus it is not assumed to activate frequently. Therefore, in case of high
frequency of use of the drive cutoff relay such as switching on and off of the drive
source repeatedly every time of setup change, the semiconductor may come to the end
of life in early timing.
●
The number of on/off operation cycles should be approximately 5 times at the most in
one day for reference. Also, leave it for approximately 30 minutes for cooling time after
the drive cutoff.
●
Construct a circuit that STOP Signal for the system IO connector gets turned on and off
at the same time as the drive power supply turned on and off for RCON-SC-1 (RCON-
PS2-3).
2.6.1 Drive-source cutoff circuit specifications
[Electrical Specifications]
Item
Specification
STOPIN Input, ENBIN Input
24V DC±10
%
/ 10mA or less
S1, S2
24V DC±10
%
/ 0.1A or less
Содержание R-unit RSEL
Страница 2: ......
Страница 5: ...ME0392 4C 2 Quick Start Guide Japanese Only ...
Страница 32: ...Actuator Coordinate System Intro 18 ME0392 4C 2 Slider type 3 Table type 0 0 0 0 ...
Страница 50: ...Chapter 1 RSEL System 1 4 Installation 1 13 ME0392 4C ...
Страница 82: ...Chapter 2 System Configuration and Power Specifications 2 6 Drive Source Cutoff 2 30 ME0392 4C ...
Страница 244: ...Chapter 4 Unit connection Installation and Wiring 4 5 PIO Circuit 4 32 ME0392 4C ...
Страница 249: ...Chapter 4 Unit connection Installation and Wiring 4 7 Brake Box Option ME0392 4C 4 37 Appearance ...
Страница 251: ...Chapter 4 Unit connection Installation and Wiring 4 7 Brake Box Option ME0392 4C 4 39 Appearance ...
Страница 316: ...Chapter 5 Operation 5 10 ELECYLINDER Operation 5 52 ME0392 4C ...
Страница 438: ...Chapter 6 Field Network PIO SIO 6 5 Example of Connectivity Setting 6 120 ME0392 4C ...
Страница 472: ...Chapter 7 6 axis Cartesian Robot 7 2 Caution When Using Orthogonal Coordinate System Features 7 33 ME0392 4C ...
Страница 530: ...Chapter 9 Special Functions 9 6 RSEL Serial Communication Multiple Channel Applicable Features 9 38 ME0392 4C ...
Страница 532: ...10 6 Servo Gain Adjustment 10 90 10 7 Parameter Configuration Advanced Use 10 93 ...
Страница 638: ...Chapter 10 Parameter 10 7 Parameter Configuration Advanced Use 10 106 ME0392 4C ...
Страница 838: ...Chapter 14 Warranty 14 Warranty 14 3 ME0392 4C ...
Страница 843: ......
Страница 844: ......