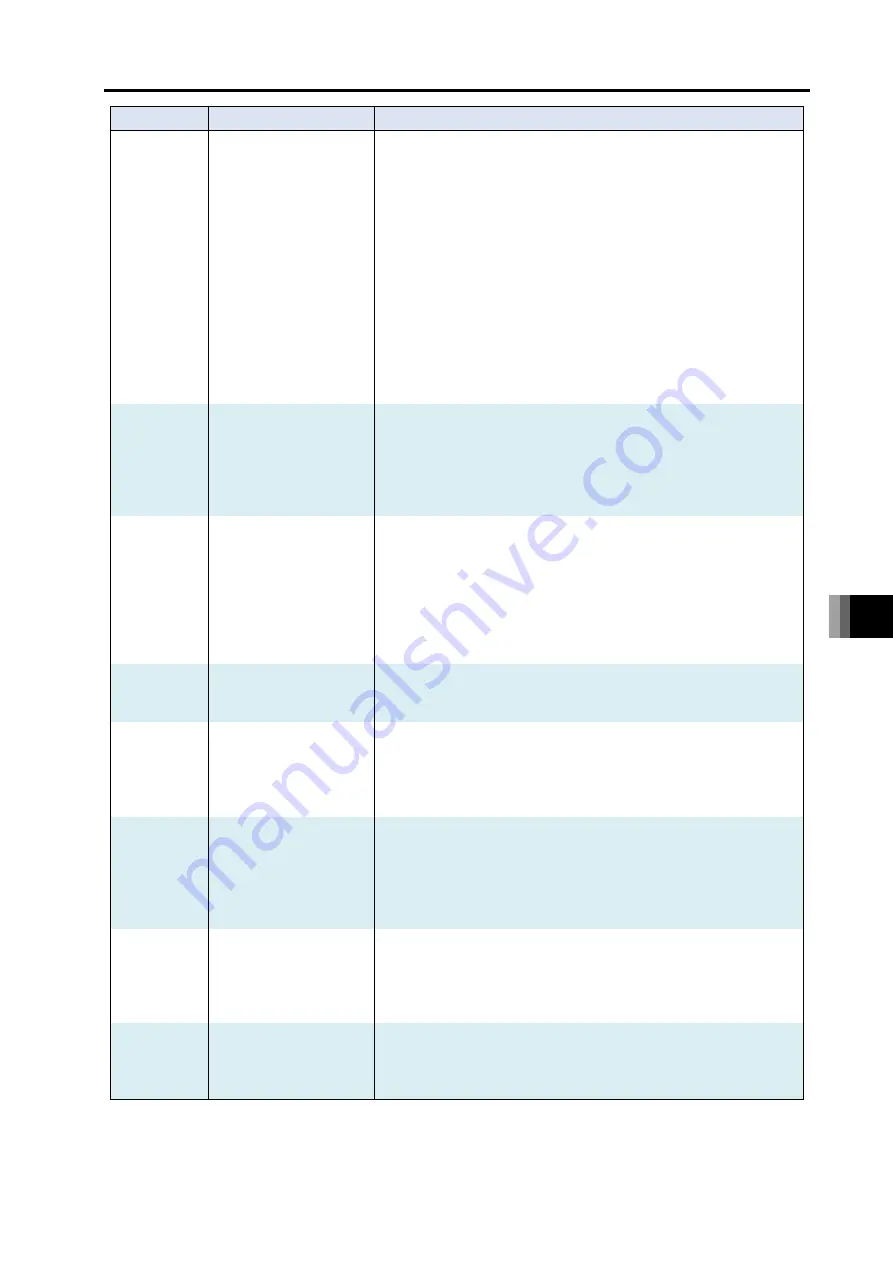
Chapter
11 T
roubleshooting
11.4 Alarm Codes of Driver Unit
11-83
ME0392-4C
Alarm code
Alarm name
Causes/countermeasures
0E5
P, A, S
Driver limited
Encoder reception error
Cause: Data from the encoder was not normally received by the driver
unit.
1) Encoder cable line breakage or connector connection
failure (when the detail code in the teaching tool alarm list is
0002H)
2) Influence from noise (Detail code 0001H).
3) Actuator internal part malfunction (communication part).
4) Driver unit internal part malfunction (communication part).
[Only for P Driver]
5) Initialization of battery-less absolute encoder incomplete
(Detail code 000AH)
6) Communication error occurred to battery-less absolute
encoder
(Detail code 000CH)
Countermeasure: 1) Check for any wire breakage on a connector and
inspect the condition of the wire connections.
2) Try turning OFF power to all peripheral devices
and moving only the driver unit and actuator. If no
error is generated, the culprit may be noise. Take
measures against noise.
In case of 3), 4) or 5), replace the actuator (motor
part) and/or the driver unit.
6) Check the encoder cable line breakage and
connection at connectors.
For the high-resolution
battery-less absolute encoder, check the capacity
of the 24V DC power source and connection at
the power supply cables.
Contact IAI if the cause cannot be determined.
0E6
P, A, S
Driver limited
Encoder count error
Cause: The encoder cannot detect location information properly.
1) Disconnection of the encoder relay cable or actuator side
attached cable, or connector connection failure.
2) Failure of the encoder itself.
3) An error response status was received during initial
communication with battery-less absolute encoder.
Countermeasure: 1) Check for any wire breakage on a connector and
inspect the condition of the wire connections.
If there is no cable malfunction, encoder failure may
be possible. Contact IAI.
0E7
S
Driver limited
A-, B- and Z-phase wire
breaking
Cause: Encoder signals cannot be detected correctly.
1) The encoder relay cable or supplied actuator cable is
disconnected or its connector is not plugged in correctly.
2) The encoder itself is faulty.
Countermeasure: 1) Check if any wire breakage on a connector and
the condition of wire connections.
If the cables are normal, faulty encoder is
suspected. Please contact IAI.
11.4 Alarm Codes of Driver Unit
ME0392-4C
11-84
Alarm code
Alarm name
Causes/countermeasures
0E8
P, A, D
Driver limited
A- and B-phase
disconnection
Cause: The encoder signal cannot be detected normally.
1) Disconnection of the actuator connection cable, actuator
side attached cable, or connector connection failure.
2) Failure of the encoder itself.
3) Disconnected axis parameter No. 158 “Enabled/Disabled
Axis Select” is 0: Enabled.
Countermeasure: 1) Check for any wire breakage on a connector and
inspect the condition of the wire connections.
2) If there is no cable malfunction, encoder failure
may be possible. Contact IAI.
3) Parameter No. 158 “Enabled/Disabled Axis
Select” 1: Disabled.
* When the actuator is not connected, this alarm is
generated just by setting the reserved axis in the
gateway parameter configuration tool or setting
the driver unit to “Not set”.
0EB
P, A
Driver limited
Battery-less Absolute
Encoder error detected
Cause: Battery-less absolute encoder cannot detect location
information normally.
Countermeasure: Check for any wire breakage on a connector and
inspect the condition of the wire connections.
If there is no cable malfunction, encoder failure may
be possible. Contact IAI.
0EC
D
Driver limited
PS-phase disconnection
Cause: The encoder signal cannot be detected normally.
1) Disconnection of the actuator connection cable, actuator
side attached cable, or connector connection failure.
2) Failure of the encoder itself.
Countermeasure: 1) Check for any wire breakage on a connector and
inspect the condition of the wire connections.
If there is no cable malfunction, encoder failure
may be possible. Contact IAI.
0F0
A, D
Driver limited
Driver logic error
Cause: Excessive load, parameter (motor type) mismatch, noise,
RSEL system failure, etc.
Countermeasure: Contact IAI.
0F4
P, A
Driver limited
PCB mismatch
Cause: The circuit board is not supported by the connection motor at
startup check.
There may be a mismatch between the actuator and driver
unit. Check the model numbers.
Countermeasure: Contact IAI if this error occurs.
0F5
S
Driver limited
Non-volatile memory write
verify error
Cause: When data is written to the non-volatile memory, comparison
(verification) is performed to confirm whether the data in the
memory matches the write data. At this time, a mismatch was
detected. (Failure of non-volatile memory)
Countermeasure: Contact IAI if this reoccurs even after turning ON
the power again.
0F6
Non-volatile memory write
timeout
Cause: There is no response within the specified time during the data
writing to the non-volatile memory. (Failure of non-volatile
memory)
Countermeasure: Contact IAI if this reoccurs even after turning ON
the power again.
0F8
Non-volatile memory data
destruction
Cause: Abnormal data was detected by non-volatile memory check at
startup. (Failure of non-volatile memory)
Countermeasure: Contact IAI if this reoccurs even after turning ON
the power again.
Содержание R-unit RSEL
Страница 2: ......
Страница 5: ...ME0392 4C 2 Quick Start Guide Japanese Only ...
Страница 32: ...Actuator Coordinate System Intro 18 ME0392 4C 2 Slider type 3 Table type 0 0 0 0 ...
Страница 50: ...Chapter 1 RSEL System 1 4 Installation 1 13 ME0392 4C ...
Страница 82: ...Chapter 2 System Configuration and Power Specifications 2 6 Drive Source Cutoff 2 30 ME0392 4C ...
Страница 244: ...Chapter 4 Unit connection Installation and Wiring 4 5 PIO Circuit 4 32 ME0392 4C ...
Страница 249: ...Chapter 4 Unit connection Installation and Wiring 4 7 Brake Box Option ME0392 4C 4 37 Appearance ...
Страница 251: ...Chapter 4 Unit connection Installation and Wiring 4 7 Brake Box Option ME0392 4C 4 39 Appearance ...
Страница 316: ...Chapter 5 Operation 5 10 ELECYLINDER Operation 5 52 ME0392 4C ...
Страница 438: ...Chapter 6 Field Network PIO SIO 6 5 Example of Connectivity Setting 6 120 ME0392 4C ...
Страница 472: ...Chapter 7 6 axis Cartesian Robot 7 2 Caution When Using Orthogonal Coordinate System Features 7 33 ME0392 4C ...
Страница 530: ...Chapter 9 Special Functions 9 6 RSEL Serial Communication Multiple Channel Applicable Features 9 38 ME0392 4C ...
Страница 532: ...10 6 Servo Gain Adjustment 10 90 10 7 Parameter Configuration Advanced Use 10 93 ...
Страница 638: ...Chapter 10 Parameter 10 7 Parameter Configuration Advanced Use 10 106 ME0392 4C ...
Страница 838: ...Chapter 14 Warranty 14 Warranty 14 3 ME0392 4C ...
Страница 843: ......
Страница 844: ......