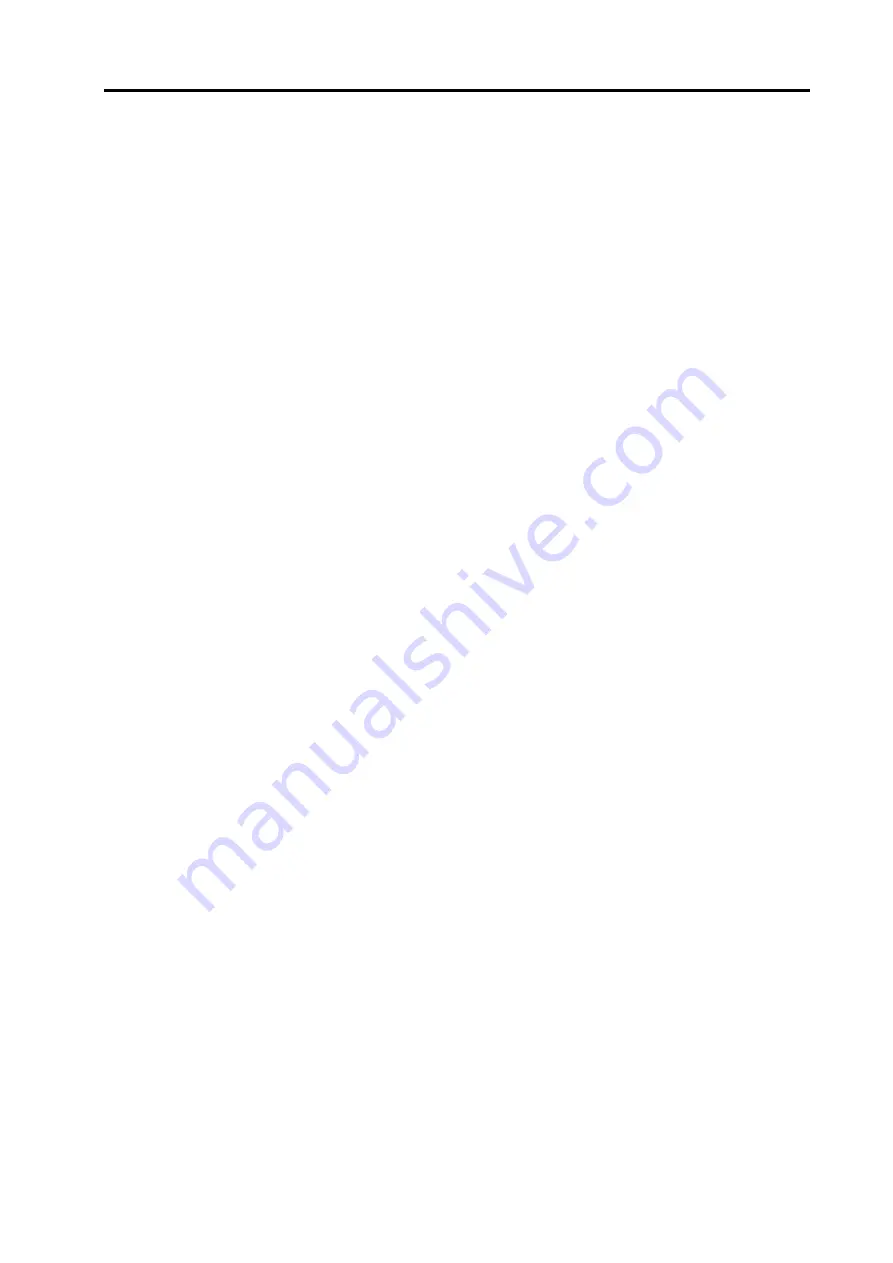
Precautions for Handling
Intro-8
ME0392-4C
Precautions for Handling
1. Make sure to follow the usage condition, environment and specification range of the product.
In case it is not secured, it may cause a drop in performance or malfunction of the product.
2. Use the correct teaching tool.
Refer to the following item and use compatible tools for PC software and teaching pendant
usable for RSEL system.
Refer to [2.1.6 Teaching tool (Option)]
3. Back up data in order to be prepared for a breakdown.
This system possesses a save area in the hold memory and a save area in the flash memory.
Transferring data to the PC software or a teaching pendant enables only to write it in the
memory and the data should be deleted when the power is turned off or the controller is reset. In
order to certainly store data, the data that you would prefer to save should be written in the flash
memory.
Refer to [5.7.6 Memory map]
Also, keep the data updated to the latest so recovery process can be rapidly carried out when it
is necessary to replace this controller with a substitute in case such as malfunction.
How to save
(1) To save data to an external memory device or hard disk via a teaching tool such as the PC
software.
(2) Record position table and parameters in writing
4. Perform initial operation setting.
This controller complies with seven types of field networks and PIO controls.
Establish settings suitable to the system to use at the startup.
Refer to [Chapter 6 Field Network, PIO, SIO]
Warning
●
It is dangerous if operation settings of the control sequence and field network are not
matched, as it will not only prevent normal operation but can also lead to unpredictable
operation.
Precautions for Handling
ME0392-4C
Intro-9
5. Calendar function time setting
Therefore may be a case that “Error Code 202 Calendar Features Error” gets generated at the
first time of turning the power on after delivery. In that case, set the current time with the
teaching tool.
When fully charged, time data can be retained approximately 10 days after the power is turned
OFF.
At shipment, time will be set but the unit will not be fully charged. Therefore, even if the above-
mentioned number of days has not passed from shipment, the time data may be lost.
6. Be careful of rubbing or twisting when using the through hole of the rotary actuator.
If using a rotary actuator with rotational center through hole, with cables, etc. inserted to the
through hole, take measures against wear due to rubbing, or wire disconnection due to twisting.
Be particularly cautious if the actuator is 360-degree specification, as it can infinitely rotate in the
same direction.
7. There are restrictions on index mode operation of the rotary actuator.
With use of Driver unit Parameter No. 79 "Rotary Axis Mode Select", rotary actuators with 360-
degree specification allow selection of normal mode which provides limited rotation operation, or
index mode which enables multi-rotation control.
Refer to [Chapter 10 Parameter]
The index mode has the following restrictions.
(1) In jog or inching operation using teaching tools such as PC software, etc., the one-time
command range enables a maximum of 360° in jog operation, or 1° in inching operation.
(2) Pushing cannot be performed. For push torque, settings other than 0 cannot be made.
(3) Do not repetitively execute positioning commands around 0 degree numerous times while
traveling in the vicinity of 0 degree. The rotation direction may switch, or operation may
become unstable.
(4) Software stroke limit is disabled in index mode.
Содержание R-unit RSEL
Страница 2: ......
Страница 5: ...ME0392 4C 2 Quick Start Guide Japanese Only ...
Страница 32: ...Actuator Coordinate System Intro 18 ME0392 4C 2 Slider type 3 Table type 0 0 0 0 ...
Страница 50: ...Chapter 1 RSEL System 1 4 Installation 1 13 ME0392 4C ...
Страница 82: ...Chapter 2 System Configuration and Power Specifications 2 6 Drive Source Cutoff 2 30 ME0392 4C ...
Страница 244: ...Chapter 4 Unit connection Installation and Wiring 4 5 PIO Circuit 4 32 ME0392 4C ...
Страница 249: ...Chapter 4 Unit connection Installation and Wiring 4 7 Brake Box Option ME0392 4C 4 37 Appearance ...
Страница 251: ...Chapter 4 Unit connection Installation and Wiring 4 7 Brake Box Option ME0392 4C 4 39 Appearance ...
Страница 316: ...Chapter 5 Operation 5 10 ELECYLINDER Operation 5 52 ME0392 4C ...
Страница 438: ...Chapter 6 Field Network PIO SIO 6 5 Example of Connectivity Setting 6 120 ME0392 4C ...
Страница 472: ...Chapter 7 6 axis Cartesian Robot 7 2 Caution When Using Orthogonal Coordinate System Features 7 33 ME0392 4C ...
Страница 530: ...Chapter 9 Special Functions 9 6 RSEL Serial Communication Multiple Channel Applicable Features 9 38 ME0392 4C ...
Страница 532: ...10 6 Servo Gain Adjustment 10 90 10 7 Parameter Configuration Advanced Use 10 93 ...
Страница 638: ...Chapter 10 Parameter 10 7 Parameter Configuration Advanced Use 10 106 ME0392 4C ...
Страница 838: ...Chapter 14 Warranty 14 Warranty 14 3 ME0392 4C ...
Страница 843: ......
Страница 844: ......