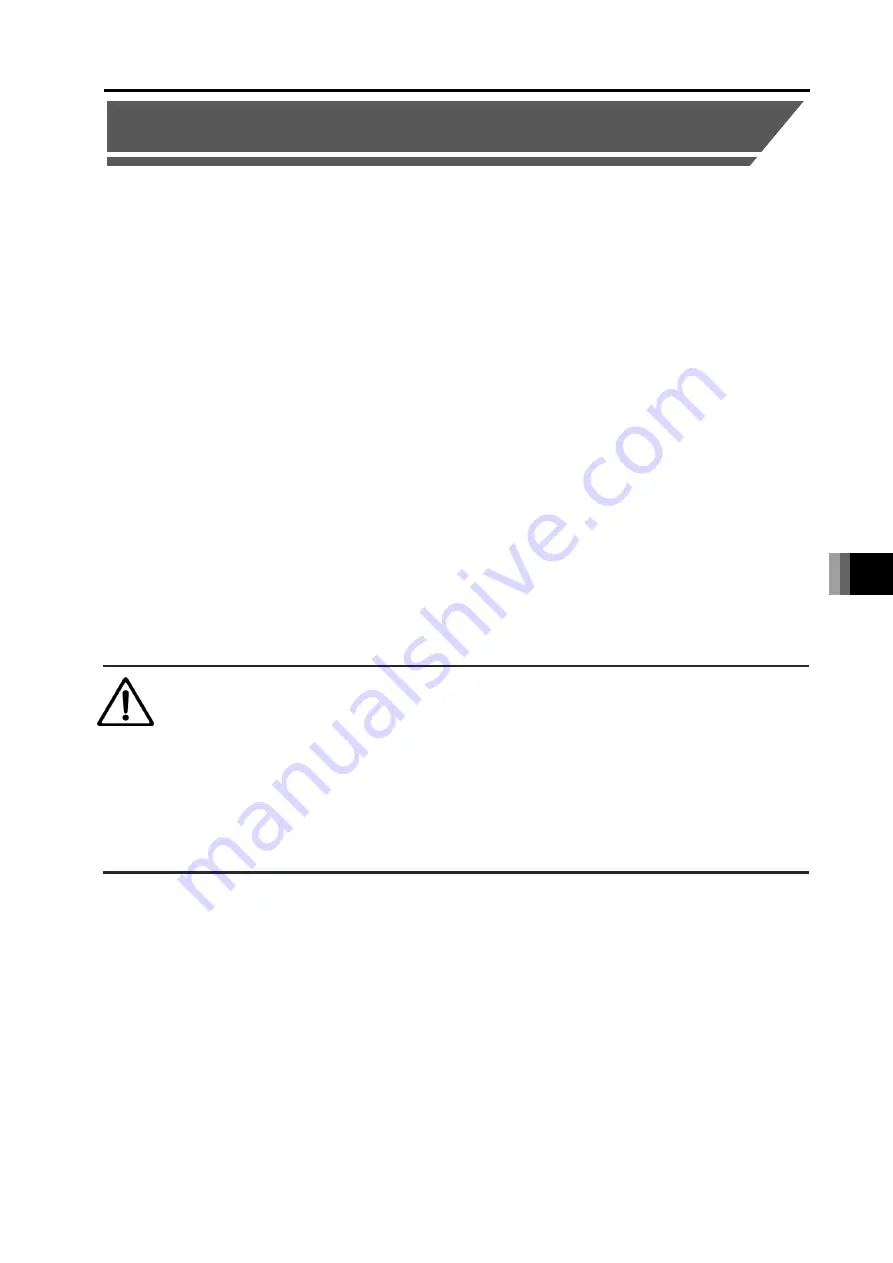
Chapter 10 Parameter
10.6 Servo Gain Adjustment ·········································· 10-90
10.7 Parameter Configuration (Advanced Use) ·················· 10-93
10.1 Overview
ME0392-4C
10-1
10.1 Overview
Parameter data should be set appropriately according to the application requirements. When a
change is required to the parameters, make sure to back up the data before the change so the
settings can be returned anytime.
With the PC software, it is available to have a backup in a PC. With a teaching pendant, it is
available to have a backup in a Secure Digital memory card.
Also, for the purpose of rapid recovery after the investigation of failure unit or replacing the
controller, keep data backup or memo also after the parameter change.
The change to the parameters will be activated after they are edited, written to the flash ROM,
then either software reset or reboot of the power. It will not be active only with writing on the
teaching tool.
The initial settings (reference) described in the tables in the sections from 6.1 I/O Parameters to
6.7 Other Parameters differ depending of the actuator.
The input ranges are the limitations for the input in the teaching pendant and PC software. For
the actual setting, input the values defined in the remarks.
The values other than those defined in the remarks are for the system reservation. Do not
attempt to input the values other than those defined in the remarks.
Warning
Establishment of parameter setting gives a great influence to operation.
Wrongly established setting could cause not only an operation error or malfunction, but
also it is very dangerous.
Settings at the delivery enable the product to operate standardly.
Understand very well about the control logic of controller if making a change or performing
a setting suitable to the system. Please contact us if you have anything unclear.
Do not turn off the power to the controller during the parameter writing.
Содержание R-unit RSEL
Страница 2: ......
Страница 5: ...ME0392 4C 2 Quick Start Guide Japanese Only ...
Страница 32: ...Actuator Coordinate System Intro 18 ME0392 4C 2 Slider type 3 Table type 0 0 0 0 ...
Страница 50: ...Chapter 1 RSEL System 1 4 Installation 1 13 ME0392 4C ...
Страница 82: ...Chapter 2 System Configuration and Power Specifications 2 6 Drive Source Cutoff 2 30 ME0392 4C ...
Страница 244: ...Chapter 4 Unit connection Installation and Wiring 4 5 PIO Circuit 4 32 ME0392 4C ...
Страница 249: ...Chapter 4 Unit connection Installation and Wiring 4 7 Brake Box Option ME0392 4C 4 37 Appearance ...
Страница 251: ...Chapter 4 Unit connection Installation and Wiring 4 7 Brake Box Option ME0392 4C 4 39 Appearance ...
Страница 316: ...Chapter 5 Operation 5 10 ELECYLINDER Operation 5 52 ME0392 4C ...
Страница 438: ...Chapter 6 Field Network PIO SIO 6 5 Example of Connectivity Setting 6 120 ME0392 4C ...
Страница 472: ...Chapter 7 6 axis Cartesian Robot 7 2 Caution When Using Orthogonal Coordinate System Features 7 33 ME0392 4C ...
Страница 530: ...Chapter 9 Special Functions 9 6 RSEL Serial Communication Multiple Channel Applicable Features 9 38 ME0392 4C ...
Страница 532: ...10 6 Servo Gain Adjustment 10 90 10 7 Parameter Configuration Advanced Use 10 93 ...
Страница 638: ...Chapter 10 Parameter 10 7 Parameter Configuration Advanced Use 10 106 ME0392 4C ...
Страница 838: ...Chapter 14 Warranty 14 Warranty 14 3 ME0392 4C ...
Страница 843: ......
Страница 844: ......