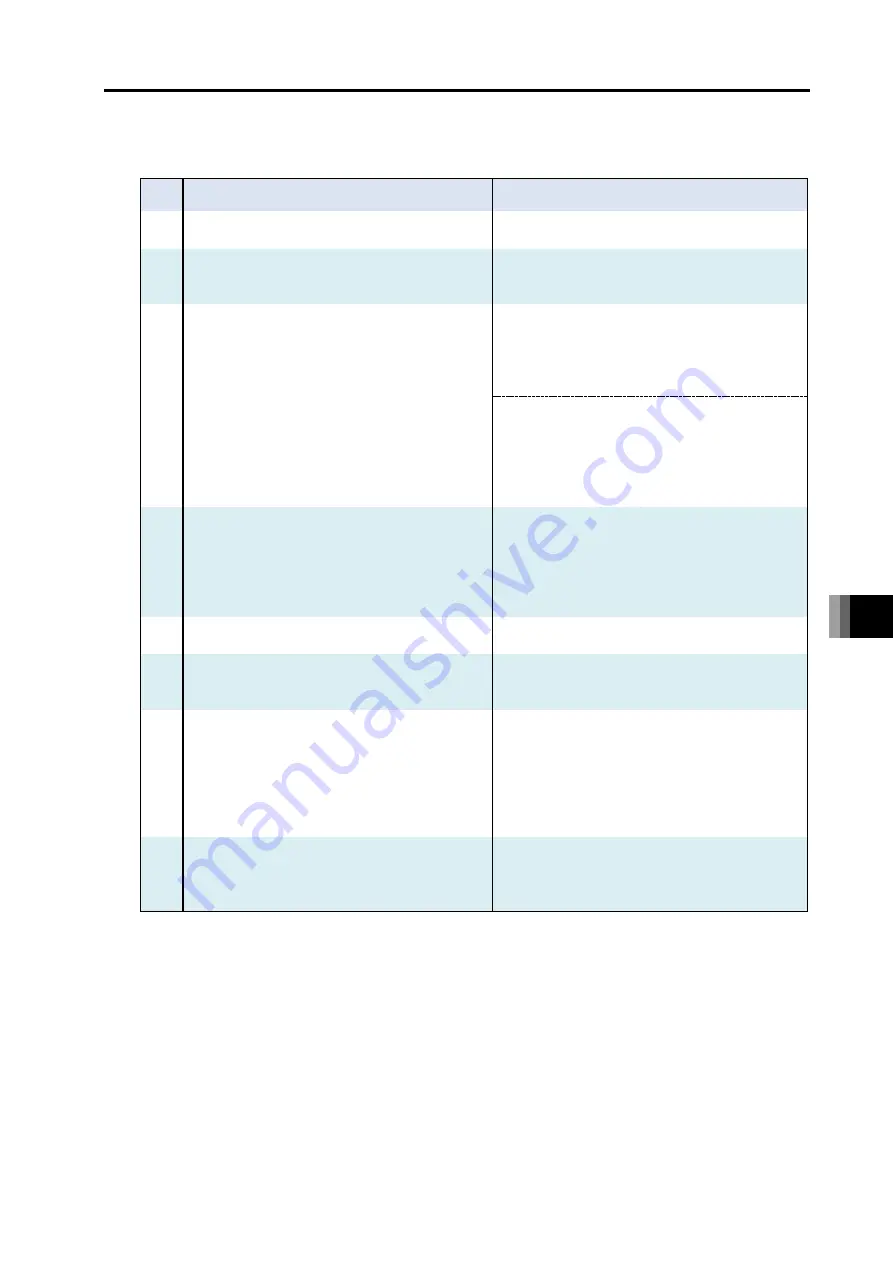
Chapter
11 T
roubleshooting
11.5 Causes and Countermeasures for ELECYLINDER Alarms
11-87
ME0392-4C
11.5.2 Troubleshooting for ELECYLINDER alarm groups
ELECYLINDER alarms are classified into “alarms” and “warnings” depending on the content.
“Alarms” are grouped into 5 types.
Alarm
level
SV/ALM
LED
* ALM
signal
Situation
when
generated
Clearing method
Alarm
Red ON
OFF
Servo OFF
after gradual
stop
Cleared by resetting the alarm.
If it cannot be cleared by resetting the
alarm, turn off the power, then turn it
on again.
Warning
Red/green
alternate
blinking
ON
Continued
operation
● Maintenance
Warnings 1/2
(Total travel count/Total travel
distance) are cleared by updating the
set values in the maintenance
information window.
● Maintenance Warning 3 (Overload
warning) is cleared by resetting the
alarm.
Caution
●
Clear alarms only after investigating and resolving the cause.
●
If the same alarm recurs after clearance, it is highly probable that the cause of the alarm
has not been resolved.
●
If the cause of the alarm cannot be resolved or the alarm cannot be cleared after
resolving the cause, contact IAI.
●
Set to the disable status on the deadman’s switch in the teaching pendant, and
ELECYLINDER gets to the motor voltage drop condition (teaching pendant alarm: 203).
11.5 Causes and Countermeasures for ELECYLINDER Alarms
ME0392-4C
11-88
[Alarm group A: Overload alarm]
Moving parts of ELECYLINDER stopped abnormally while moving to the target position.
No.
Cause
Countermeasure
1
Operation may not be possible due to contact
with or snagging on external obstacles.
Remove any external obstacles or other external
loads.
2
The ELECYLINDER may be being used under
conditions exceeding the specifications
described in the catalog.
Check the specification values such as payload,
acceleration/deceleration and speed, and adjust
them appropriately.
3
Causes may include foreign matter, brake failure
or motor failure.
Visually check for the depletion of grease on the
ball screw/guide inside the ELECYLINDER,
intrusion of foreign matter, etc.
If this is the case, clean the inside of the
ELECYLINDER and replenish the grease.
Remove the motor and check the sliding
movement of the ELECYLINDER body.
If there is no abnormality in the sliding motion,
there is a possibility of motor or brake failure.
Replacement of the motor is recommended.
4
The base may have been distorted when
mounting the ELECYLINDER, increasing the
sliding resistance of the guide.
The ELECYLINDER mounting surface should be
a machined surface or a plane with similar
accuracy, with flatness within 0.05mm/m.
Refer to the [Instruction manual of each
ELECYLINDER] for the recommended tightening
torque of the bolt for fixing the base.
5
The peak power capacity of the 24V power
supply is less than 4.2A.
Use a power supply with peak current of 4.2 A or
higher (per axis).
6
As there is a contact error at the terminals on the
EC connection unit cable, the peak current would
not flow.
Check if there is any looseness, contact error or
line breakage on the terminals or connectors of
the EC connection unit cable.
7
The deceleration distance was insufficient and
the calculation result of the arrival position
exceeded the operation range of the
ELECYLINDER due to the “next movement
command
”
being issued too soon during
operation with “Smooth accel/decel setting
”
enabled.
Adjust the timing of the “next movement
command
”
so that the command will be given
after the first movement is completed.
8
24V power was turned ON while the moving
parts of the ELECYLINDER were immobilized or
pressed against the mechanical stopper.
Resolve the state of immobilization.
If the unit is pressed against the mechanical
stopper, move it at least 5 mm away, then turn on
the power again.
Содержание R-unit RSEL
Страница 2: ......
Страница 5: ...ME0392 4C 2 Quick Start Guide Japanese Only ...
Страница 32: ...Actuator Coordinate System Intro 18 ME0392 4C 2 Slider type 3 Table type 0 0 0 0 ...
Страница 50: ...Chapter 1 RSEL System 1 4 Installation 1 13 ME0392 4C ...
Страница 82: ...Chapter 2 System Configuration and Power Specifications 2 6 Drive Source Cutoff 2 30 ME0392 4C ...
Страница 244: ...Chapter 4 Unit connection Installation and Wiring 4 5 PIO Circuit 4 32 ME0392 4C ...
Страница 249: ...Chapter 4 Unit connection Installation and Wiring 4 7 Brake Box Option ME0392 4C 4 37 Appearance ...
Страница 251: ...Chapter 4 Unit connection Installation and Wiring 4 7 Brake Box Option ME0392 4C 4 39 Appearance ...
Страница 316: ...Chapter 5 Operation 5 10 ELECYLINDER Operation 5 52 ME0392 4C ...
Страница 438: ...Chapter 6 Field Network PIO SIO 6 5 Example of Connectivity Setting 6 120 ME0392 4C ...
Страница 472: ...Chapter 7 6 axis Cartesian Robot 7 2 Caution When Using Orthogonal Coordinate System Features 7 33 ME0392 4C ...
Страница 530: ...Chapter 9 Special Functions 9 6 RSEL Serial Communication Multiple Channel Applicable Features 9 38 ME0392 4C ...
Страница 532: ...10 6 Servo Gain Adjustment 10 90 10 7 Parameter Configuration Advanced Use 10 93 ...
Страница 638: ...Chapter 10 Parameter 10 7 Parameter Configuration Advanced Use 10 106 ME0392 4C ...
Страница 838: ...Chapter 14 Warranty 14 Warranty 14 3 ME0392 4C ...
Страница 843: ......
Страница 844: ......