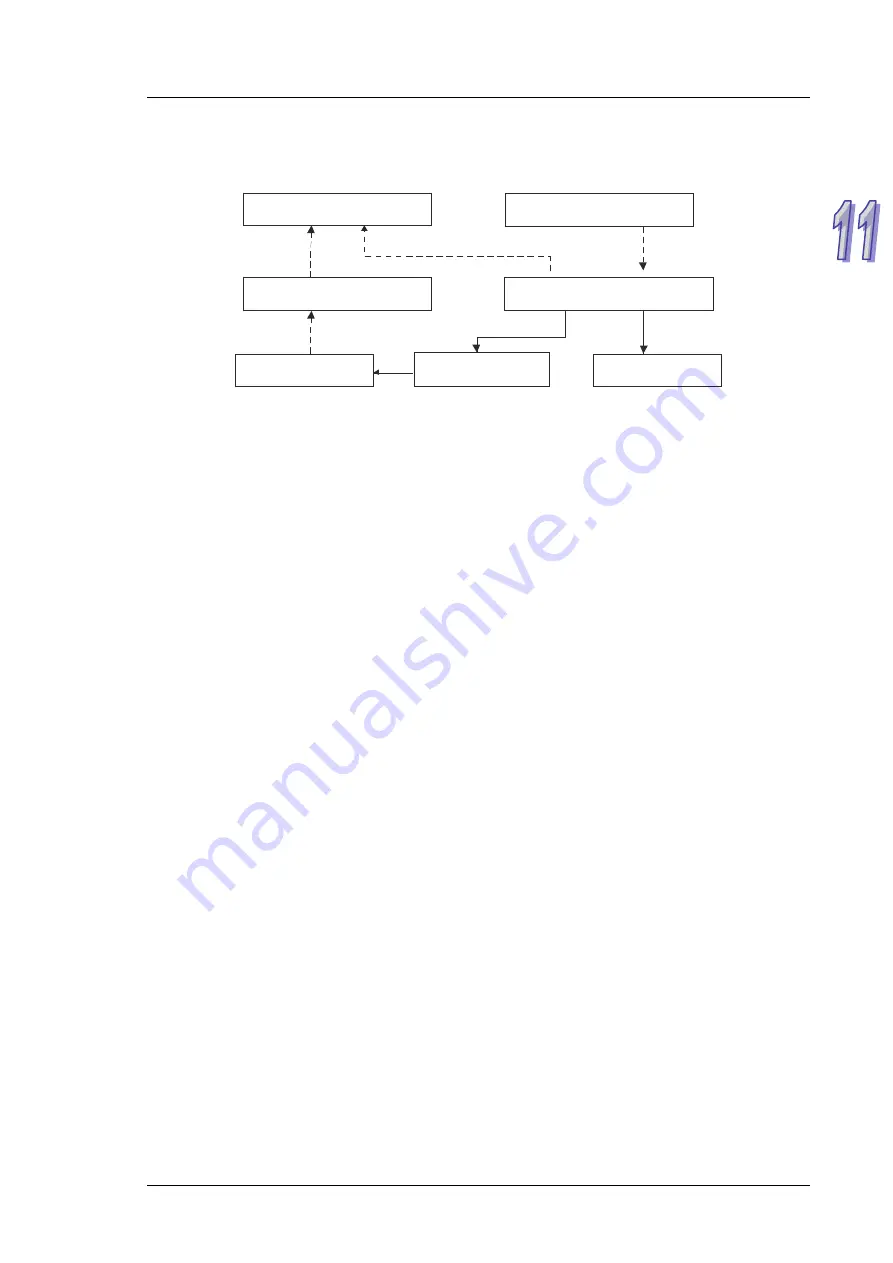
C h a p t e r 11 H i g h - s p e e d C a p t u r e a n d C o m pa r e F u n c t i o n
(2) A deviation often occurs when the present position of an axis or the value in
C200/C204/C208/C212 is read. To prevent a deviation from occurring, users read a value
immediately by setting an input terminal to ON. Capture is described below.
(C) D ata reg iste r n (n=0 ~7)
(B) C o ntro l reg iste r n (n=0 ~7)
(D) C ap tu re sou rce
(D)F RO M K2 53 K1 D 0 D 50
(A)TO K25 3 K1 D0 D5 0
(F) Tri gg er
(E) Capture mode
Block (A): The instruction TO is used to write data into control registers (block C).
Block (B): Users set a capture source (block D), set bit 5~bit 4 to 0 (block E), and set a
trigger (block F) in a control register.
Block (C): The capture of a value (block D) is triggered by an input terminal, and the value
captured is stored in data registers.
Block (D): The present positions of four axes, the values in C200, C204, C208, and C212
are capture sources.
Block (E): Capture mode
Block (F): External trigger
Block (G): The instruction FROM is used to read data from control registers (block C) and
data registers (block B). The values stored in the data registers are values
captured.
Procedure for a high-speed capture: The instruction TO is used to write data into control
registers (block A).
→
An input terminal is set to ON (block F).
→
The present position of the
1
st
/2
nd
/3
rd
/4
th
, or the value in C200/C204/C208/C212 is captured (block D). The value
captured is stored in data registers (block C).
→
Users read the value captured by means of
the instruction FROM.
Example
【
Description
】
Start the high-speed counter C204. The value in C204 is captured when X0.1 is set to ON.
【
Steps
】
1. When SM002 in O100 is ON, the initial setting of high-speed capture is carried out.
D0=0
Initial group number n=0
D1=0
D20=10
Writing 6 values by means of the instruction TO (Only one value is captured.)
D60=10
Reading 6 values by means of the instruction FROM (Only one value is
captured.)
2. When M1 is ON, the high-speed capture is set.
The value in (D3, D2) is 16#1005
The capture source set is C204. (The value of bit
3~bit 0 is 5). The mode selected is a capture mode. (The value of bit 5~bit 4 is 0.) The
trigger selected is X0.1. (The value of bit 15~bit 12 is 1.)
The value in (D5, D4) is K100. Users can set (D5, D4) by themselves.
3. The high-speed capture is started when M2 is ON.
11 - 11
Содержание AH500
Страница 9: ...viii...
Страница 52: ...Chapter 2 Hardware Specifications and Wiring Wiring AH10PM 5A and a Panasonic CN5 series servo drive 2 31...
Страница 53: ...AH500 Motion Control Module Manual Wiring AH10PM 5A and a Yaskawa servo drive 2 32...
Страница 54: ...Chapter 2 Hardware Specifications and Wiring Wiring AH10PM 5A and a Mitsubishi MJR2 series servo drive 2 33...
Страница 55: ...AH500 Motion Control Module Manual Wiring AH10PM 5A and a Fuji servo drive 2 34...
Страница 115: ...AH500 Motion Control Module Manual 4 16 MEMO...
Страница 375: ...AH500 Motion Control Module Manual 5 260 MEMO...
Страница 376: ...Chapter 6 Data Transmission Table of Contents 6 1 Functions 6 2 6 2 Parameters 6 2 6 3 Usage 6 5 6 1...
Страница 383: ...AH500 Motion Control Module Manual 6 8 MEMO...
Страница 419: ...AH500 Motion Control Module Manual 7 36 MEMO...
Страница 436: ...Chapter 8 Electronic Cam 8 17...
Страница 482: ...Chapter 10 High speed Counters and High speed Timers 3 The cyclic mode is used to measure a frequency 10 7...
Страница 483: ...AH500 Motion Control Module Manual 10 8 MEMO...
Страница 505: ...AH500 Motion Control Module Manual 12 8 MEMO...
Страница 515: ...AH500 Motion Control Module Manual 13 10 MEMO...
Страница 544: ...Appendix A Error Code Table Table of Contents A 1 Error Code Table A 2 A 1...
Страница 547: ...AH500 Motion Control Module Manual A 4 MEMO...