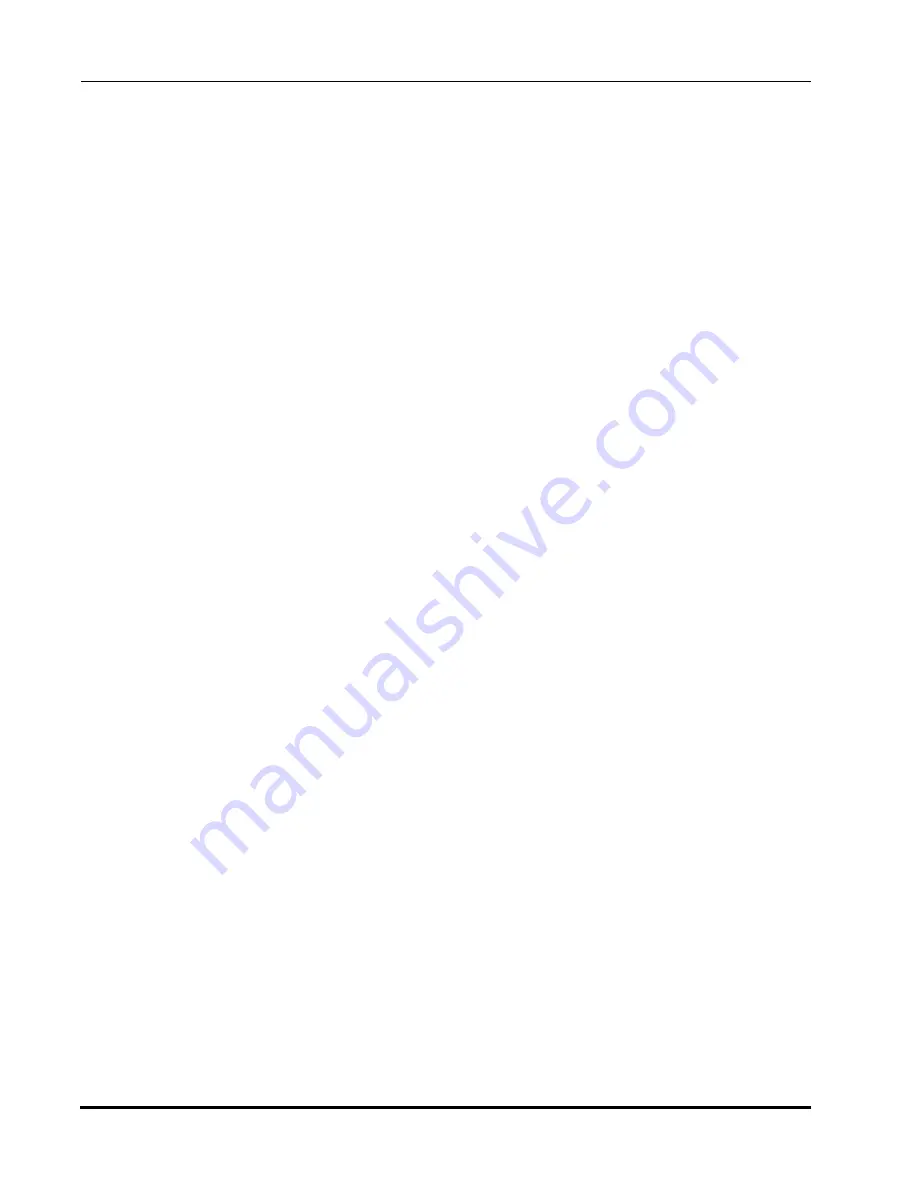
Operation
MagnaTran 7.1 User’s Manual
Operational Interlocks
MN-003-1600-00
Brooks Automation
6-26
Revision 2.2
Creating the Operational Interlocks
Creating the Operational Interlocks is a two step process. The first step maps an
assigned name to a specific pin on the discreet I/O connector and defines its behavior.
If the interlock is related to a sensor, a second step will assign the mapped I/O to a
specific station.
Related Commands
Each group of command types shown in
has Setup, Request, and Store com-
mands related to that particular group:
Sensor: Set Station Option
Request Station Option on page 8-106
Store Station Option on page 8-167
I/O State OUTPUTS:
All types:
Remove IO on page 8-66
Request I/O State on page 8-84
Request I/O Map on page 8-82
Pass Through Feature
An added feature of the I/O is to pass information from valves, etc. through the robot.
These I/O channels are mapped or assigned as discussed in this section and also have
the option of changing the polarity of the output bit. See
for the command string. Pass through items are updated every 1 mSec.
Special Notes on RETRACT_PIN
The RETRACT-PIN is a different type of operational interface in that it is controlled
by the robot motion controller. This interlock is set up at the factory on pin 35. If an
output pin is mapped as a RETRACT_PIN then it will go active whenever the robot
arm is referenced and retracted. When the robot is not referenced, an extend condi-
tion will occur to prevent slot valve closure in case the arms are extended when first
powered on. Upon power up, the default status is NOT-RETRACTED, after HOME
R, status is RETRACTED.
The robot is considered extended when it extends a distance of 5% of its total exten-
sion from home position. For example, if a robot’s total extension is 50mm from
home, then the RETRACT_PIN considers the arm extended when it has move 2.5mm
from home position (50mm x 5% = 2.5mm).