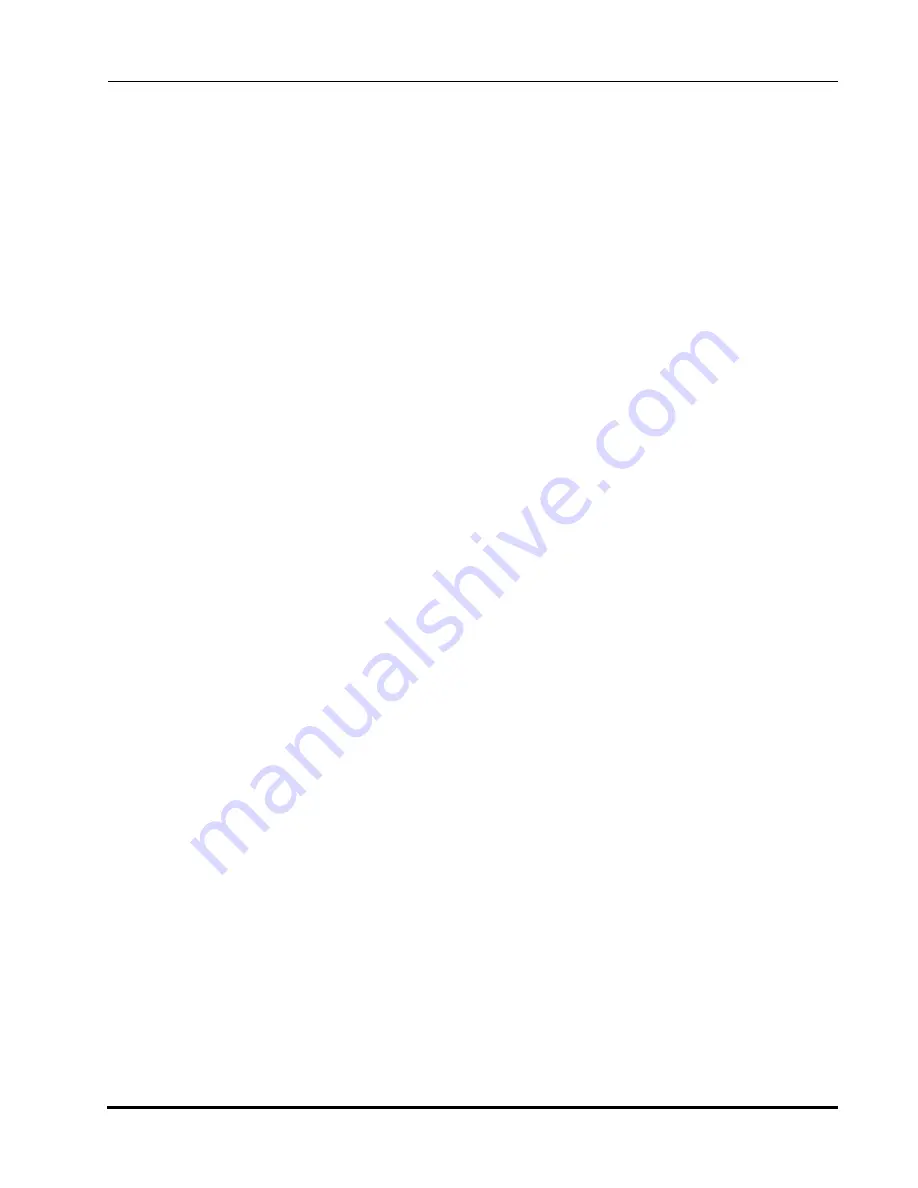
MagnaTran 7.1 User’s Manual
Subsystems
MN-003-1600-00
Mechanical System
Brooks Automation
Revision 2.2
4-9
Robot Arms
The arms supplied with the MagnaTran 7 are designed for a vacuum environment for
100mm to 300mm wafers. Various arm sizes, end effectors and configurations are
available.
Arm sets follow the basic design of the Brooks Automation “frog-leg” arms and pro-
vide a maximum extension of 1050 mm from the center-line of the robot to the center-
line of the wafer being handled. Patented arm styles are available in either the Single
Pan Arm Set, the BiSymmetrik™ Dual Pan Arm Set, or the Leap Frog™ same-side
Dual Arm Set.
displays the various arm configurations available.
Arm sets are controlled in the R and T axes by the T1 and T2 drives. The vertical
motion is controlled by the Z axis drive.
Arm motion in the T axis (rotation) is provided by synchronous rotational movement
of the T1 and T2 drives in the same direction. Due to the unique design of these drives
there is no limit to the rotational movement of the arm. Arm motion in the R axis
(radial extension) is also provided by the T1 and T2 drives. However, R motion is
accomplished by rotating these drives in opposite directions causing the arms to
extend or retract depending upon the direction of rotation.
The MagnaTran 7 robot arms are actuated by two direct drive servo motors with inde-
pendent coaxial shafts providing full two axis movement of theta (unlimited arm
rotation) and radial (extend and retract ) motion. Z (vertical) axis motion of the arm
set is accomplished by raising and lowering the drive motor assembly using a direct
drive servo motor. The unique design of the robot enables the drive shafts to interface
with the arms, without the use of rotary seals, and allows unlimited motion in the T
(rotational) axis.