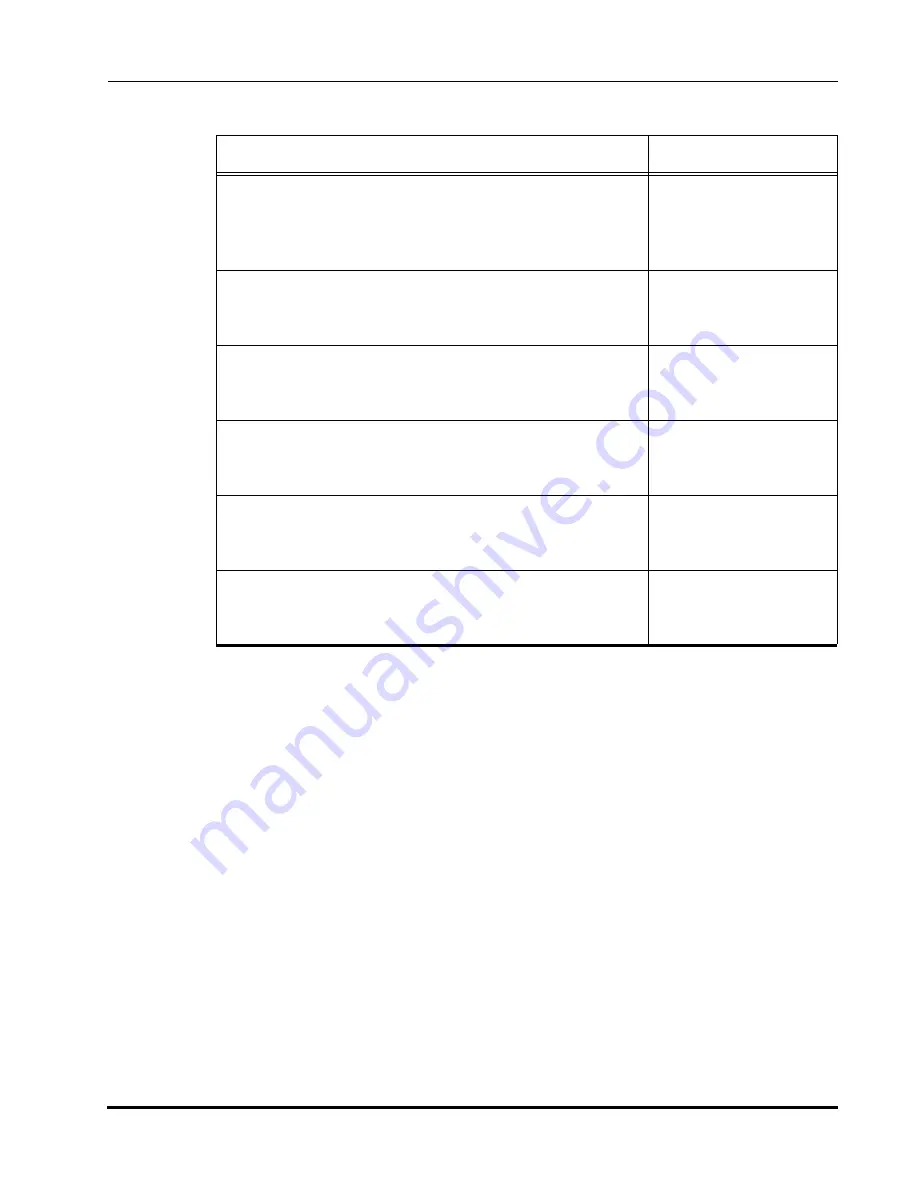
MagnaTran 7.1 User’s Manual
Troubleshooting
MN-003-1600-00
Troubleshooting Overview
Brooks Automation
Revision 2.2
10-3
3.
Troubleshooting commands: the Magnatran 7 has three commands that pro-
vide additional information from the robot that is useful in troubleshooting.
These commands are:
RQ HISTORY (see
) - this command displays the errors and non-
action commands executed by the robot.
SET ERRLVL 5 - this command sets the robot’s error level response to a range
of 1 through 5, where 1 yields the least number of error messages and 5 yields
the maximum number of error messages. The Brooks default error level is 2.
For maximum wafer throughput, the error level MUST be set at “2” after trou-
bleshooting by using the command SET ERRLVL 2 and STORE ERRLVL.
SET COMM SEQ or SET COMM BKG+ - The Magnatran 7 must either be in the
“sequential” or “bac” communication flow setting to generate error
code messages. The Magnatran 7 will not generate error code messages when
operating in the “background” communication flow setting. The robot MUST
be returned to the original communication flow setting after troubleshooting .
Refer to the Magnatran 7 User’s Manual, Command Reference Section for addi-
tional communication setting information.
Find Phase
• “Command Failed” error occurs.
• T1/T2 shafts do not move together while ping-
ing in theta direction.
See
Home Z Axis
• “Command Failed” error occurs.
See
Operational Interlock
• Operational Interlock is not functional.
• Operational Interlock state is not valid.
See
Interlock Related
Issues on page 10-20
.
Station Orientation
• Arm B moves 180 degrees from desired theta
station value.
See
Orientation Related
Issues on page 10-26
.
Repeatability
• Wafer is not placed to same position repeatedly.
See
Power Pak
• Arms “drift” after halted by Power Pak when
main robot power is turned off.
See
Table 10-1: Symptoms of Observed Errors Types
Observed Symptoms
Page Number