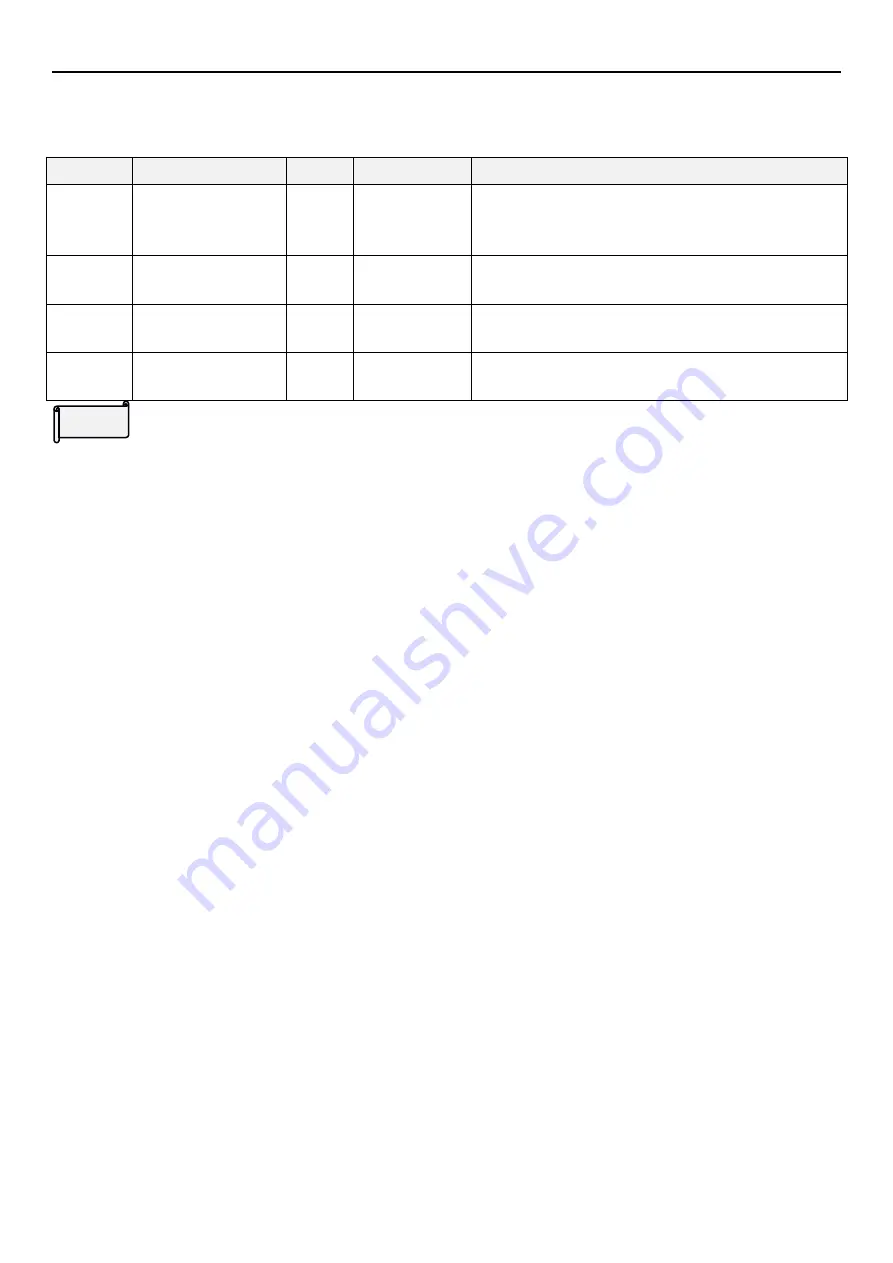
Tension control parameter group 14
PARAMETER DESCRIPTION 303
5.15.5 Tension compensation
Only relating to opened-loop torque mode.
Parameter
Name
Default Setting Range
Content
14-33
P.633
Mechanical inertia
compensation
coefficiency
0
0~65535
---
14-34
P.634
Material density
0kg/m
3
0~60000kg/m
3
---
14-35
P.635
Material width
0mm
0~60000mm
---
14-36
P.636
Friction compensation
coefficiency
0.0%
0~50.0%
---
Tension compensation
When selecting opened-loop torque mode for tension control, during the acceleration/deceleration of the system,
additional torque shall be provided in order to overcome the moment of inertia of the system.Otherwise,situation
such as tension decrease when wind-up acceleration, tension increase when wind-up deceleration or tension
increase when release acceleration, tension decrease when release decelerate might occur.
14-33(P.633) is for setting the mechanical inertia compensation coefficiency. It is used to compensate the moment
of inertia of the system, including motor, rotation system and shaft. Such inertias are fixed and are not related to
the winding radius. This parameter can be obtained automatically by self-learning or by manually setting according
to the situation.
14-34(P.634) and 14-35(P.635) is related to material inertia compensation. The inverter will automatically calculate
the material inertia compensation value according to the parameter and the winding radius.
14-36(P.636) is for setting the friction compensation coefficiency. Take wind-up for instance, Material tension
decreases because of friction ,especially with small rolls.Also,it makes tension nonlinear. It can be improved by
setting this parameter.
Setting