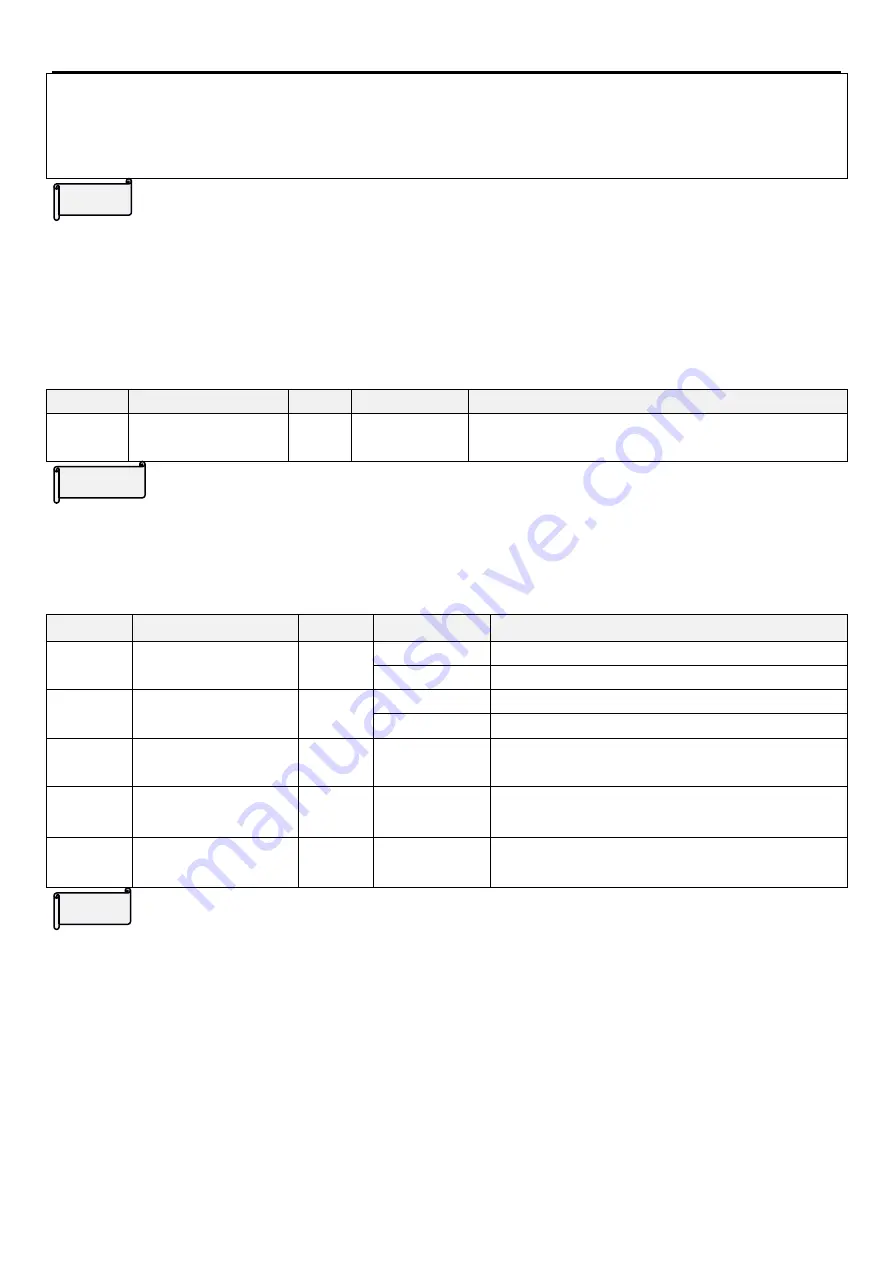
Speed and torque control parameter group 11
PARAMETER DESCRIPTION 273
Note: 1. Increase 11-00(P.320) / 11-03(P.323) speed control gain can elevate response. But set too high can generate
vibration and noises.
2. Reduce 11-01(P.321) / 11-04(P.324) speed control integral coefficient can shorten the time required to go
back to the original speed. But if the value is too small, overshoot can happen.
Adjuster parameter
When the setting value of 11-06(P.326) increases, current adjuster response level improves. But when set too
large, the current loop oscillate, and the electromagnetic noise becomes louder.
5.12.2 Low-pass filter for IM motor estimated rotation speed
Set IM motor estimated rotation speed low-pass filter time when using sensorless vector control.
Parameter
Name
Default
Setting range
Content
11-26
P.415
IM motor estimated
speed filtering time
0ms
0~100.00ms
Valid only when 00-21
(P.300)
=3
IM motor estimated rotation speed low-pass filter time setting
In sensorless vector control using IM motor, if motor oscillate, 11-26(P.415) can be adjusted , but usually not used.
5.12.3 PM motor setting
The parameters setting below can improve the VC and SVC control characteristic of PM motor.
Parameter
Name
Default
Setting Range
Content
11-07
P.327
PM motor type
0
0
SPM
1
IPM
11-08
P.328
PM motor initial position
detection method
0
0
Pull in.
1
High frequency pulse
11-09
P.329
PM motor acceleration id
80%
0~200%
id given at acceleration, valid only when 00-21
(P.300)
=6
11-10
P.330
PM motor constant
speed id
0%
0~200%
id given at constant speed, valid only when
00-21
(P.300)
=6
11-11
P.331
PM motor estimated
speed filtering time
2ms
0~1000ms
PM motor estimated rotation speed filter time constant,
valid only when 00-21
(P.300)
=6
PM motor control setting
11-08(P.328) is used to select how the rotor position is detected at PM motor start. In PM motor close-loop vector
control mode, inverter performs a magnetic pole search the first time it starts the motor. After that, rotor position is
calculated from the PG encoder signal and saved until the inverter power is switched off.
When 11-08(P.328)=0, detect initial magnetic pole position of the rotor by using pull-in method, the motor cannot
start with heavy duty, or it may fail to start.
When 11-08(P.328)=1, detect the initial magnetic pole position of the rotor by using high frequency pulse vibration
method, electromagnetic noise may be generated from the motor at start.
11-09(P.329) is the current for pulling in the pole when PM motor starts. 05-05(P.306) (motor rated current) is set
to 100%, setting the pull-in current during acceleration/deceleration, adjustments to this setting may help in the
following situations:
Setting
Setting
Setting