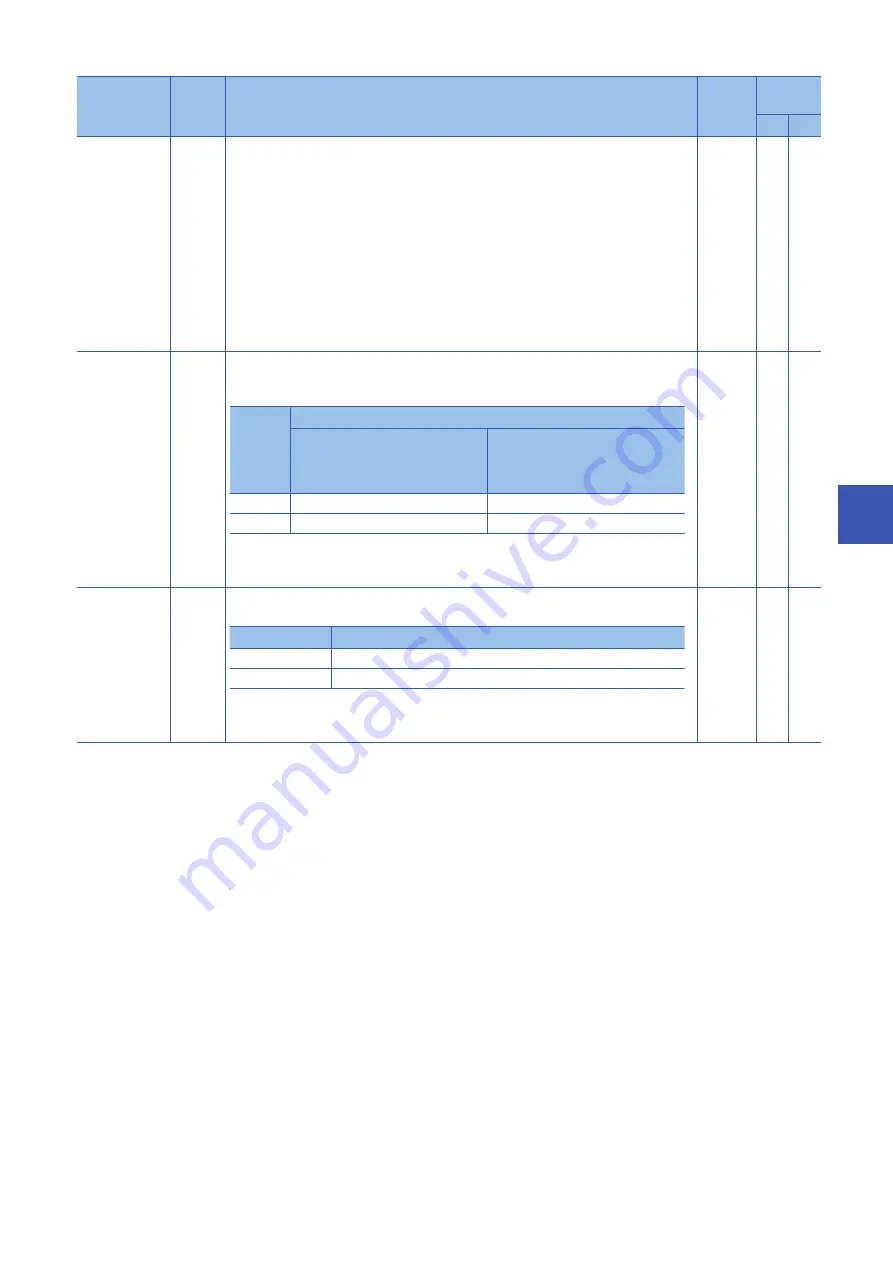
7 PARAMETERS
7.2 Detailed list of parameters
183
7
PA10
INP
In-position range
Set an in-position range per command pulse.
To change it to the servo motor encoder pulse unit, set [Pr. PC06].
In the I/O mode, the in-position range is the range where Index 2D15h Status DO5 bit5 (Travel
completion) and Index 2D11h Status DO1 bit12 (In-position) are outputted.
The unit will be as follows depending on the positioning mode.
• Point table method
When [Pr. PC06] is set to "_ _ _ 0", the unit can be changed to [
μ
m], 10
-4
[inch], 10
-3
[degree], or
[pulse] with the setting of [Pr. PT01]. When [Pr. PC06] is set to "_ _ _ 1", the unit is fixed to [pulse].
• Indexer method
It will be command unit [pulse]. (unit of a load-side rotation expressed by the number of servo motor
resolution pulses)
For example, when making an in-position range "±1 degree" for the rotation angle on the load side,
set 4194304 × (1/360) = 11650 pulses.
Setting range: 0 to 65535
1600
Refer to
Function
column
for unit.
PA14
*POL
Rotation direction
selection/travel
direction
selection
Select a rotation direction or travel direction.
The torque polarity can be changed with the combination of this parameter and [Pr. PC29 Torque
POL reflection selection].
This parameter corresponds to "Polarity (607Eh)". When the object is mapped to the cyclic
communication data, do not write values with MR Configurator2 because the controller overwrites
the servo parameter values written with MR Configurator2.
0
PA14
*POL
Station number
direction
selection
Select an assignment direction of station No.
This parameter setting is used with servo amplifier with software version A3 or later.
This parameter corresponds to "Polarity (607Eh)". When the object is mapped to the cyclic
communication data, do not write values with MR Configurator2 because the controller overwrites
the servo parameter values written with MR Configurator2.
0
No./symbol/
name
Setting
digit
Function
Initial
value
[unit]
Control
mode
CP
PS
Setting
value
Servo motor rotation direction/linear servo motor travel direction
Position mode
Positioning address increase/
Velocity mode
Speed command: positive
Position mode
Positioning address decrease/
Velocity mode
Speed command: negative
0
CCW or positive direction
CW or negative direction
1
CW or negative direction
CCW or positive direction
Setting value
Assignment direction of station No.
0
Station numbers will be assigned in CW direction in order of 1, 2, 3…
1
Station numbers will be assigned in CCW direction in order of 1, 2, 3…