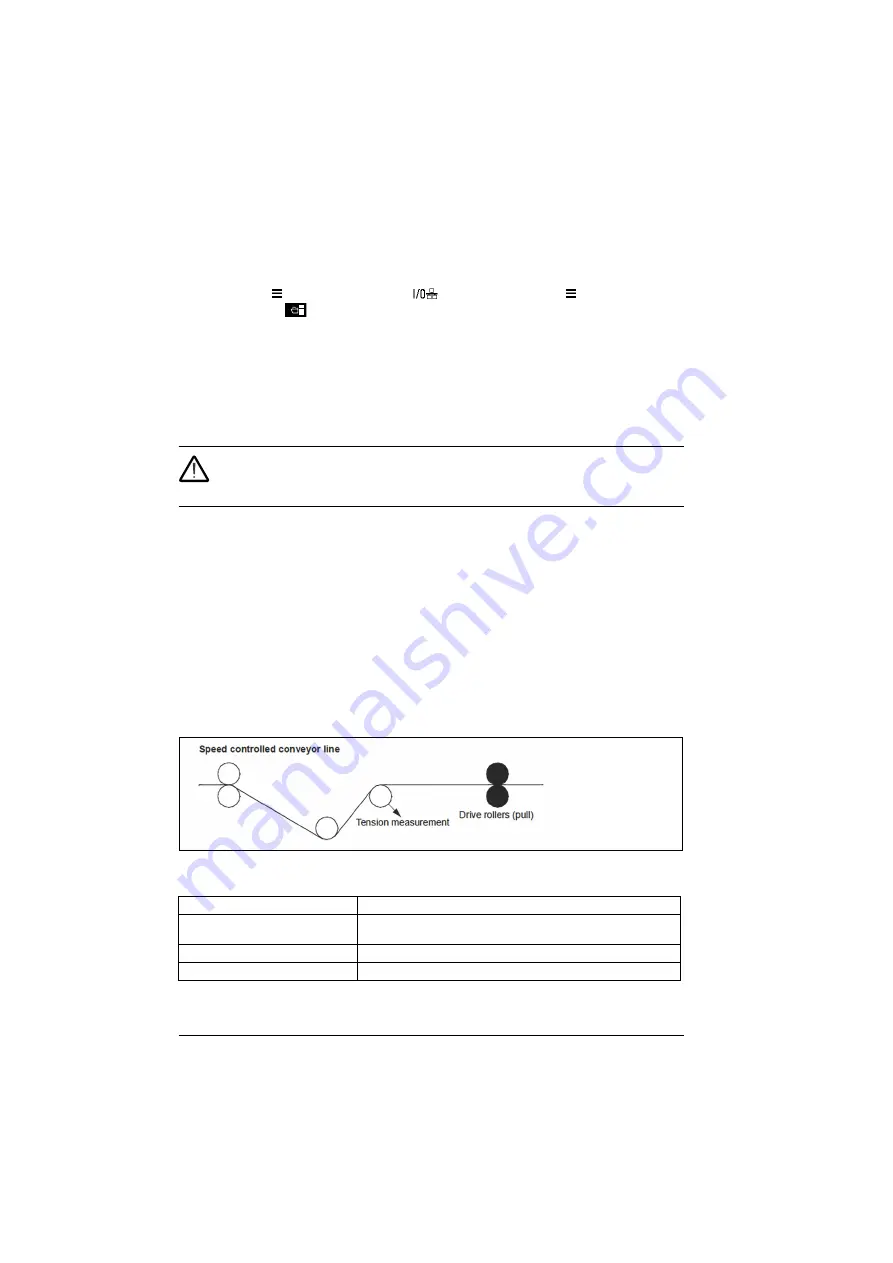
54 Program features
Settings
• Main menu
Connection macro
PID
or Main menu
Complete
parameter list
parameter
PID.
• Parameter groups
(page
) and
(page
PID trim function
The PID trim function is used to maintain the set tension either by trimming the drive
main speed reference or torque reference (speed controller output).
WARNING!
Make sure that the drive acceleration and deceleration time is set
to 0 when using PID trim function. This is required to perform quick tension
control by speed correction.
PID trim is implemented as one of the Process PID functions (parameter group
). Both PID set1 and PID set 2 can be
used for this functionality.
The trimmed output is calculated from parameter
or
. This is based on the selection in parameter
(for process PID set 1) or
(for process PID
set 2). In most of the use cases,
PID trim functionality in Variable Frequency Drive (VFD) is used in applications where
tension control of the material is very essential. For example, auxiliary drives in metal
process industries, infeed and outfeed of rotogravure printing machines, surface
winder etc.
You must link the trimmed output from PID to the speed chain manually if PID
trimmed output is used for trimming speed. Set below parameters as follows:
Parameter
Value
Process speed reference given by
source
Other,
Summary of Contents for ACS560
Page 1: ...ABB GENERAL PURPOSE DRIVES ACS560 standard control program Firmware manual...
Page 4: ...4...
Page 30: ...30 Start up control with I O and ID run...
Page 32: ...32 Using the control panel...
Page 100: ...100 Program features...
Page 153: ...Control macros 153...
Page 160: ...160...
Page 374: ...374 Parameters...
Page 408: ...408 Additional parameter data...
Page 466: ...466 Fieldbus control through the embedded fieldbus interface EFB...
Page 504: ...504 Control chain diagrams...
Page 508: ...508 Parameterization with drive composer...
Page 512: ...512 Parameterization with automation builder drive manager...