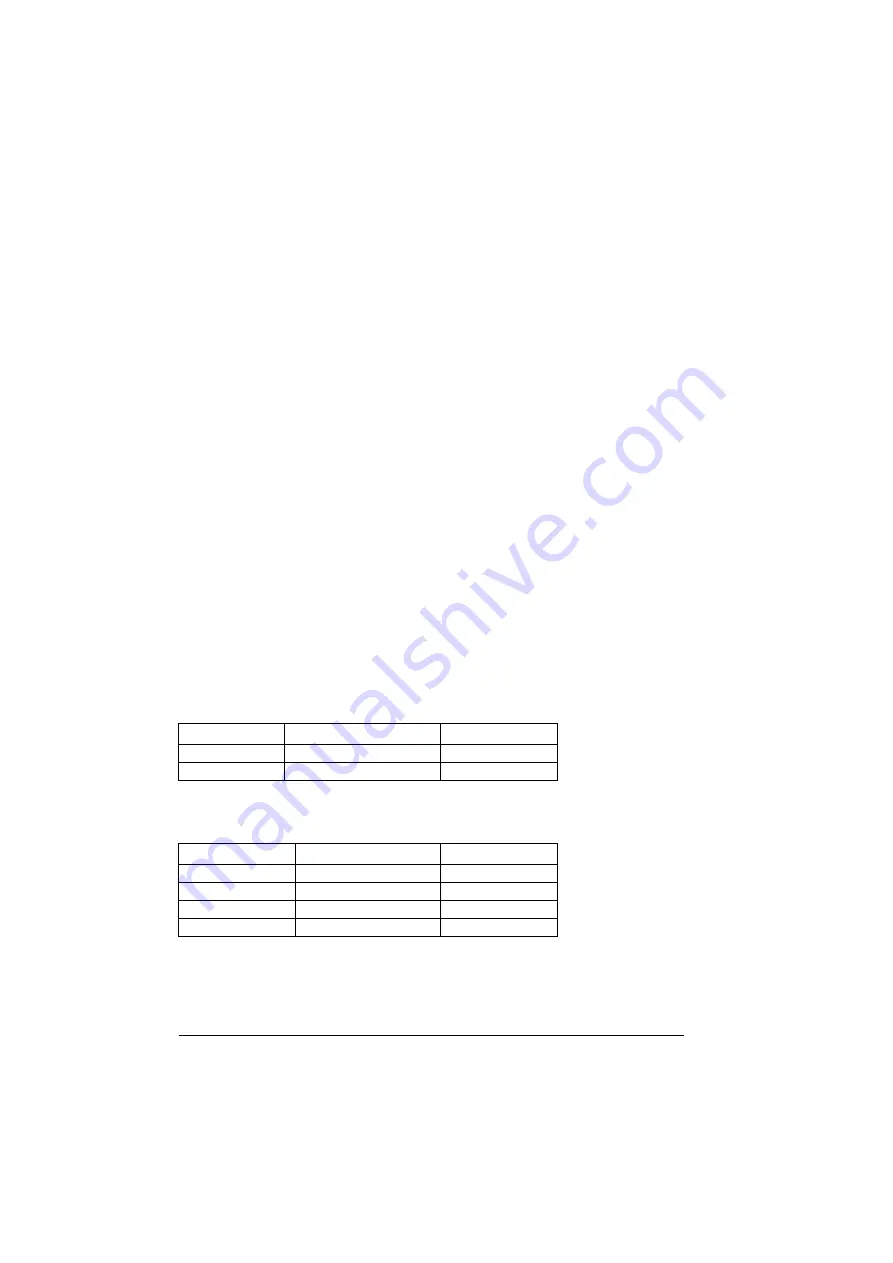
148 Control macros
T
erminal sizes
• (frames R0…R8): 0.14…1.5 mm
2
(all terminals)
• Tightening torques: 0.5…0.6 N·m (0.4 lbf·ft)
Notes
1)
Current [0(4)…20 mA,
R
in
< 500 ohm] or voltage [ 0(2)…10 V,
R
in
> 200 kohm]
input as selected with parameter
12.15 AI1 unit selection
.
2)
Current [0(4)…20 mA,
R
in
= 100 ohm] or voltage [ 0(2)…10 V,
R
in
> 200 kohm]
input as selected with parameter
12.25 AI2 unit selection
.
3)
Total load capacity of the auxiliary voltage 24V (X2:10) = 6.0 W (250 mA /
24 V). User can use this source for either of the I/O connections (DI1... DI2- RO1 or
DI3...DI6 - RO2~RO3).
4)
Connected with jumpers at the factory.
5)
Ground the outer shield of the cable 360 degrees under the grounding clamp on
the grounding shelf for the control cables.
6)
Can be used to set up pressure alarm warning.
7)
Can be used for cold start prevention with connection to ‘temperature reached’
output of temperature controller or PLC
8)
Input signal
9)
Output signal
10)
For R0...R2 frames only
For information on cable connection and drive operation, see
Control Connections
in
the
hardware manual (3AXD50000044998)
.
Additional Notes
• Some inputs and settings are set automatically as follows:
• As per the default settings, when the AI1 reference is at any value, the drive can
be started. If you want to enable the drive to start the motor only when the AI
reference is below minimum value, set the parameter as follows:
When the extruder is jammed and the motor is stopped, you can use these
settings to prevent the motor to start with existing AI reference. This helps to
prevent damage of the screw in the extruder.
No.
Name (Input/Setting)
Value
No.
Name (Input/Setting) Value
1.00V
Summary of Contents for ACS560
Page 1: ...ABB GENERAL PURPOSE DRIVES ACS560 standard control program Firmware manual...
Page 4: ...4...
Page 30: ...30 Start up control with I O and ID run...
Page 32: ...32 Using the control panel...
Page 100: ...100 Program features...
Page 153: ...Control macros 153...
Page 160: ...160...
Page 374: ...374 Parameters...
Page 408: ...408 Additional parameter data...
Page 466: ...466 Fieldbus control through the embedded fieldbus interface EFB...
Page 504: ...504 Control chain diagrams...
Page 508: ...508 Parameterization with drive composer...
Page 512: ...512 Parameterization with automation builder drive manager...