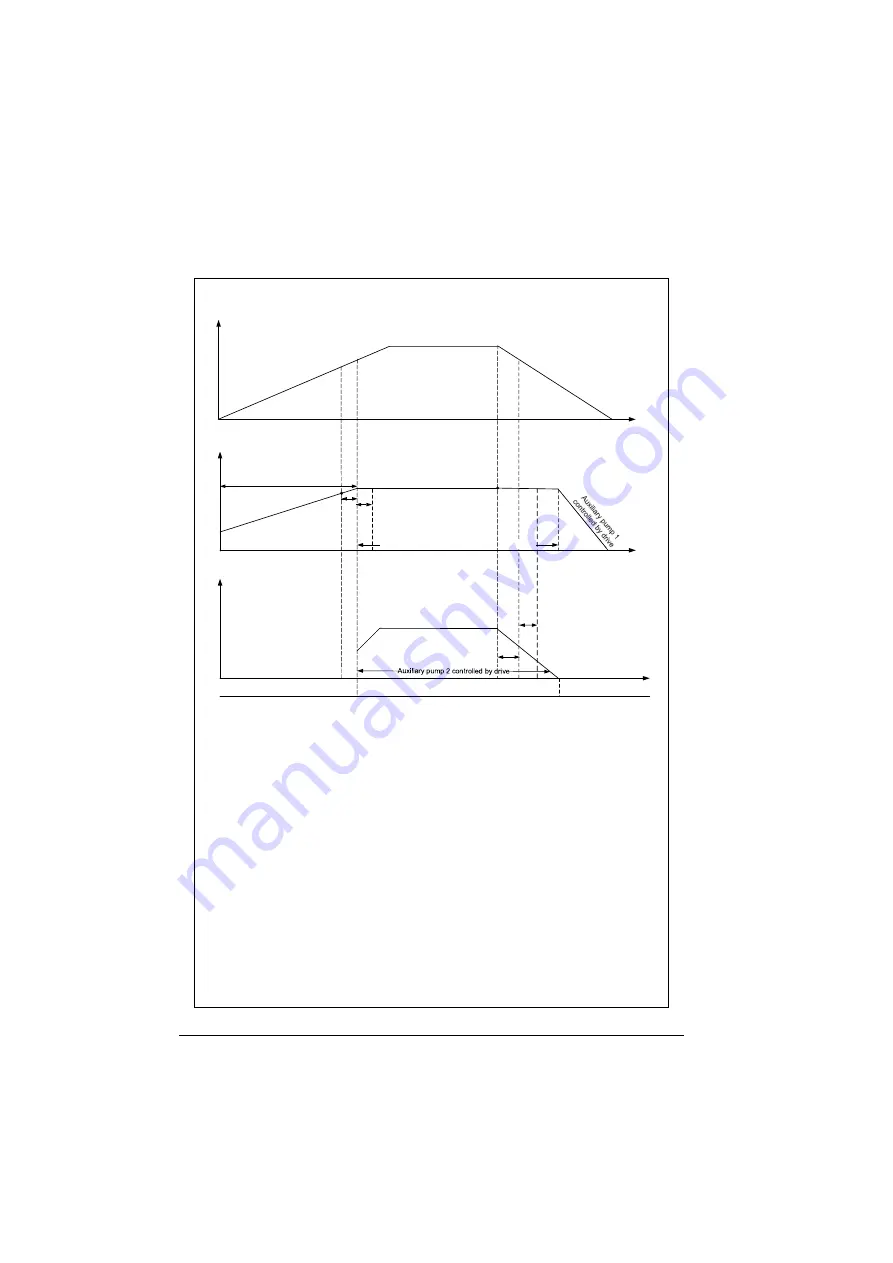
136 Control macros
SPFC enabled pump control timing diagram.
Speed (auxiliary
pump 1)
Expected
Flow Rate/
Pressure
Pump connected directly online through contactor
Time
Time
(2)
(3)
(1)
(4)
Speed (auxiliary
pump 2)
(5)
Auxiliary pump 1 controlled by
drive
Time
Relay
RO2
On
RO3
On
RO3
Off
(6)
- Start speed for the auxiliary pump 2.
- Delay time to start auxiliary pump 2. The pump is
started only when the speed of the auxiliary pump 1 is higher or same as the
start speed (
) for the duration mentioned in this parameter.
- Time used to compensate the time needed to
accelerate the auxiliary pump 2 to a speed where it produces flow. For
duration mentioned in the parameter, the auxiliary pump 1 maintains its
speed momentum.
(4)
- Stop speed for the auxiliary pump 2.
- Delay time to turn off the auxiliary pump 2 when the
speed of the auxiliary pump 1 is lower or same as the stop speed (
) for
the duration mentioned in this parameter.
(6)
- Time is used to compensate the time needed
to accelerate the auxiliary pump 1 to a speed where it produces flow.
(
Demand - represented by the pro-
cess PID reference)
Summary of Contents for ACS560
Page 1: ...ABB GENERAL PURPOSE DRIVES ACS560 standard control program Firmware manual...
Page 4: ...4...
Page 30: ...30 Start up control with I O and ID run...
Page 32: ...32 Using the control panel...
Page 100: ...100 Program features...
Page 153: ...Control macros 153...
Page 160: ...160...
Page 374: ...374 Parameters...
Page 408: ...408 Additional parameter data...
Page 466: ...466 Fieldbus control through the embedded fieldbus interface EFB...
Page 504: ...504 Control chain diagrams...
Page 508: ...508 Parameterization with drive composer...
Page 512: ...512 Parameterization with automation builder drive manager...