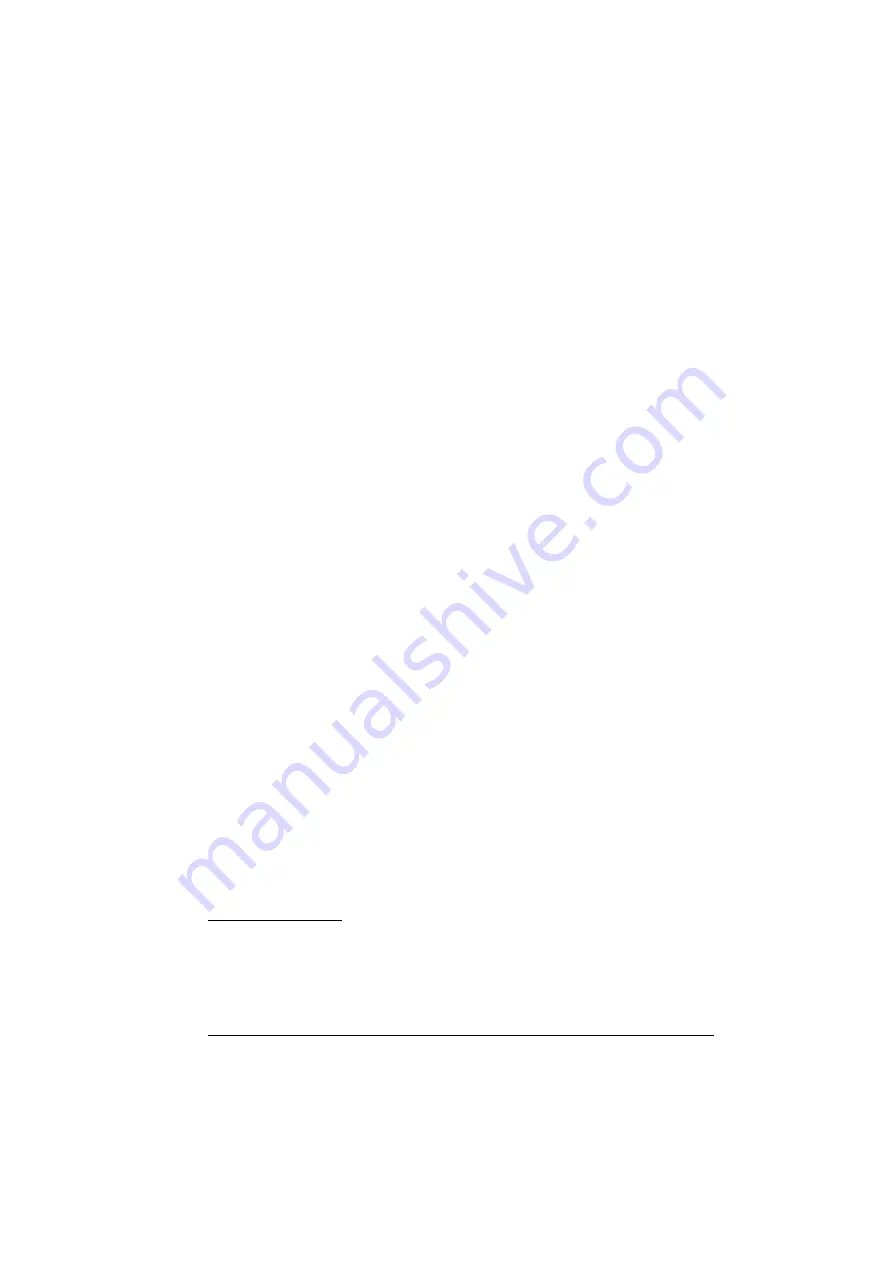
Program features 59
= 750 (AI1 actual scaled value)
= 100 (limited to 100)
= 0.1
= 0.5
Then,
If
is 0.
If
is 750.
If
is 1500.
PID trim auto connection
PID trim auto connection (
) enables the connection of PID
trim output actual (
) to the respective speed, torque
or frequency reference chains. You can use parameter
(for
(for PID set 2) and select the respective trim
(speed, torque or frequency).
The motor control mode (
) also impacts the PID trim output
actual (
) added to the speed, torque or frequency
reference chains. In scalar control mode, the speed trim and torque trim values are
zero and in vector control mode, the frequency trim value is zero.
See the control chain diagram on page
.
Note:
is disabled and the drive stops
through Ramp stop (Off1) or Emergency ramp stop (Off3) emergency stop mode
(
), the PID trim output actual (
) is not added to the frequency reference chain during the drive
deceleration condition
Speed trim connection
Speed trim is added to
. The parameter
displays the final speed reference after the addition of speed trim.
Par40.05
1500 0.1
1 0.1
–
0
+
1
=
Par40.05
150
=
Par40.05
1500 0.1
1 0.1
–
750
+
1
=
Par40.05
825
=
Par40.05
1500 0.1
1 0.1
–
1500
+
1
=
Par40.05
1500
=
Summary of Contents for ACS560
Page 1: ...ABB GENERAL PURPOSE DRIVES ACS560 standard control program Firmware manual...
Page 4: ...4...
Page 30: ...30 Start up control with I O and ID run...
Page 32: ...32 Using the control panel...
Page 100: ...100 Program features...
Page 153: ...Control macros 153...
Page 160: ...160...
Page 374: ...374 Parameters...
Page 408: ...408 Additional parameter data...
Page 466: ...466 Fieldbus control through the embedded fieldbus interface EFB...
Page 504: ...504 Control chain diagrams...
Page 508: ...508 Parameterization with drive composer...
Page 512: ...512 Parameterization with automation builder drive manager...