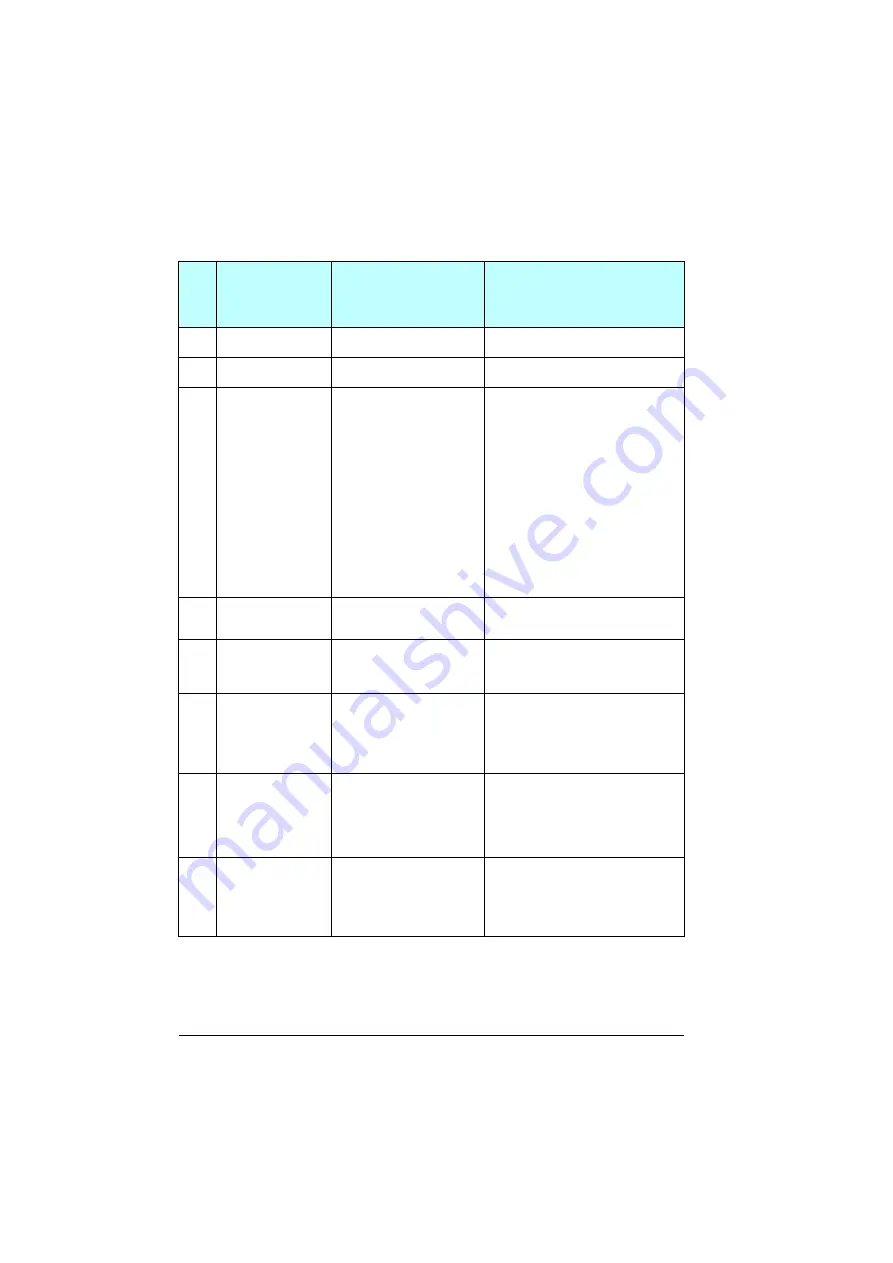
418 Fault tracing
0000 0002 Thermal time constant not
given.
Check value of
0000 0003 Maximum continuous power
not given.
Check value of
A79C
BC IGBT excess
temperature
Brake chopper IGBT
temperature has exceeded
internal warning limit.
Let chopper cool down.
Check for excessive ambient
temperature.
Check for cooling fan failure.
Check for obstructions in the air flow.
Check the dimensioning and cooling of
the cabinet.
Check resistor overload protection
function settings (parameters
).
Check minimum allowed resistor value
for the chopper being used.
Check that braking cycle meets allowed
limits.
Check that drive supply AC voltage is not
excessive.
A7AB
Built in/Extension I/O
configuration failure
The I/O built in/extension
module is not connected to the
device properly.
Make sure that the I/O built in/extension
module is connected to the device.
A7AC I/O Module internal
error
Calibration data is not stored in
the I/O module. Analog signals
are not working with full
accuracy.
Replace I/O module.
A7A1
Mechanical brake
closing failed
Mechanical brake control
warning.
Check mechanical brake connection.
Check mechanical brake settings in
parameter group
Check that acknowledgment signal
matches the actual status of the brake.
A7A2
Mechanical brake
opening failed
Status of mechanical brake
acknowledgment is not as
expected during brake open.
Check mechanical brake connection.
Check mechanical brake settings in
parameter group
Check that acknowledgment signal
matches the actual status of brake.
A7A5
Mechanical brake
opening not allowed
Open conditions of mechanical
brake cannot be fulfilled.
Check mechanical brake settings in
parameter group
Check that the acknowledgment signal (if
used) matches the actual status of the
brake.
Code
(hex)
Warning / Aux. code
(
aux code visible only
on assistant control
panel and drive
composer
)
Cause
What to do
Summary of Contents for ACS560
Page 1: ...ABB GENERAL PURPOSE DRIVES ACS560 standard control program Firmware manual...
Page 4: ...4...
Page 30: ...30 Start up control with I O and ID run...
Page 32: ...32 Using the control panel...
Page 100: ...100 Program features...
Page 153: ...Control macros 153...
Page 160: ...160...
Page 374: ...374 Parameters...
Page 408: ...408 Additional parameter data...
Page 466: ...466 Fieldbus control through the embedded fieldbus interface EFB...
Page 504: ...504 Control chain diagrams...
Page 508: ...508 Parameterization with drive composer...
Page 512: ...512 Parameterization with automation builder drive manager...