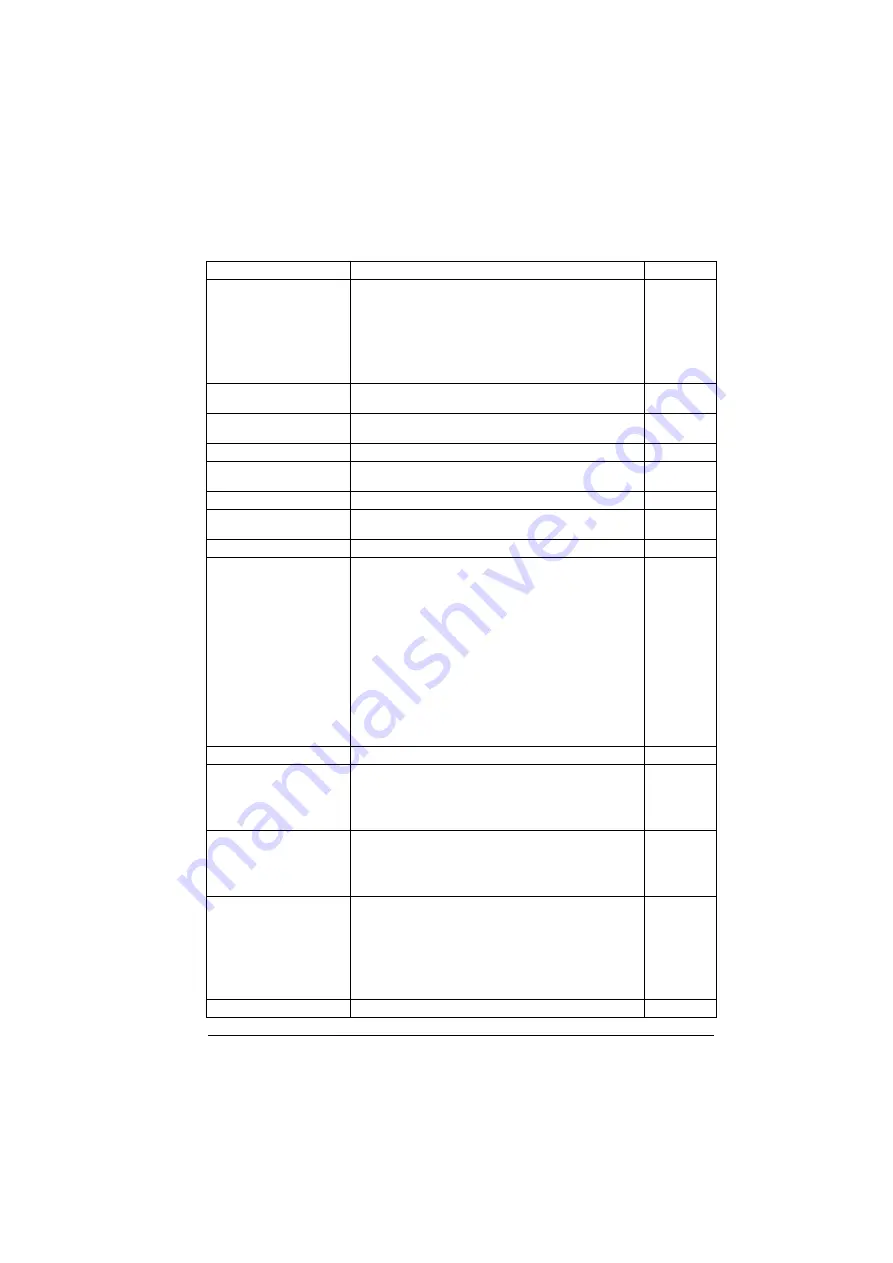
Parameters 347
PFC
PFC enabled. One pump at a time is controlled by the drive.
The remaining pumps are direct-on-line pumps that are
started and stopped by the drive logic
The frequency (group
) / speed
) reference must be
defined as PID for the PFC functionality to work properly.
SPFC enabled. For more information, see
on page.
2
SPFC
SPFC enabled. For more information, see
on page.
3
Total number of motors used in the application, including the
motor connected directly to the drive.
1
1…4
Number of motors.
1 = 1
Minimum number of motors running simultaneously.
1
0…4
Minimum number of motors.
1 = 1
Maximum number of motors running simultaneously.
1
1…4
Maximum number of motors.
1 = 1
Defines the start speed (Hz/rpm) for the first auxiliary pump.
As the motor speed or frequency exceeds the limit defined by
this parameter, a new auxiliary pump is started.
To avoid nuisance starts of the auxiliary pump, the speed of
the variable speed pump should be higher than the start
speed for the duration defined by parameter
. If the speed decreases below the start speed, the
auxiliary pump is not started.
To maintain the process conditions during the start of the
auxiliary pump, a speed hold on time can be defined with
parameter
. Certain pump types do
not produce significant flow with low frequencies. The speed
hold on time can be used to compensate the time needed to
accelerate the auxiliary pump to a speed where it produces
flow.
Vector:
1300 rpm;
Scalar 48 Hz;
58 Hz
(
b0)
0…32767 rpm/Hz
Speed/frequency.
1 = 1 unit
Defines the start speed (Hz/rpm) for the second auxiliary
motor. See parameter
.
Vector:
1300 rpm;
Scalar 48 Hz;
58 Hz
(
b0)
Defines the start speed (Hz/rpm) for the third auxiliary motor.
See parameter
Vector:
1300 rpm;
Scalar 48 Hz;
58 Hz
(
b0)
Defines the stop speed (Hz/rpm) for the first auxiliary motor.
When the speed of the motor connected directly to the drive
falls below this value and one auxiliary motor is running, the
stop delay defined by parameter
is started.
If the speed is still at the same level or lower when the stop
delay elapses, the first auxiliary motor stops.
The running speed of the drive is increased by [
] after the auxiliary motor stops
Vector:
800 rpm;
Scalar 25 Hz;
30 Hz
(
b0)
0…32767 rpm/Hz
Speed/frequency
1 = 1 unit
No.
Name/Value
Description
Def/FbEq16
Summary of Contents for ACS560
Page 1: ...ABB GENERAL PURPOSE DRIVES ACS560 standard control program Firmware manual...
Page 4: ...4...
Page 30: ...30 Start up control with I O and ID run...
Page 32: ...32 Using the control panel...
Page 100: ...100 Program features...
Page 153: ...Control macros 153...
Page 160: ...160...
Page 374: ...374 Parameters...
Page 408: ...408 Additional parameter data...
Page 466: ...466 Fieldbus control through the embedded fieldbus interface EFB...
Page 504: ...504 Control chain diagrams...
Page 508: ...508 Parameterization with drive composer...
Page 512: ...512 Parameterization with automation builder drive manager...