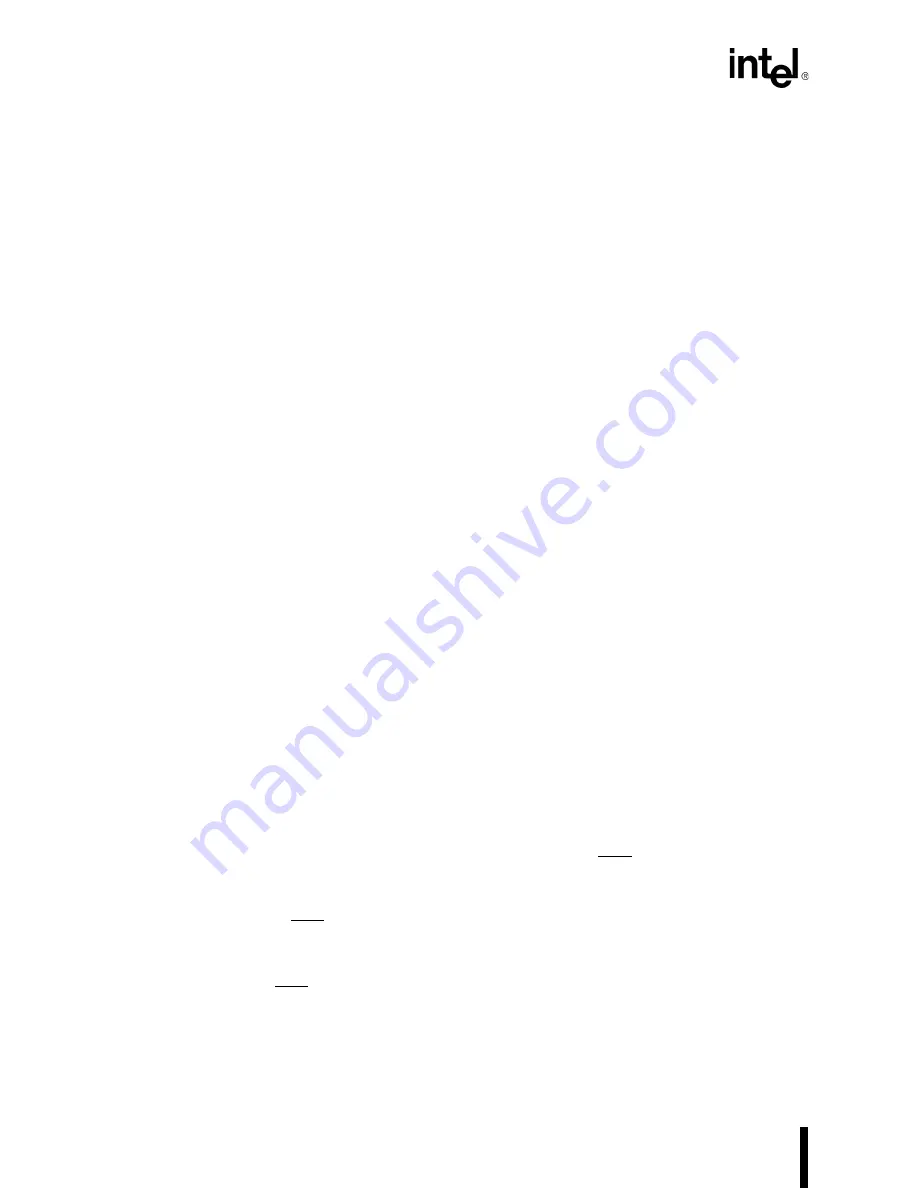
CLOCK GENERATION AND POWER MANAGEMENT
5-6
An important consideration when using crystals is that the oscillator start correctly over the volt-
age and temperature ranges expected in operation. Observe oscillator startup in the laboratory.
Varying the load capacitors (within about ± 50%) can optimize startup characteristics versus sta-
bility. In your experiments, consider stray capacitance and scope loading effects.
For help in selecting external oscillator components for unusual circumstances, count on the crys-
tal manufacturer as your best resource. Using low-cost ceramic resonators in place of crystals is
possible if your application will tolerate less precise frequencies.
5.1.2
Using an External Oscillator
The microprocessor’s on-board clock oscillator allows the use of a relatively low cost crystal.
However, the designer may also use a “canned oscillator” or other external frequency source.
Connect the external frequency input (EFI) signal directly to the oscillator X1 input. Leave X2
unconnected. This oscillator input drives the internal divide-by-two counter directly, generating
the CPU clock signals. The external frequency input can have practically any duty cycle, provid-
ed it meets the minimum high and low times stated in the data sheet. Selecting an external clock
oscillator is more straightforward than selecting a crystal.
5.1.3
Output from the Clock Generator
The crystal oscillator output drives a divide-by-two circuit, generating a 50% duty cycle clock for
the processor’s integrated components. All processor timings refer to this clock, available exter-
nally at the CLKOUT pin. CLKOUT changes state on the high-to-low transition of the X1 signal,
even during reset and bus hold.
In a CMOS circuit, significant current flows only during logic level transitions. Since the micro-
processor consists mostly of clocked circuitry, the clock distribution is the basis of power man-
agement.
5.1.4
Reset and Clock Synchronization
The clock generator provides a system reset signal (RESET). The RES input generates RESET
and the clock generator synchronizes it to the CLKOUT signal.
A Schmitt trigger in the RES input ensures that the switch point for a low-to-high transition is
greater than the switch point for a high-to-low transition. The processor must remain in reset a
minimum of 4 CLKOUT cycles after V
CC
and CLKOUT stabilize. The hysteresis allows a simple
RC circuit to drive the RES input (see Figure 5-5). Typical applications can use about 100 milli-
seconds as an RC time constant.
Summary of Contents for 80C186XL
Page 1: ...80C186XL 80C188XL Microprocessor User s Manual...
Page 2: ...80C186XL 80C188XL Microprocessor User s Manual 1995...
Page 18: ...1 Introduction...
Page 19: ......
Page 27: ......
Page 28: ...2 Overview of the 80C186 Family Architecture...
Page 29: ......
Page 79: ......
Page 80: ...3 Bus Interface Unit...
Page 81: ......
Page 127: ......
Page 128: ...4 Peripheral Control Block...
Page 129: ......
Page 137: ......
Page 138: ...5 ClockGenerationand Power Management...
Page 139: ......
Page 154: ...6 Chip Select Unit...
Page 155: ......
Page 178: ...7 Refresh Control Unit...
Page 179: ......
Page 193: ......
Page 194: ...8 Interrupt Control Unit...
Page 195: ......
Page 227: ......
Page 228: ...9 Timer Counter Unit...
Page 229: ......
Page 253: ......
Page 254: ...10 Direct Memory Access Unit...
Page 255: ......
Page 283: ......
Page 284: ...11 Math Coprocessing...
Page 285: ......
Page 302: ...12 ONCE Mode...
Page 303: ......
Page 306: ...A 80C186 Instruction Set Additions and Extensions...
Page 307: ......
Page 318: ...B Input Synchronization...
Page 319: ......
Page 322: ...C Instruction Set Descriptions...
Page 323: ......
Page 371: ......
Page 372: ...D Instruction Set Opcodes and Clock Cycles...
Page 373: ......
Page 396: ...Index...
Page 397: ......