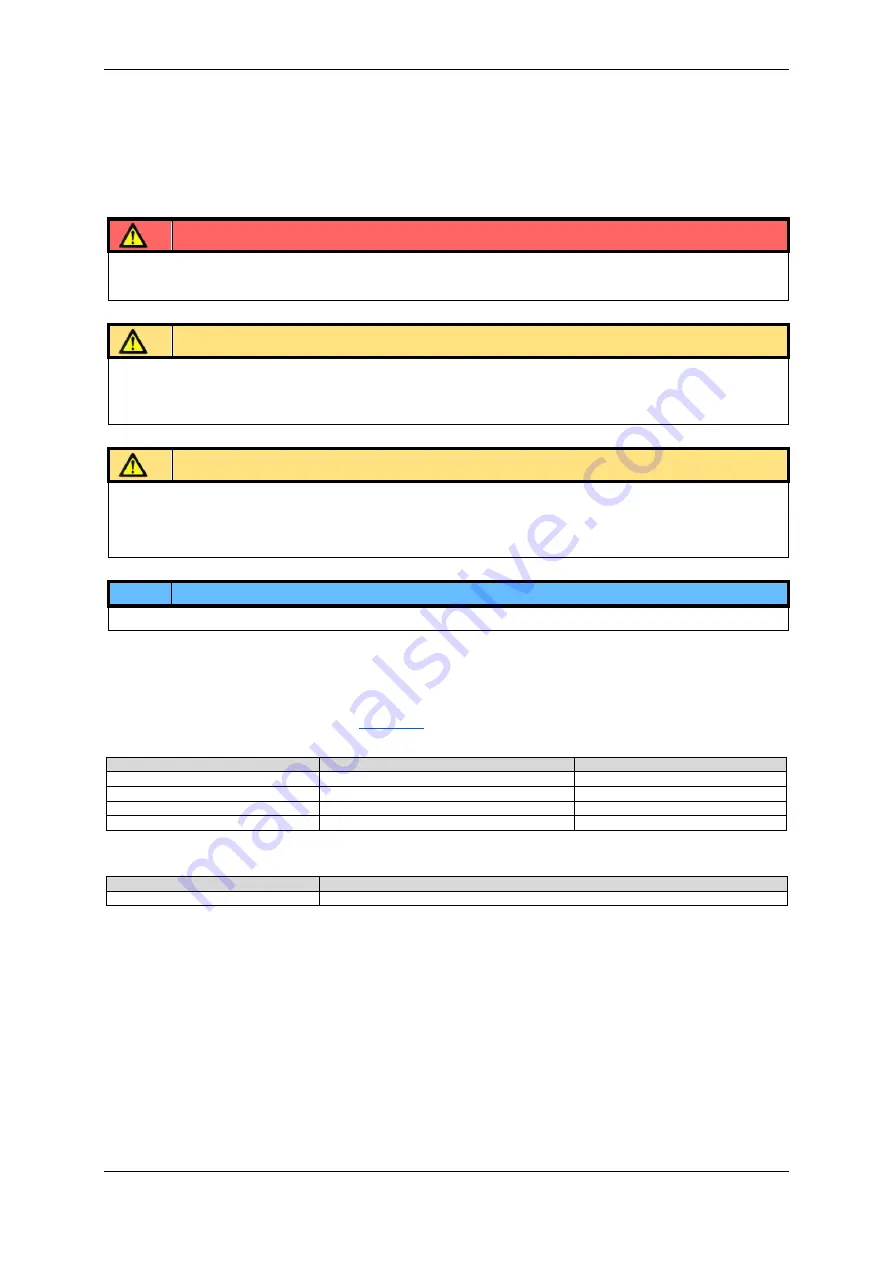
Initial Operation and User Interface
40/121
Operating Manual dryve D1, ST-, DC-, EC/BLDC-Motor Control System - V2.4
5.4.8 Braking Resistor for EC/BLDC Motors
While reducing the motor speed the motor will to change into the generator operation state. This produces a counter-voltage
peaks which might be higher as the applied load voltage and might cause the destruction of the dryve D1 controller.
If an application requires high decelerations a Braking Resistor must be used to dissipate the generated excessive energy.
Each used dryve D1 controller driving an EC/BLDC motor must be equipped with it’s own Braking Resistor.
WARNING!
-
Burn Hazard!
The surface temperature of the resistor can reach temperatures of above 250°C.
Consider necessary component mounting distances and ensure an adequate resistor and switching cabinet cooling.
WARNING!
-
Risk of destruction!
Using a multi axis system containing several dryve D1 controller with EC/BLDC motors and connecting all these controllers
motor connector X5 wise to one single Braking Resistor may lead to a destruction of all connected controllers due to high
current flow in-between.
NOTE
The Braking Resistor is only available for EC/BLDC motors.
5.4.8.1 Braking Resistor selection for igus motors
The stated resistor values were determined from different application scenarios and are meant as a guideline to select an
appropriate resistor.
The corresponding part number is stated at the
(p. 115).
If the application requires a detailed det
ermination, please proceed at “Braking Resistor Dimensioning for Custom Motors”.
Motor
Resistance Value with 48 V Load Voltage
Power
MOT-EC-42-XXX
18 Ω
15 W
– 35 W
MOT-EC-56-XXX
4,7 Ω
25 W
– 65 W
MOT-EC-60-XXX
3,3 Ω
50 W
– 85 W
MOT-EC-86-XXX
2,7
Ω
50 W
– 100 W
Wire Cross-Section
Cable length
Min Cross-Section
Max. 3m
0,34 mm²
Danger!
-
Fire Hazard!
An incorrectly dimensioned Brake Resistor might cause a thermal overload and lead to an acute fire hazard.