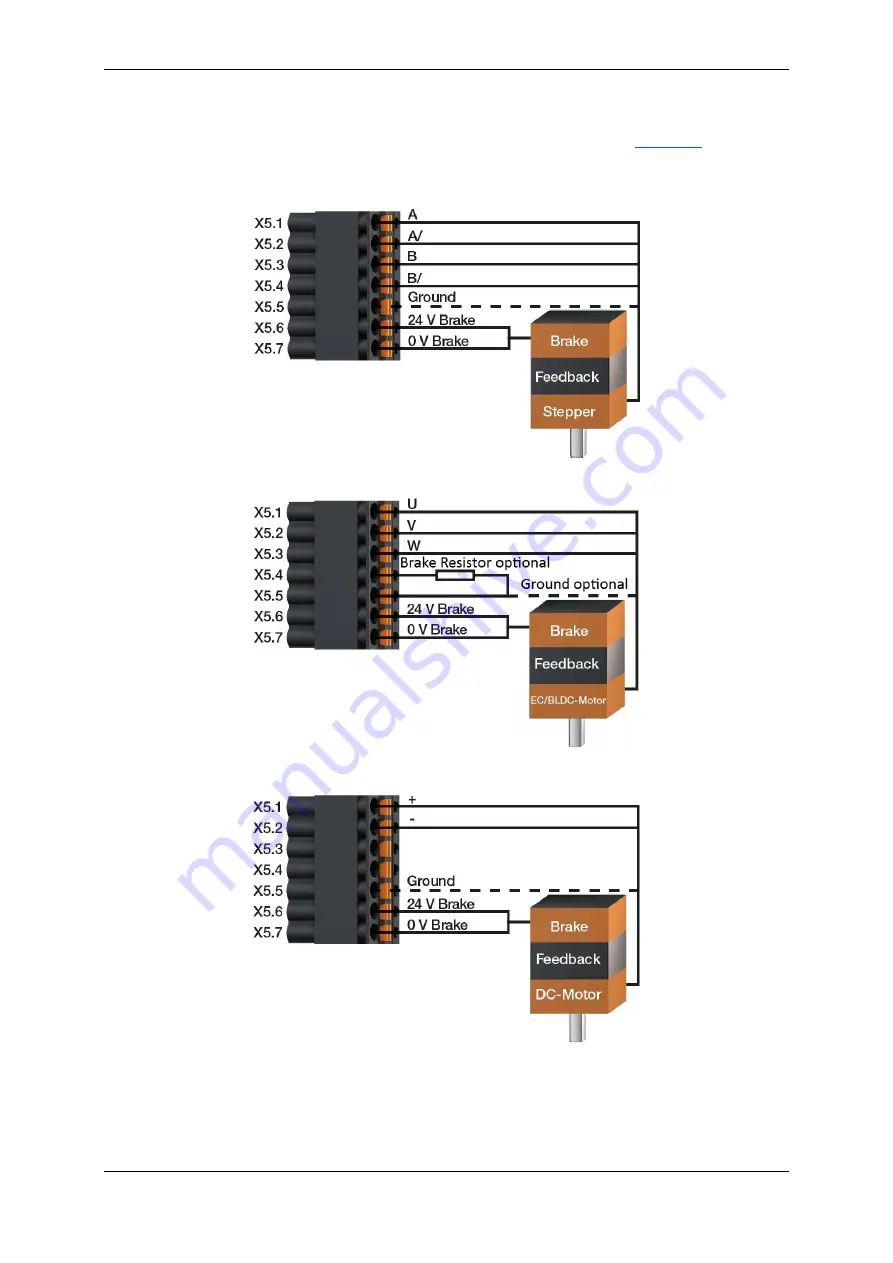
Installation
23/121
Operating Manual dryve D1, ST-, DC-, EC/BLDC-Motor Control System - V2.4
The following illustrations show how to connect a holding brake to X5.6 and X5.7.
If the dryve D1 motor control system is operated with a load voltage of 24 V at X1.1, the voltage is directly passed on to the X5.6
brake output. In the case of a load voltage of 48 V at X1.1, the brake output voltage is lowered by a
to 24 V.
In case of a necessary motor potential equalisation this is to be achieved via X5.5.
Stepper Motor
EC/BLDC Motor
DC Motor