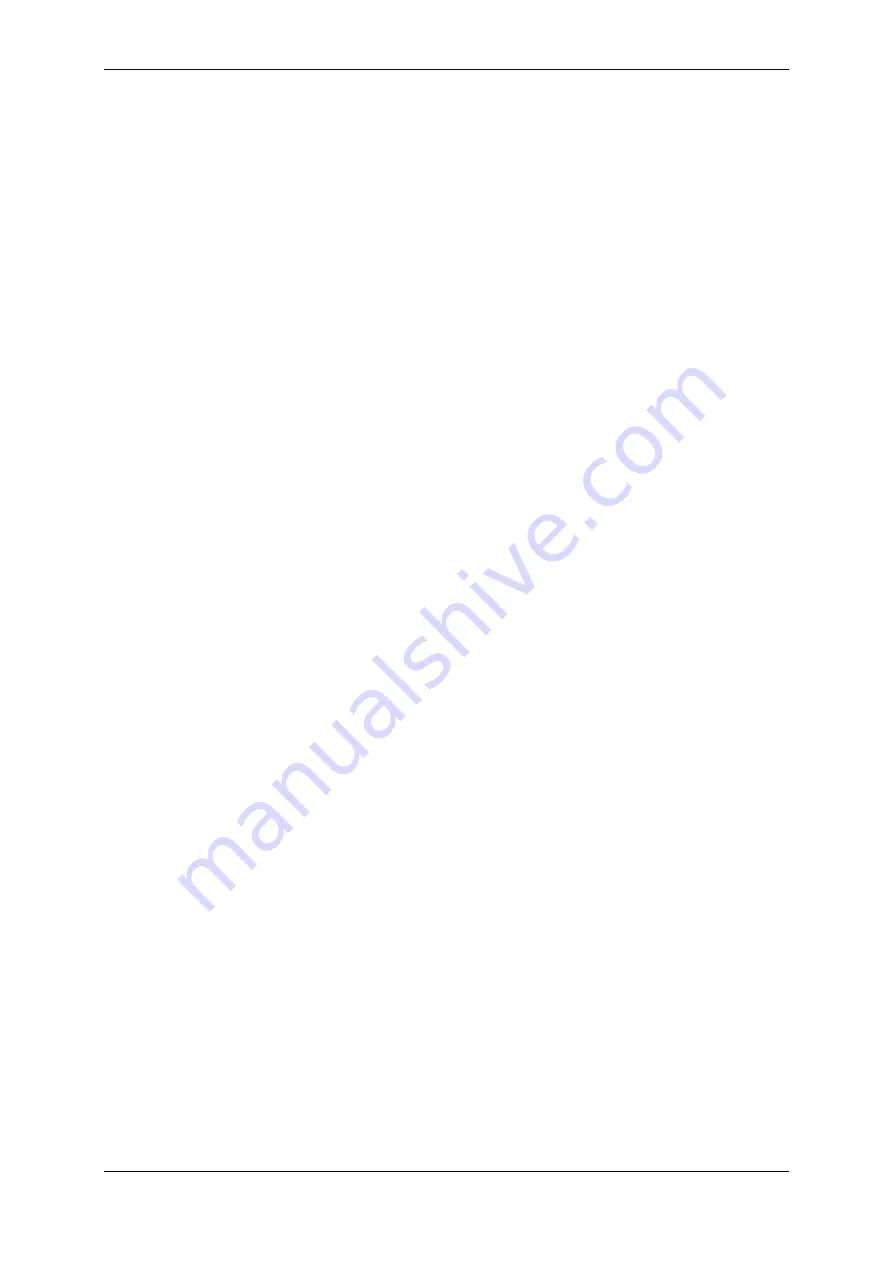
Product Overview
13/121
Operating Manual dryve D1, ST-, DC-, EC/BLDC-Motor Control System - V2.4
3 Product Overview
Ready to use instantly
The igus
®
dryve D1 uses standard commercially available Ethernet technology and therefore can communicate directly with
your network or a control unit (PC or PLC) via a standard Ethernet cable. The user interface is displayed in a browser of your
choice, without having to install any additional software. This makes it possible to parameterise the igus
®
dryve D1 motor
controller in an extremely short time.
Easy to control
You can use the simple intuitive user interface to parameterise positioning movements, accelerations and velocities of your
linear axis without the need of having any prior knowledge. Programs for continuously recurring movements can be created in
just a few seconds. A "Teach" function makes it possible to incorporate current actuator positions into the parameterisation with
just one click of the mouse.
Industry standards
The standard communication protocols CANopen and Modbus TCP Gateway make it very easy to connect the system to
industrial controllers such as the programmable logical controllers (PLC) as of Siemens or Beckhoff. The ten digital inputs, 5 of
which are binary coded for the preselection of 32 positioning movements, and five digital outputs enable extremely easy
communication with higher-level industrial controllers as well as with low-price open-source modules such as an Arduino or
Raspberry Pi.
Powerful technology
The igus
®
dryve D1 supports stepper, DC and EC/BLDC-Motors in Open-Loop as with Closed-Loop technology. With the
sinusoidally commutated Closed-Loop, a Stepper Motor can be operated as a servo motor. Due to the Closed-Loop, the Motor
Current is controlled according to the load case, because of which the operating temperature of the dryve D1 and the connected
motor can be lowered.
To optimally attune the igus
®
dryve D1 to a motor, current, velocity and position control parameters are able to be tuned. In
addition an automatic Step Mode selection is available.
The system can be set to the "zero point" by different external and internal homing methods. Position monitoring with automatic
Following Error correction and Closed-Loop control is available via different Feedback systems. The supported load voltage of
up to 48 V ensures high motor velocities, whereby the high rated current of 7 A and peak currents of up to 21 A (depending on
type of motor) enable powerful and dynamic movements.
I²T motor protection
To protect motors against thermal overload, the igus
®
dryve D1 is equipped with I²T protection for overload monitoring.
I²T protection makes it possible to safely operate the motor for a certain time even if used with overload conditions.
3.1 Operating Modes
In the following section, the different operating modes of the dryve D1 motor control system are described. Due to the different
operating modes, the arrangement of the electric wiring changes depending on the intended application.
Binary
The "Binary" operating mode offers up to 32 individual positioning movements parameterised with different motion types and
movement data such as accelerations and velocities. It is possible to generate a simple programme sequence executed via the
user interface or control it entirely with a higher-level control system via the Digital Inputs/Outputs
In addition, the target position of the command can be specified in the absolute reference system of the axis or relative to the
current position.
It is possible to execute manually controlled movements via the user interface.
Tipp/Teach
With the "Tipp/Teach" mode, positioning movements can be executed by external switches. The motor can be moved manually
with these external switches in the desired direction at a pre-set acceleration and velocity.
Up to 8 individual positioning movements can be pre-set via the user interface. The target positions can be altered with the
external switches without the user interface being used.
Step/Direction
In the "Step/Direction" mode, a step frequency and a direction signal are applied to the dryve D1 motor control system by a
master controller. The acceleration and the speed are fed to Digital Input 1 and the movement direction is fed to Digital Input 2.
BUS communication
The dryve D1 motor control system can be controlled by an external higher-level control system via the CANopen protocol or
the Modbus TCP Gateway protocol.