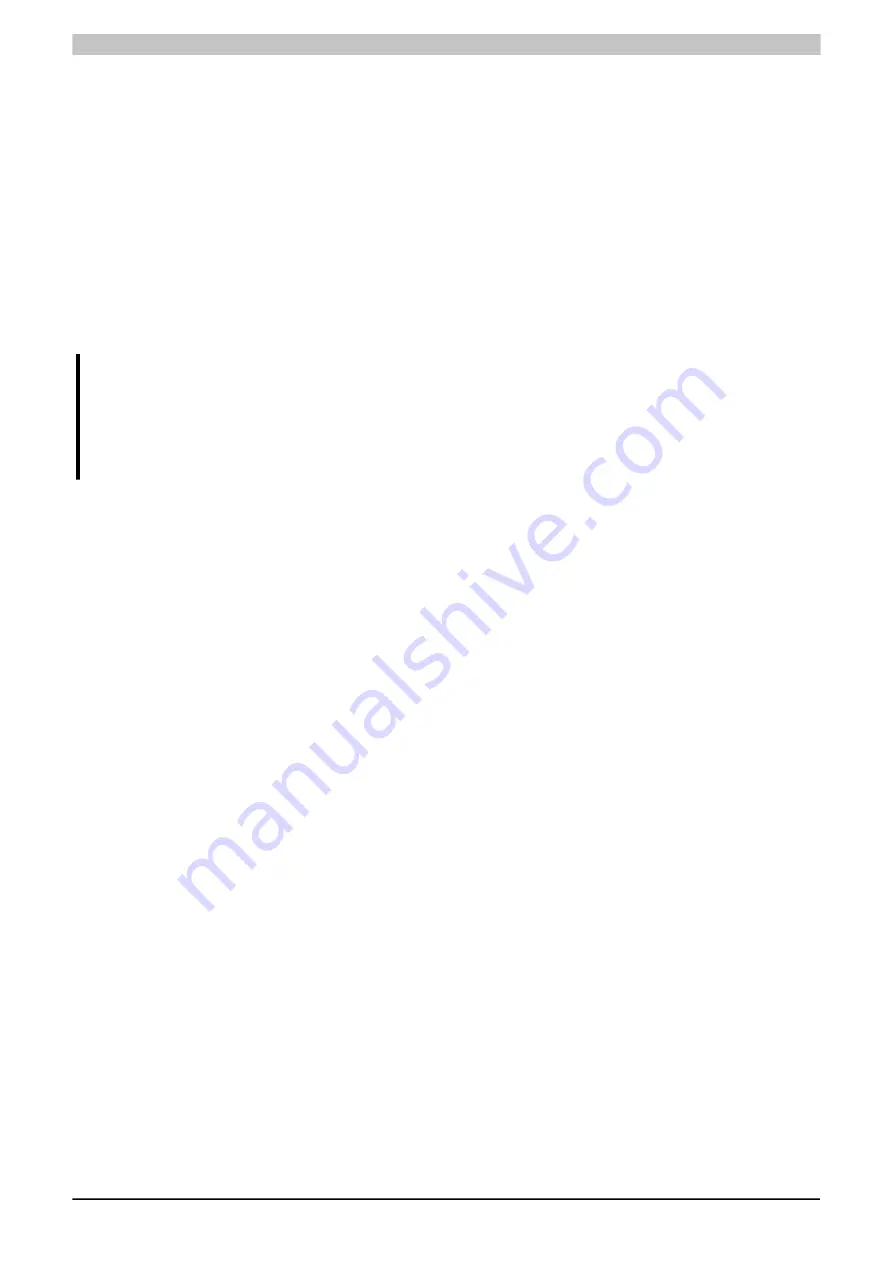
Programming guidelines
220
ACOPOSinverter P84 User's Manual 2.10
2.8.11.11 Brake logic
Used to control an electromagnetic brake by the inverter, for horizontal and vertical hoisting applications, and for
unbalanced machines.
Principle:
Vertical hoisting movement:
Maintains the increase in motor torque during the brake engagement and release phases, for holding the load and
for smooth starting when the brake is released and for smooth stopping when the brake is engaged.
Horizontal hoisting movement:
Synchronize brake release with the build-up of torque during startup and with the brake engagement at zero fre-
quency on stopping, to prevent jolting.
Recommended settings for brake logic control for a vertical hoisting application:
Warning!
ACCIDENTAL OPERATION OF DEVICE
Check that the selected settings and configurations will not result in the dropping or loss of control
of the load being lifted.
Failure to follow these instructions will result in death or serious injury.
1. Brake impulse
(bIP)
: YES. Make sure that the forward direction of operation corresponds to hoisting the load.
For applications in which the lowered load differs very much from the raised load, set
bIP
= 2
Ibr
(Example:
Always lift with a load and lower in the empty state).
2. Brake opening current (
Ibr
and
Ird
if
bIP
= 2
Ibr
): Set the brake release current to the rated current according
to the nameplate of the motor.
When testing, adjust the brake release current to achieve slip-free holding of the load
3. Acceleration time: For hoisting applications it is advisable to set the acceleration ramps to at least 0.5 seconds.
Check that the inverter does not go into current limit mode.
The same recommendation also applies to deceleration.
Please note: For a hoisting movement, a braking resistor must be used.
4. Brake release delay
(brt)
: Set this value depending on the type of brake. This is the time required for the
mechanical brake to release.
5. Brake engage rate
(blr)
only in the open control loop: Leave in
[Auto]
mode and align if necessary.
6. Brake release rate
(bEn)
: leave in
[Auto]
mode and align if necessary.
7. Brake release time
(bEt)
: Set this value depending on the type of brake. It is the time required for the me-
chanical brake to engage.
Recommended settings for brake logic control for a horizontal hoisting application:
1. Brake impulse
(bIP)
: No.
2. Brake engage current
(Ibr)
: Set to 0.
3. Brake engage time
(brt)
: Set this value depending on the type of brake. This is the time required for the
mechanical brake to release.
4. Brake release rate
(bEn)
only in the open control loop: Leave in
[Auto]
mode and align if necessary.
5. Brake release time
(bEt)
: Set this value depending on the type of brake. It is the time required for the me-
chanical brake to engage.
Summary of Contents for ACOPOSinverter P84
Page 2: ......
Page 391: ...Accessories ACOPOSinverter P84 User s Manual 2 10 391 4 7 2 Installation 8I0XF084 020 1...
Page 392: ...Accessories 392 ACOPOSinverter P84 User s Manual 2 10 8I0XF084 030 1...
Page 393: ...Accessories ACOPOSinverter P84 User s Manual 2 10 393 8I0XF084 040 1...
Page 394: ...Accessories 394 ACOPOSinverter P84 User s Manual 2 10 8I0XF084 050 1...
Page 395: ...Accessories ACOPOSinverter P84 User s Manual 2 10 395 8I0XF084 0x0 1...
Page 400: ...Accessories 400 ACOPOSinverter P84 User s Manual 2 10...