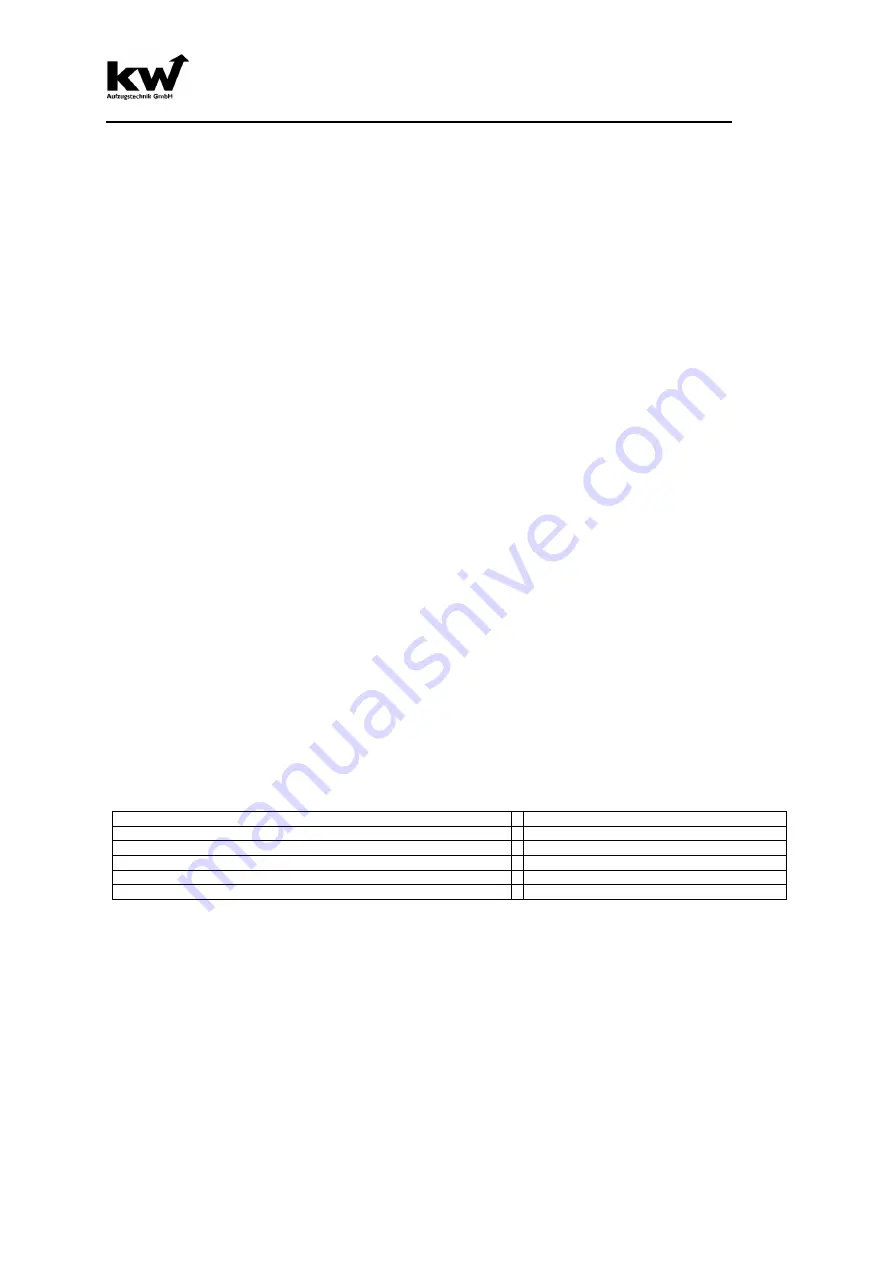
KW Aufzugstechnik GmbH OPERATING MANUAL DAVID-613
DAVID-D613-V125-E 13.04.2021
Page - 229 -
I03-
Commissioning with digital absolute copying without shaft switches
1.0 Examination of the electrical installations and attitude of the pre-end switch
All switches in the safety circuit should be attached. The absolute value device system should be func-
tionally installed. This can be on the car or at the switchboard. The entrances are presented in the
connection diagram.
(Page S-07).
2.0 Allocation of the compactness
You scolded “consice input” in the menu on the attitude floor height. Now you can register for each floor
the value in the millimeter (e.g. HS01-0000mm, HS02-3000mm). After all floors were reserved you scold
back on the attitude concise correction.
3.0 Execution of the determination of the „counter direction“
The control does not know yet the counting direction of the ABS-absolute-value-encoder. The factory
setting value of the parameter counter direction is “negative”. Set from there the value to “
lerning: Drive
Downward
” and proceed the car with the manual control (releveling control or inspection control) a
small piece more deeply until the control terminates the trip. The control learned the counting direction
now.
4.0 Execution of the synchronisation in the lowest stop
Now the ABS-absolute-value-encoder with the control must be synchronized meaning the controller has
to allocate the announced impulse conditions of the abs giver of the individual floors. In addition you
drive the car with the manual control (releveling control or inspection control) into the lowest floor con-
cisely and activate the menu option synchronizing HS01.
5.0 Choice of the driving speeds by adjusting the braking distances
If you want to use only the speed of V3 at your lift, then you can give a pair of car calls now in order to
examine the approach mode the plant. If you want to drive in addition with the V1 and/ or V2, or even
short trip stops to have must enter you the delay ways for V1 and/or V2.
Please consider during the input:
braking distance V1 < Braking distance V2 < Braking Distance V3
With the choice of the braking distance you also specify, with which speed the elevator control starts the
stops. If a delay way for a speed was set to the value zero then this speed is no longer used by the
control. E.g. the floor distance of two floor is smaller than the entered value “ B43 delay in V3” during
this trip the speed of V2 is selected automatically ( e.g. floor trip with fast plants). The floor distance is
smaller than the entered value “B43 delay in V2” during this trip the speed of V1 is selected automatically
( e.g. short trip stop). The foor distance is smaller than the entered value “ B42 delay in V1” during this
trip the speed of V0 is selected automatically ( extreme short trip stop, few cm).
The parameters delay V0-> 0 and delay V3 must always exhibit a value.
Braking distance at 0,8 m/s
2
Deceleration
Maximum Speed
1000 mm
0,63 m/s
1200 mm
1,00 m/s
1800 mm
1,25 m/s
2300 mm
1,60 m/s
3000 mm
2,00 m/s
6.0 Measurement of the level is not ok and correction of the concise values
The control was now examined i.e. the car does not overdrive the stops and drive in the cab is possible.
Connect your HPG60 with the car calling in the car. From there out comfortably the “level is not ok” can
be measured and will enter directly into the system. Go with the car into the first stop and select the
parameter concise value level 1. Retaining inaccuracies are stopped by operation of the yellow plus or
Minus-Buttons.
If your car stands too highly then you register the millimeter value which your car stands too
highly by, thorugh manipulating of the Minus-Button.
If your car stands too low then by manipulation of the plus button the millimeter value is regis-
tered which your car stands too low by.
The determined concise value is corrected automatically.
Repeat the procedure for the other stops.
Содержание DAVID 613
Страница 1: ...OPERATING MANUAL LIFT CONTROLLER SYSTEM DAVID 613 FUNCTIONS START UP INSTRUCTIONS...
Страница 2: ...KW Aufzugstechnik GmbH OPERATING MANUAL DAVID 613 DAVID D613 V125 E 13 04 2021 Page 2...
Страница 7: ...KW Aufzugstechnik GmbH OPERATING MANUAL DAVID 613 DAVID D613 V125 E 13 04 2021 Page 7 8 INDEX 263...
Страница 10: ...KW Aufzugstechnik GmbH OPERATING MANUAL DAVID 613 DAVID D613 V125 E 13 04 2021 Page 10...
Страница 12: ...KW Aufzugstechnik GmbH OPERATING MANUAL DAVID 613 DAVID D613 V125 E 13 04 2021 Page 12...
Страница 13: ...KW Aufzugstechnik GmbH OPERATING MANUAL DAVID 613 DAVID D613 V125 E 13 04 2021 Page 13...
Страница 14: ...KW Aufzugstechnik GmbH OPERATING MANUAL DAVID 613 DAVID D613 V125 E 13 04 2021 Page 14...
Страница 34: ...KW Aufzugstechnik GmbH OPERATING MANUAL DAVID 613 DAVID D613 V125 E 13 04 2021 Page 34...
Страница 35: ...KW Aufzugstechnik GmbH OPERATING MANUAL DAVID 613 DAVID D613 V125 E 13 04 2021 Page 35...
Страница 98: ...KW Aufzugstechnik GmbH OPERATING MANUAL DAVID 613 DAVID D613 V125 E 13 04 2021 Page 98...
Страница 124: ...KW Aufzugstechnik GmbH OPERATING MANUAL DAVID 613 DAVID D613 V125 E 13 04 2021 Page 124 Unit shaft copying system...