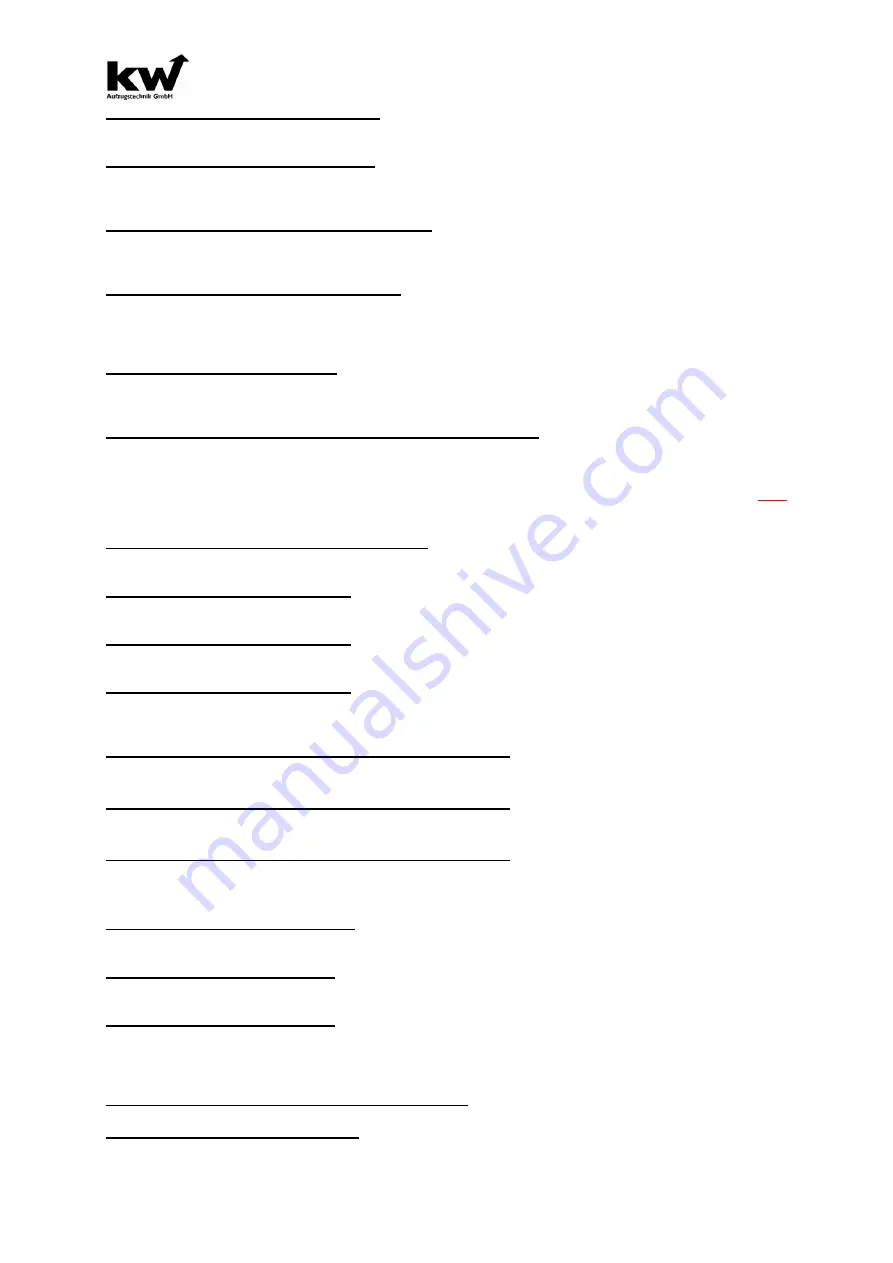
KW Aufzugstechnik GmbH OPERATING MANUAL DAVID-613
DAVID-D613-V125-E 13.04.2021
Page - 107 -
PARAMETER: PULSE BUFFER DELAY
There is a pulse buffer-delay-time between 2 and 150ms. It depends on the type of magnets, you are using. The
KW-magnets only needs a delay-time of 2ms.
PARAMETER: CORRECTION TRAVEL
If it comes in the shaft copying to false countings, a correction trip goes on. The time of execution can takes place
”after call-input” or immediately in “automatic“ mode.
PARAMETER: 2.PRE- END- SWITCH BOTTOM
There is a golden rule that the pre-end switch bottom must be between 1. and 2. stop. If the 2. stop is a short trip
stop, then the distance pre-end switch would not be sufficient down to the zone of the 1. stop with a faulty meas-
urement to brake the carconcisely.
PARAMETER: 2.PRE –END- SWITCH TOP
There is a golden rule that the pre-end switch bottom must be between last and pre-last stop. If the pre-last stop is
a short trip stop, then the distance pre-end switch would not be sufficient down to the zone of the last stop with a
faulty measurement to brake the carconcisely.
In this situation the 2. pre-end-switch can be placed between the
pre-last- and pre-pre-last-floor.
PARAMETER: SHORT TRAVELS
Extreme short trip stops are appropriate for two stops within a zone. With this parameter it is adjusted whether this
case is present and if like many of these short trip stops is present.
PARAMETER: DISTANCE PRE-END-SWITCH-ZONE BOTTOM
In this parameter the distance center magnet pre-end switch is registered down to the highest magnet of the lowest
zone in mm. This value must be determined absolutely accurately. It is important for the perfect functioning of the
digital shaft copying.
Attention! With hydraulic, unsetteled rope and variable voltage rope plants the input the delay way of both
direction takes place. (UP and DOWN-Direction)! With hydraulic and there however only V0 and V-fast are
unsetteled rope plants to stop!
PARAMETER: DECELERATION SPEED V0->0
This parameter is the brake-way from the drive-in speed V0 to the stop (0). The value comes automatically by the
learn drive. Nevertheless the value can be change per hand.
PARAMETER: DECELERATION V1
This parameter is the brake-way from the speed V1 to the drive-in speed V0. This value depends on the speed V1
and the deceleration in the inverter. The standard value is 500 mm.
PARAMETER: DECELERATION V2
This parameter is the brake-way from the speed V2 to the drive-in speed V0. This value depends on the speed V2
and the deceleration in the inverter. The standard value is 1000 mm.
PARAMETER: DECELERATION V3
This parameter is the brake-way from the speed V3 to the drive-in speed V0. This value depends on the speed V3
and the deceleration in the inverter. The standard value is 1500 mm.
PARAMETER: TRAVEL BY V0 – IF DISTANCE < xxxx mm
If the distance to the target floor is smaller than the specified distance xxxx mm, the speed V0 is selected,
regardless of the value set in the parameter Delay at V1.
PARAMETER: TRAVEL BY V1 – IF DISTANCE < xxxx mm
If the distance to the target floor is smaller than the specified distance xxxx mm, the speed V1 is selected,
regardless of the value set in the parameter Delay at V2.
PARAMETER: TRAVEL BY V2 – IF DISTANCE < xxxx mm
If the distance to the target floor is smaller than the specified distance xxxx mm, the speed V2 is selected,
regardless of the value set in the parameter Delay at V3.
PARAMETER: LEARN DRIVE WITH
For the learn drive you can choose three speeds like, V1, V2, and V3. If you have a drive with a short distance, you
should chosse speed V1. The standard value is speed V1.
PARAMETER: ENCODER INPUT
The encoder for the shaft copying can attache on the Car (FKR) or the machine room (ZR). The location is to be
registered in this parameter. As default value ZR is deposited.
PARAMETER: DRIVE ACTIVATE
If the electrical installation is fine and the software-parameters like number of floors,..., is put in, the learn-drive can
be started. The car should be in a position between the first and second floor, but it must stand above the correction
switch bottom. Then the learn-drive should be started. A very concrete description is in the chapter
I01-Activation
of the digital shaft presentation.
PARAMETER: SWITCH HYSTERES OVERLAPPING
After successful learning trip the value of the hysteress was determined for the shaft switches.
PARAMETER: EVELING-FLOOR-XX
After a learn-drive, you must put in this parameter in the level-values for each floor. Here you can correct unlevels
for every floor.
Содержание DAVID 613
Страница 1: ...OPERATING MANUAL LIFT CONTROLLER SYSTEM DAVID 613 FUNCTIONS START UP INSTRUCTIONS...
Страница 2: ...KW Aufzugstechnik GmbH OPERATING MANUAL DAVID 613 DAVID D613 V125 E 13 04 2021 Page 2...
Страница 7: ...KW Aufzugstechnik GmbH OPERATING MANUAL DAVID 613 DAVID D613 V125 E 13 04 2021 Page 7 8 INDEX 263...
Страница 10: ...KW Aufzugstechnik GmbH OPERATING MANUAL DAVID 613 DAVID D613 V125 E 13 04 2021 Page 10...
Страница 12: ...KW Aufzugstechnik GmbH OPERATING MANUAL DAVID 613 DAVID D613 V125 E 13 04 2021 Page 12...
Страница 13: ...KW Aufzugstechnik GmbH OPERATING MANUAL DAVID 613 DAVID D613 V125 E 13 04 2021 Page 13...
Страница 14: ...KW Aufzugstechnik GmbH OPERATING MANUAL DAVID 613 DAVID D613 V125 E 13 04 2021 Page 14...
Страница 34: ...KW Aufzugstechnik GmbH OPERATING MANUAL DAVID 613 DAVID D613 V125 E 13 04 2021 Page 34...
Страница 35: ...KW Aufzugstechnik GmbH OPERATING MANUAL DAVID 613 DAVID D613 V125 E 13 04 2021 Page 35...
Страница 98: ...KW Aufzugstechnik GmbH OPERATING MANUAL DAVID 613 DAVID D613 V125 E 13 04 2021 Page 98...
Страница 124: ...KW Aufzugstechnik GmbH OPERATING MANUAL DAVID 613 DAVID D613 V125 E 13 04 2021 Page 124 Unit shaft copying system...