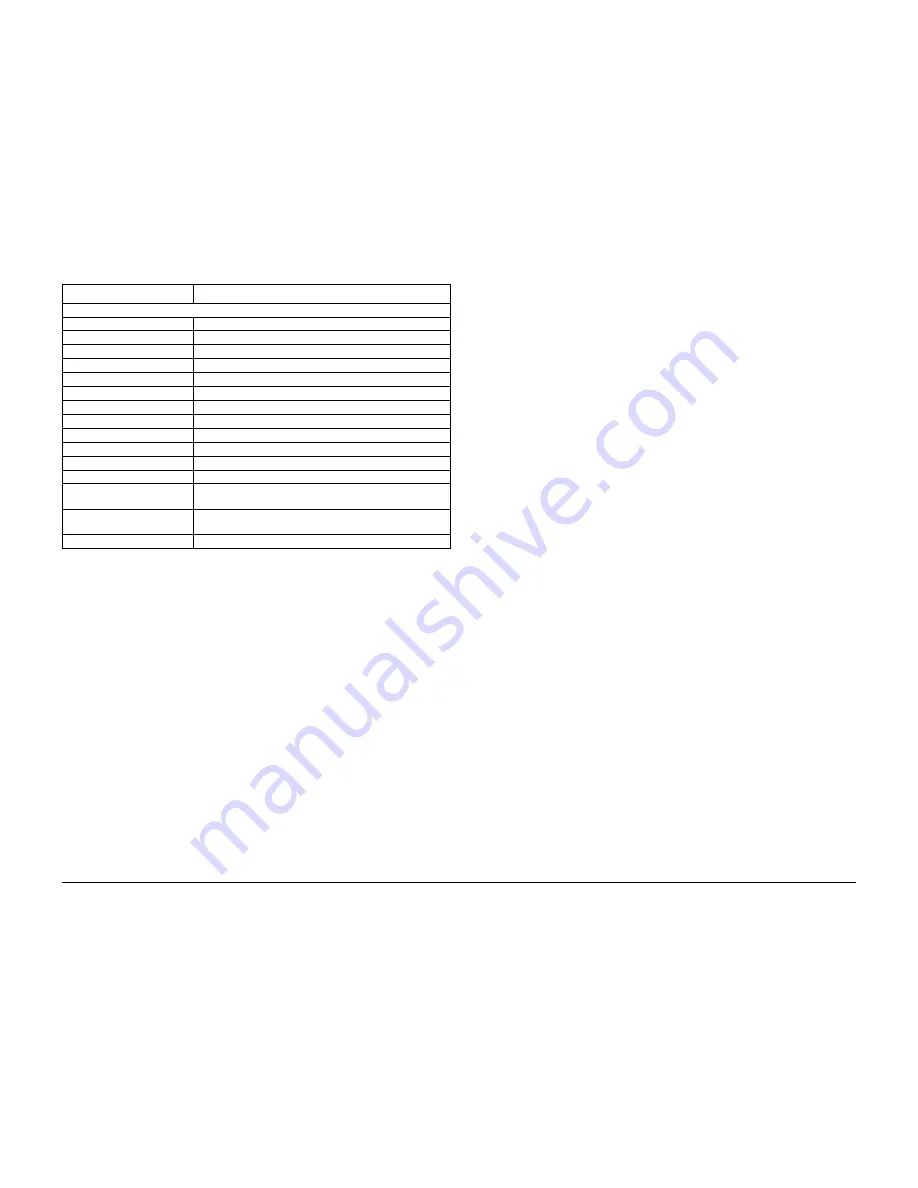
10/2006
1-4
Phaser 8510/8560MFP Multifunction Product
Service Call Procedures, Initial Actions
Initial Issue
Service Call Procedures
Initial Actions
Purpose
Use the following procedure to determine the reason for the service call and to identify and
organize the actions which must be performed.
Procedure
1.
Gather the information about the service call and the condition of the copier/printer.
a.
Question the operator(s). Ask about the location of most recent paper jams. Ask
about the image quality and the copier/printer performance in general, including any
unusual sounds or other indications.
b.
After informing the customer that the machine will not be available for copying and
printing, disconnect the machine from the customer’s network.
c.
If a new installation, be sure all packing material is removed.
d.
Check that the power cords are in good condition, directly plugged in to the power
source, and free from defects. Repair or replace the power cords as required. Check
that the circuit breaker, if present, is not tripped.
e.
If the system appears is inoperative, go to Electrical Troubleshooting and repair the
problem. Then continue below.
f.
Inspect any rejected copies. Inquire as to, or otherwise determine, the paper quality
and weight. Print the Paper Tips page for specific media specifications. Look for any
damage to the copies, oil marks, image quality defects, or other indications of an
unreported problem.
NOTE: If a fault code is displayed while performing a diagnostics procedure, go to
that fault code RAP and repair the fault. Return to Diagnostics and continue with the
procedure that you were performing.
g.
Display and review the information in the Fault History, Jam History, Service Usage
Profile. Classify this information into categories:
Information that is related to the problem that caused the service call.
Information that is related to secondary problems.
Information that does not require action, such as a single occurrence of a prob-
lem.
2.
Perform any required routine maintenance activities. Refer to the Routine Maintenance
Activities section.
3.
If any DADF feed jams are reported, or fault codes are logged, replace the Feed Roll Kit.
4.
Try to duplicate the problem by running the same jobs that the customer ran once repairs
are complete to verify repairs are effective.
5.
Go to General Procedures to further investigate the problem.
Optional Tools
Canned Air
3 -Prong Claw Part-Retriever
Pointer with Magnetized Head
Tweezers
Utility Knife
Dental Mirror
Screw Box
Soldering Iron
Heat Shrink tubing
Electrical Tape
Jeweler's Screwdriver Kit
Precision/Hobby tool set
phillips, flathead, pliers, small torx drivers
Serial & Parallel Loop Back
Plugs
Bootable CDs and Floppy
Disks
IC Chip Puller
Table 1 Service Tools
Description
Detail
Summary of Contents for PHASER 8560MFP
Page 1: ...701P01133 October 2006 Phaser 8560MFP Multifunction Product Service Documentation...
Page 4: ...10 2006 iv Phaser 8510 8560MFP Multifunction Product Initial Issue Introduction...
Page 22: ...10 2006 1 2 Phaser 8510 8560MFP Multifunction Product Initial Issue Service Call Procedures...
Page 28: ...10 2006 2 2 Phaser 8510 8560MFP Multifunction Product Initial Issue Error Messages and Codes...
Page 84: ...10 2006 3 2 Phaser 8510 8560MFP Multifunction Product Initial Issue Image Quality...
Page 116: ...10 2006 4 2 Phaser 8510 8560MFP Multifunction Product Initial Issue Repairs and Adjustments...
Page 194: ...10 2006 5 2 Phaser 8510 8560MFP Multifunction Product Initial Issue Parts List...
Page 204: ...10 2006 6 2 Phaser 8510 8560MFP Multifunction Product Initial Issue Diagnostics...
Page 256: ...10 2006 7 2 Phaser 8510 8560MFP Multifunction Product Initial Issue Wiring Data...
Page 274: ...10 2006 8 2 Phaser 8510 8560MFP Multifunction Product Initial Issue Theory of Operation...