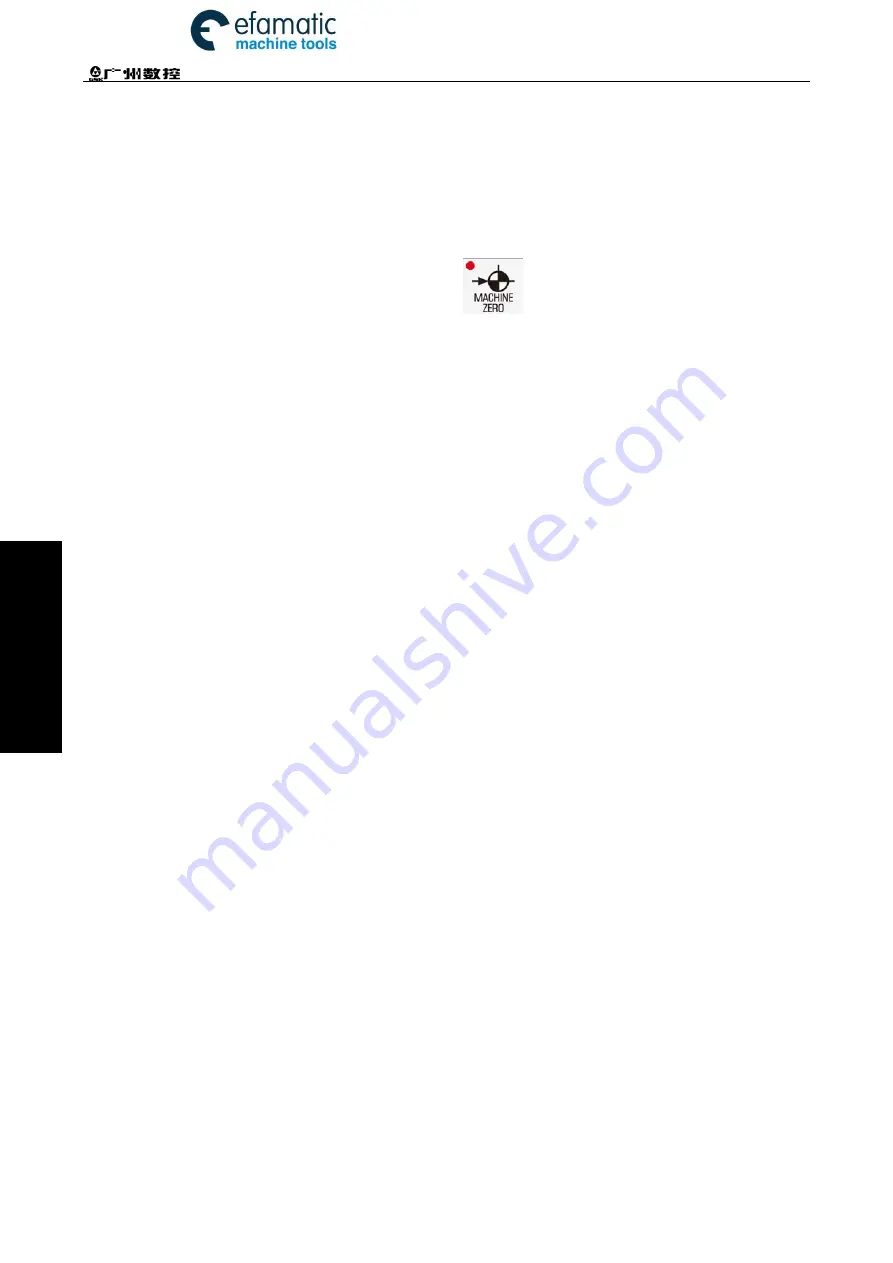
Official GSK Agents in South Africa
Tel: +27 11 626 2720, [email protected]
GSK218MC Series Machining Center CNC System PLC&Installation Connetion Manual
218
V
o
lume IV
Inst
allation
&
Connecti
o
n
single-core absolute, multi-core absolute version. And set that the parameters
P347~P351
can be
modified the single-core zero signal position of the absolute encoder. The zero return along with each
axis is enabled in the zero return method.
Zero return step:
1.
Enter mechanical zero operation method by
button, in this case, the “Mechanical
zero” displays at the lower right corner on the LCD.
2.
Select the X, Y, Z, 4
th
or 5
th
axis to be returned to the mechanical zero, and the zero return
direction is determined by bit parameter
N0:7#0
~
N0:7#4.
3.
The machine moves along with the mechanical zero rapidly (The movement velocity is
determined by parameters
P100
~
P104
) before the deceleration point. The data parameters
P342~P346
set the zero return velocity along with each axis after meeting the declaration
switch, and then inquires the pulse Z one-turn signal position continually based upon the
velocity set by the data parameter
P342~P346,
after releasing from the block; it decelerates
to stop after inspecting, and then return to the mechanical point (that is reference position)
based upon the velocity set by data parameter
P354
. The coordinate axis stops movement
after returning to the mechanical zero, the zero return indicator is then lighted up.
For example:
The common increment zero of the 1
st
axis is regarded as the example, the 1
st
axis begins to
impact the block based upon the higher velocity F4000 (Data parameter
P100
sets to 4000); F500
(Data parameter
P342
sets to 500) passes through the block after touching the deceleration switch;
search the one-turn Z pulse signal of the servo based upon the very slow velocity F40 (Data parameter
P99
sets to 40) after releasing from the block; it immediately stops after capturing; refer to the Fig.
4-8-1-4.
The common increment zero return along with the 1
st
axis is regarded as an example. Impact the
block with the higher velocity F4000 (Data parameter
P100
sets as 4000) at the beginning of the 1
st
axis, pass through the block based upon the F500 (Data parameter
P342
sets to 500) after touching
the deceleration switch, and then check the one-turn pulse z signal position based upon the F5000
velocity after releasing from the block; it decelerates to stop after inspecting, and then return to the
mechanical zero based upon the F200 velocity (Data parameter
P354
sets to 200); refer to the Fig.
4-8-2-1: