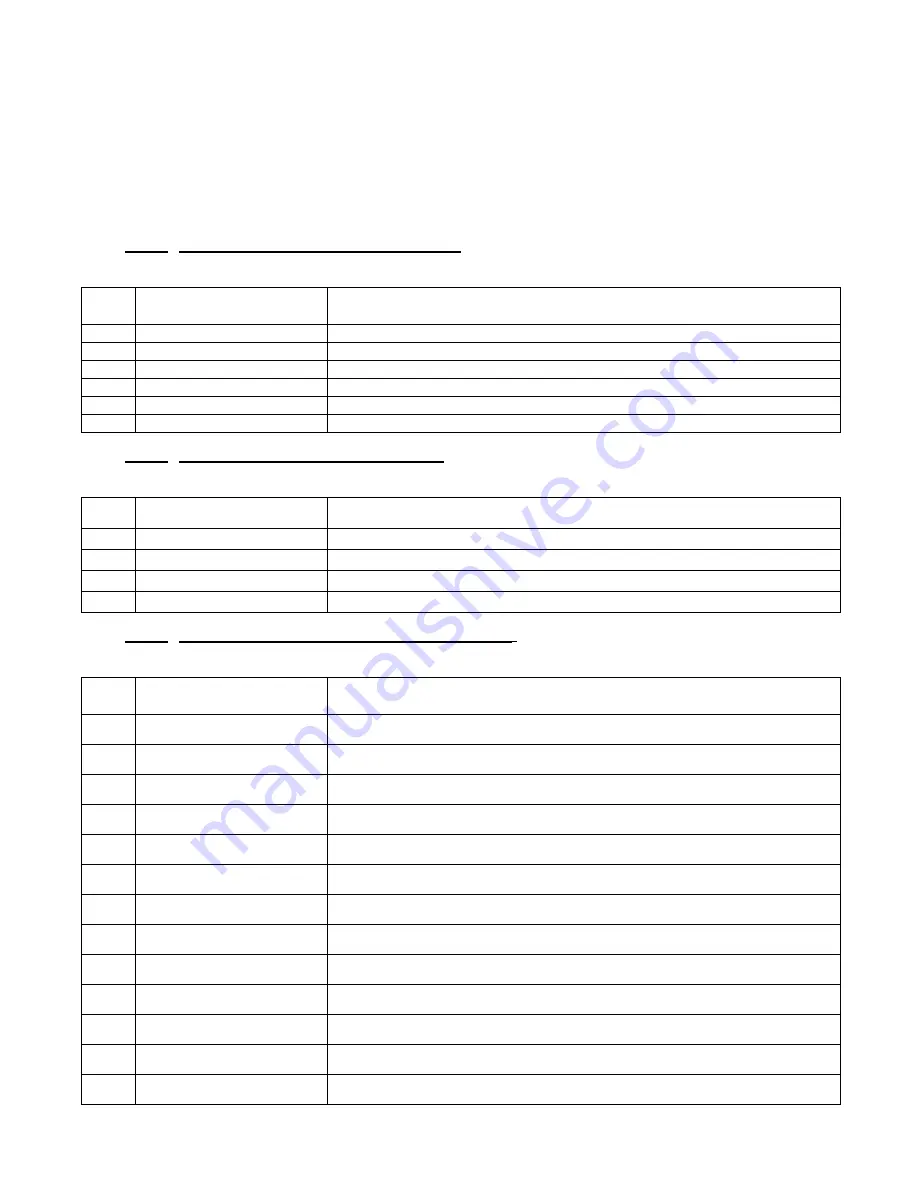
TROUBLESHOOTING
PageB8-1
B8 ERROR CODES
As stated previously, if a problem with the Control Sys-
tem is detected, the Processor is programmed to display
numerous Error Codes to aid in the isolation of the
cause. The following tables list these Error Codes, along
with a brief description
.
B8-4 C
LUTCH
S
OLENOID
E
RROR
C
ODES
B8-5 T
ROLL
S
OLENOID
E
RROR
C
ODES
B8-6 B
ASIC
C
ONTROL
S
YSTEM
E
RROR
C
ODES
Table B8-4: Clutch Solenoid Control System Error Codes
Error
No.
Title
Description
1
Clutch Astern Shorted
The Astern Clutch Solenoid is requiring more current than expected.
2
Clutch Astern Open
The Astern Clutch Solenoid should be drawing current but is not.
3
Clutch Neutral Shorted
The Neutral Clutch Solenoid is requiring more current than expected.
4
Clutch Neutral Open
The Neutral Clutch Solenoid should be drawing current but is not.
5
Clutch Ahead Shorted
The Ahead Clutch Solenoid is requiring more current than expected.
6
Clutch Ahead Open
The Ahead Clutch Solenoid should be drawing current but is not.
Table B8-5: Troll Solenoid Control System Error Codes
Error
No.
Title
Description
7 Troll ON/OFF Shorted
The Troll ON/OFF Solenoid is requiring more current than expected.
8 Troll ON/OFF Open
The Troll ON/OFF Solenoid should be drawing current but is not.
9 Troll Command Shorted
The Troll Proportional Solenoid is requiring more current than expected.
10 Troll Command Open
The Troll Proportional Solenoid should be drawing current but is not.
Table B8-6: Basic Control System Error Codes
Error
No.
Title
Description
13
Station No.1
Faulted High
Station No.1 Control Head’s lever position is out of range.
The input appears to be too high.
14
Station No.2
Faulted High
Station No.2 Control Head’s lever position is out of range.
The input appears to be too high.
15
Station No.3
Faulted High
Station No.3 Control Head’s lever position is out of range.
The input appears to be too high.
16
Station No.4
Faulted High
Station No.4 Control Head’s lever position is out of range.
The input appears to be too high.
17
Station No.5
Faulted High
Station No.5 Control Head’s lever position is out of range.
The input appears to be too high.
18
Station No.6
Faulted High
Station No.6 Control Head’s lever position is out of range.
The input appears to be too high.
19
Station No.7
Faulted High
Station No.7 Control Head’s lever position is out of range.
The input appears to be too high.
20
Station No.8
Faulted High
Station No.8 Control Head’s lever position is out of range.
The input appears to be too high.
21
Station No.9
Faulted High
Station No.9 Control Head’s lever position is out of range.
The input appears to be too high.
22
Station No.10
Faulted High
Station No.10 Control Head’s lever position is out of range.
The input appears to be too high.
23
Station No.1
Faulted Low
Station No.1 Control Head’s lever position is out of range.
The input appears to be too low.
24
Station No.2
Faulted Low
Station No.2 Control Head’s lever position is out of range.
The input appears to be too low.
25
Station No.3
Faulted Low
Station No.3 Control Head’s lever position is out of range.
The input appears to be too low.
Содержание ClearCommand 9000 Series
Страница 1: ...ClearCommand 9000 Series Installation Operation and Troubleshooting Manual MM9000 I Rev C 2 5 08...
Страница 132: ......
Страница 133: ...APPENDIX A...
Страница 134: ......
Страница 139: ......
Страница 140: ...Page A 4...
Страница 143: ......
Страница 144: ...10...
Страница 148: ...Page A 18...
Страница 149: ...Page A 19 TEMPLATE...
Страница 150: ...Page A 20...
Страница 152: ...Page A 22...
Страница 154: ...Page A 24...
Страница 156: ...Page A 26...
Страница 157: ...Page A 27 Drawing 11488D 1 Twin Screw Single APS Connection Alternate Remote Switch...
Страница 158: ...Page A 28...
Страница 159: ...Page A 29 Drawing 11488D 2 Twin Screw Dual APS Connections...
Страница 160: ...Page A 30...
Страница 161: ...Page A 31 Drawing 11488D 3 APS Notes Page...
Страница 162: ...Page A 32...
Страница 164: ...Page A 34...
Страница 166: ...Page A 36...
Страница 170: ...Page A 40...
Страница 172: ...Page A 42...
Страница 176: ...Page A 46...
Страница 178: ...Page C 48 ZF Mathers LLC 12125 Harbour Reach Drive Suite B Mukilteo WA 98275...
Страница 179: ...APPENDIX B...
Страница 180: ......
Страница 234: ...Appendix B 6...
Страница 238: ...Appendix B 10...
Страница 242: ...Appendix B 14...
Страница 247: ...Service Field Test Unit Reference Manual MM13927 Rev E 4 07...
Страница 248: ......
Страница 250: ...Page ii Table of Contents...
Страница 264: ...SERVICE FIELD TEST UNIT MM13927 RvD 10 03 Page 3 2...
Страница 265: ...APPENDIX C...
Страница 266: ......
Страница 267: ...Appendix C 1 Drawing 12284A 1 ClearCommand Diagram all options...
Страница 268: ...Appendix C 2...
Страница 269: ...Appendix C 3 Drawing 12284A 2 ClearCommand Circuit Board Connections...
Страница 270: ...Appendix C 4...
Страница 271: ...Appendix C 5 Drawing 12284A 3 ClearCommand Drawing Notes Page...
Страница 272: ...Appendix C 6...