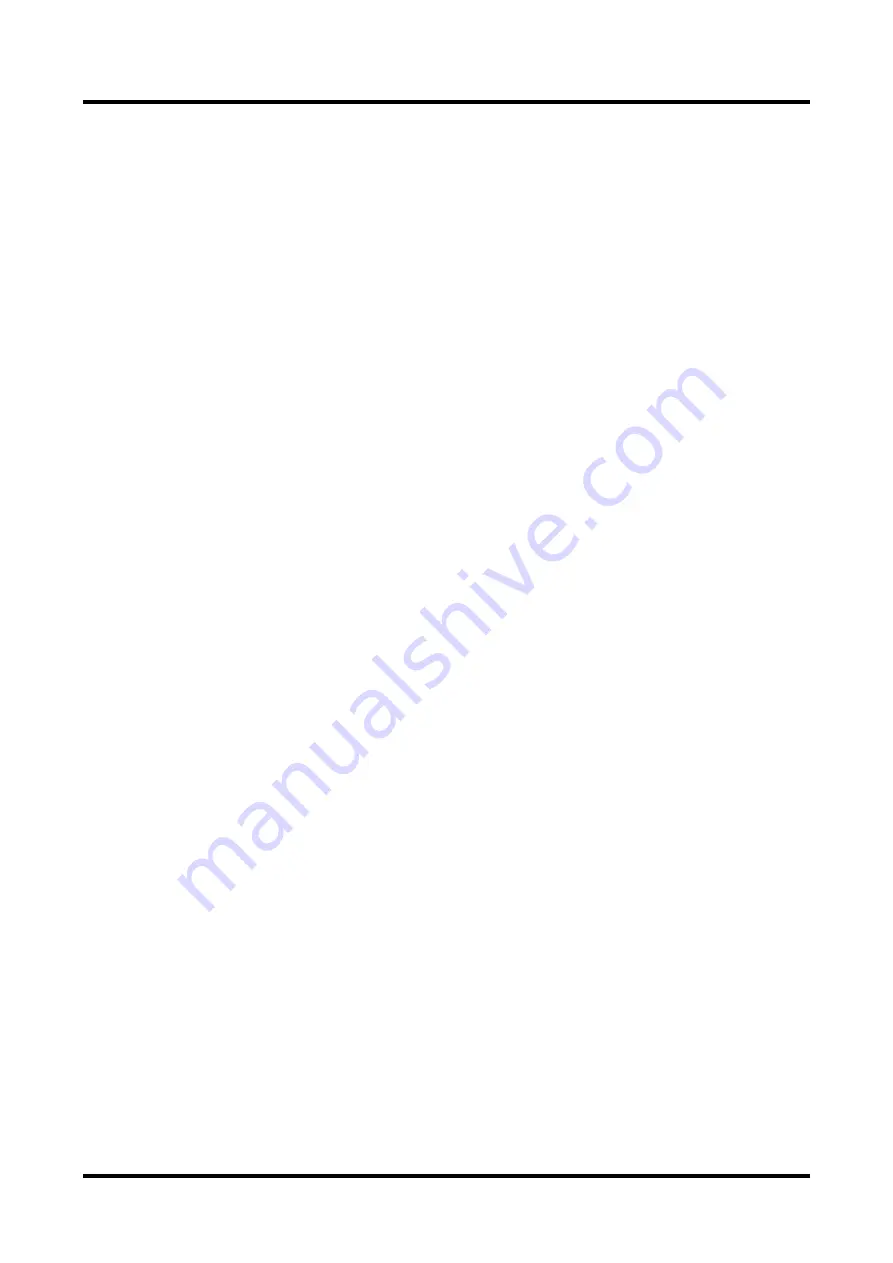
Appendix 4-6
TI71M01D06-01EN 3rd Edition: 2012.12.01
Main Power
A power supply for operating the motor
Maker Data
Internal data set up by Yokogawa. This data cannot be set up by users. It cannot be erased by
all reset operation. (Basic data, adjustment data)
Manual Tuning
An operation for adjusting each control parameter by operating the motor via a test operation
and then using an oscilloscope and the utility software functions.
Master
Indicates the master motor/drive in a master and slave relation in tandem operation.
Maximum Output Torque
The motor's output torque when driving at the drive's maximum output current. The maximum
output torque is generated at startup (the velocity is zero) in the case of DD motors.
Maximum overhung load
The motor is fastened to the base and a moment dead load is applied to the rotor's load
mounting area in the direction where the rotor's rotation axis core is tilted. The "maximum
overhung load" is the maximum load when all component parts of the motor are within the
elastic deformation zone. When the load is removed, all the component parts must be
restored to their original states. In addition, the gap between the rotor and the stator core
must not be zero (the core makes contact) in the worst condition.
Maximum Velocity
The maximum velocity a motor can rotate.
Moment displacement stiffness
The motor is fastened to the base and a moment dead load is applied to the rotor's load
mounting area in the direction where the rotor's rotation axis core is tilted within the maximum
overhung load. Moment displacement stiffness is the axis core tilt displacement angle per unit
moment load at this time. "Displacement angle/moment load" must be linear.
Monitor Pulse
Current position value pulse output from the drive
Motorless Operation (Emulation Mode)
A mode for simulating the operations of the motor using only the drive without connecting the
actual motor. This feature is convenient to check general operations of the motor before
starting the system. The utility software is used for simulation.
Mpulse
Unit of pulses obtained by raising 10 to the sixth power
Multichannel Connection
A connection to connect multiple drives to a party line using RS485 communication. A
dedicated DLL is required for control from a PC.
N
O
Operation Display Panel
A separately sold device that is connected to the drive, which displays/edits parameters and
issues commands.