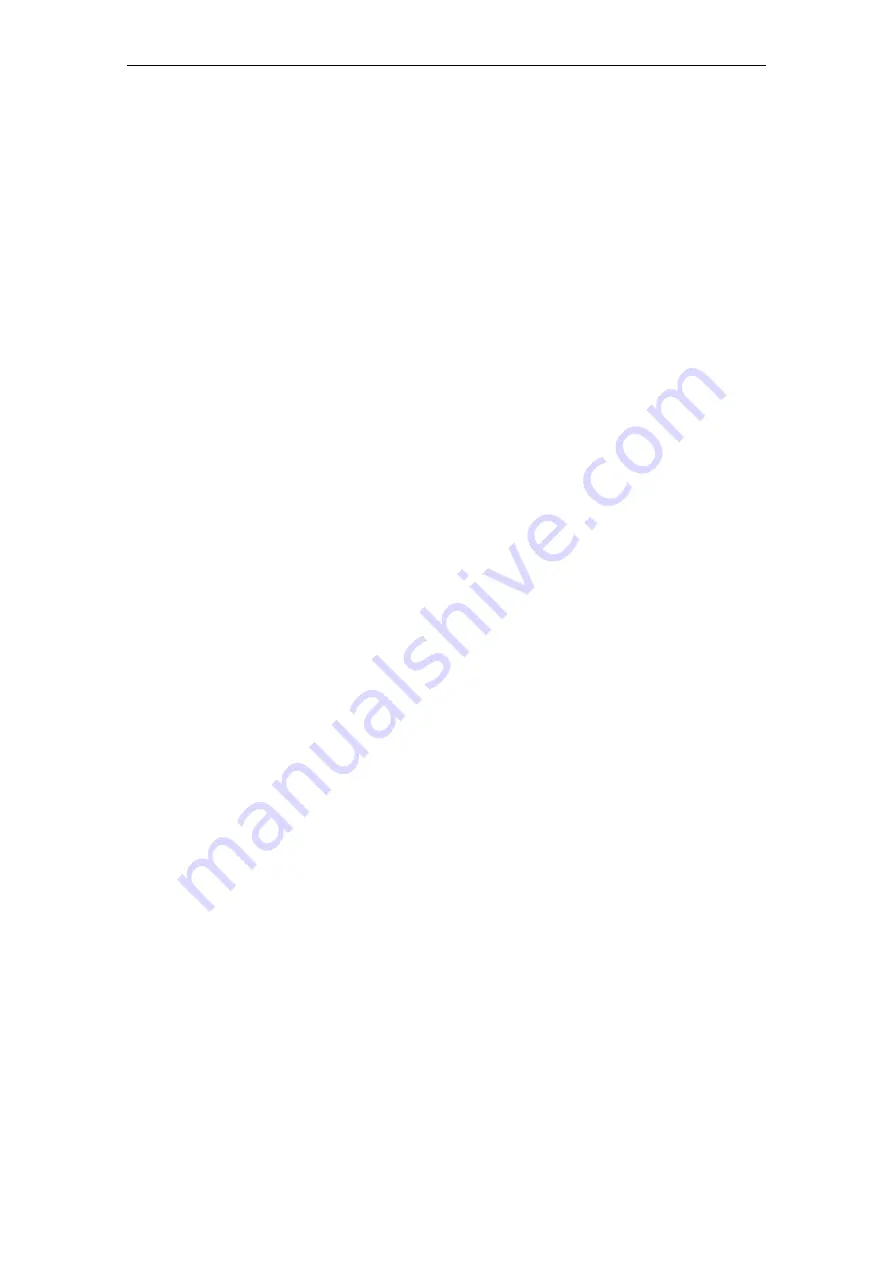
Faults and alarms
List of faults and alarms
3-1120
© Siemens AG 2012 All Rights Reserved
SINAMICS S110 List Manual (LH7), 06/2012, 6SL3097-4AP10-0BP3
207: Elasticity-based pole position identification, no negative measured value found.
It is possible that all measured values are identical. The expected deflection was not able to be reached, either
because the expectation is too high or not enough current was able to be established.
208: Elasticity-based pole position identification, measuring current is 0.
209: Elasticity-based pole position identification, the selected max. distance was exceeded (p3095).
210: Elasticity-based pole position identification without encoder.
250 ... 260:
Elasticity-based pole position identification, more than 3 attempts have been made and fault value 200 ... 210 output.
Example:
Fault value= 253 --> more than 3 attempts have been made and fault value 203 output.
Remedy:
For fault value = 1:
- check the motor connection and DC link voltage.
- for the following parameters, set practical values that are not zero (p0325, p0329).
Re fault value = 1, 2:
- in the case of a large computing time load (e.g., 6 drives with Safety Integrated), set the computing dead time of
the current controller to late transfers (p0117 = 3).
For fault value = 3:
- increase the max. distance (p1981).
- reduce the currents for the pole position identification routine (p0325, p0329).
- stop the motor in order to carry out the pole position identification routine.
For fault value = 5:
- reduce the currents for the pole position identification routine (p0325, p0329).
For fault value = 6:
- re-calibrate the Motor Module.
For fault value = 8:
- reduce the currents for the pole position identification routine (p0329, p0325, p1993).
- the power unit cannot provide the necessary pole position identification routine current (p0209 < p0329, p0325,
p1993), replace the power unit with a power unit with a higher max. current.
For fault value = 9:
- enter a value not equal to zero in the pole position identification routine current (p0329, p0325, p1993).
For fault value = 10:
- do not initiate a data set changeover during the pole position identification.
For fault value = 11:
- for incremental encoders without commutation with zero mark (p0404.15 = 0), it does not make sense to adjust the
encoder to determine the commutation angle (p1990 = 1). In this case, the function should be de-selected (p1990 =
0) or, for an encoder with suitable zero mark, commutation with zero mark should be selected (p0404.15 = 1).
- for absolute encoders, only adjust the encoder to determine the commutation angle (p1990 = 1) if the encoder sup-
plies commutation information and is finely synchronized (p1992.8 = 1 and p1992.10 = 1). The encoder is possibly
parked, de-activated (p0145), not ready for operation or signals a fault condition.
- de-select the encoder adjustment to determine the commutation angle (set p1990 to 0).
Re fault value = 40 ... 49:
- increase the currents for the pole position identification routine (p0325, p0329).
- stop the motor in order to carry out the pole position identification routine.
- select another technique for pole position identification routine (p1980).
- use another motor, absolute encoder or Hall sensors.
Re fault value = 70 ... 79:
- upgrade the software in the Sensor Module.
Re fault value = 100, 101:
- check and ensure that the motor is free to move.
- increase the current for motion-based pole position identification (p1993).
For fault value = 102:
- if the motor is to be operated with a brake: Select a different technique to identify the pole position (p1980).
- if the motor can be operated without a brake: Open the brake (p1215 = 2).
For fault value = 103:
- the motion-based pole position identification can only be carried out using an encoder. Connect an encoder or
select another technique for pole position identification routine (p1980).
For fault value = 104:
- pole position identification, increase the smoothing time, motion-based (p1997).
- pole position identification, increase the rise time, motion-based (p1994).
- pole position identification, check the gain, motion-based (p1995).
- pole position identification, check the integral time, motion-based (p1996).
- for motor encoders with track A/B sq-wave (p0404.3 = 1) and flank time measurement (p0430.20 = 0), disable the
integral time (p1996 = 0).
Содержание SINAMICS S110
Страница 1: ...s SINAMICS S110 List Manual 06 2012 SINAMICS ...
Страница 2: ......
Страница 1272: ...List of abbreviations B 1272 Siemens AG 2012 All Rights Reserved SINAMICS S110 List Manual LH7 06 2012 6SL3097 4AP10 0BP3 ...
Страница 1286: ...Index C 1286 Siemens AG 2012 All Rights Reserved SINAMICS S110 List Manual LH7 06 2012 6SL3097 4AP10 0BP3 ...
Страница 1287: ......