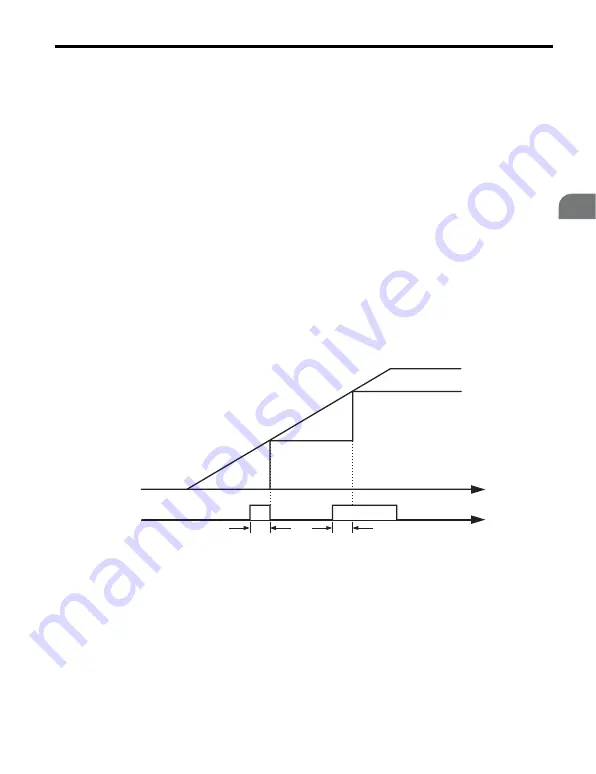
1.7 H: Terminal Functions
YASKAWA ELECTRIC SIEP C710606 10A YASKAWA AC Drive - V1000 PRELIM. Programming Manual
149
Pa
ra
m
et
er D
et
ai
ls
1
Setting 1A: Accel/Decel Time Selection 2
Used to select accel/decel times 3 and 4 in combination with the Accel/Decel Time Selection
1 command. Refer to
C1-01 to C1-08: Accel/Decel Times 1 to 4 on page 77
Setting 1B: Program Lockout
When an input is programmed for Program Lockout, parameters values can be monitored
but not changed as long as this input is open.
Setting 1E: Analog Frequency Reference Sample / Hold
This function allows the user to sample an analog frequency reference signal being input to
terminal A1 or A2 and hold the frequency reference at the sampled level. Once the Analog
Frequency Reference Sample / Hold function is held for at least 100 ms, the drive reads the
analog input and changes the frequency reference to the newly sampled speed as illustrated
in
.
When the power is shut off and the sampled analog frequency reference is cleared, the
frequency reference is reset to 0.
Figure 1.51
Figure 1.51 Analog Frequency Reference Sample/Hold
An oPE03 error will occur when one of the following functions is used simultaneously with
the Analog Frequency Reference Sample / Hold function.
• Hold Accel/Decel Stop (setting: A)
• Up command, Down command (setting: 10, 11)
• Offset Frequency (setting: 44 to 46)
• Up or Down functions (setting: 75, 76)
Frequency
reference
ON (closed)
OFF (open)
Time
Referenece
Sample Hold Input
100 ms
Summary of Contents for OYMC V1000
Page 2: ...2 YASKAWA ELECTRIC SIEP C710606 10A YASKAWA AC Drive V1000 PRELIM Programming Manual...
Page 8: ...8 YASKAWA ELECTRIC SIEP C710606 10A YASKAWA AC Drive V1000 PRELIM Programming Manual INDEX 393...
Page 407: ...YASKAWA ELECTRIC SIEP C710606 10A YASKAWA AC Drive V1000 PRELIM Programming Manual 407...