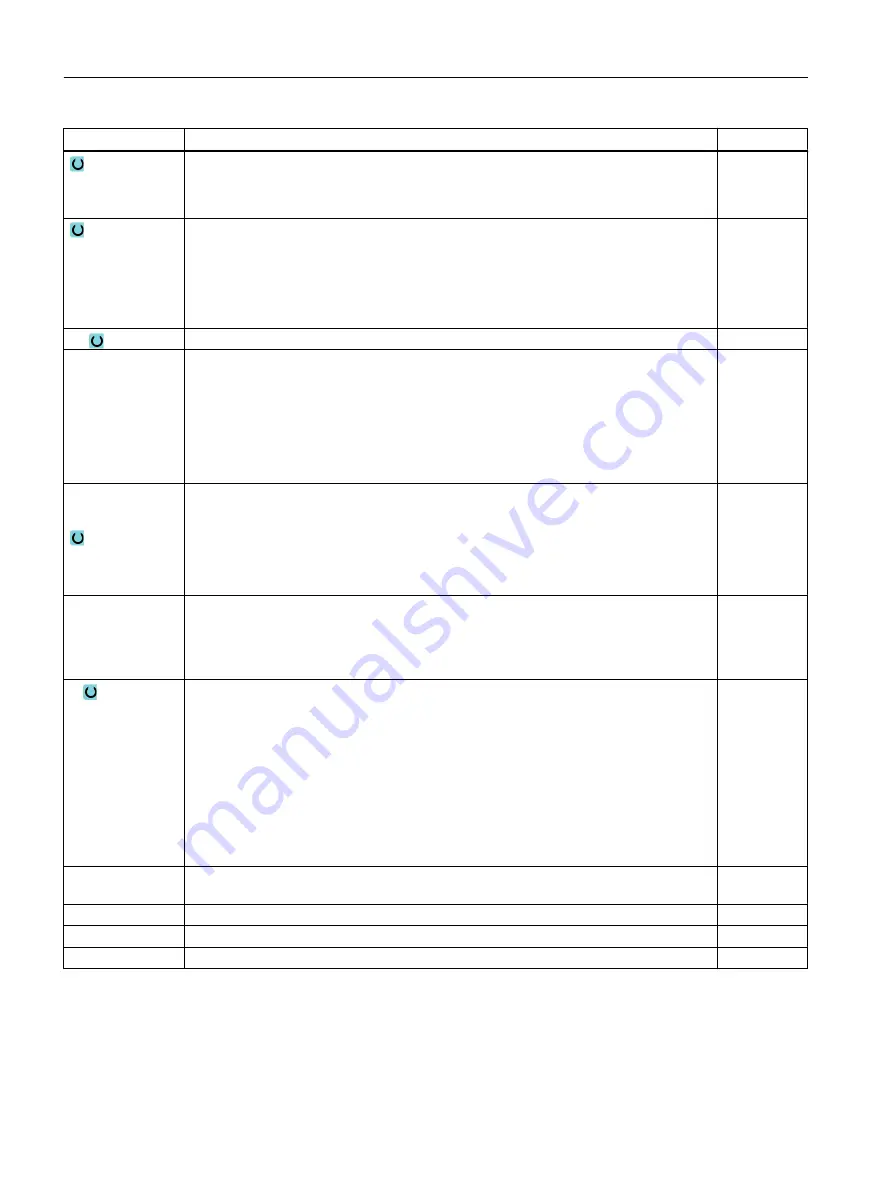
Parameter
Description
Unit
(only for G code)
Machining position:
● Single position
● Position pattern (MCALL)
X0
Y0
Z0
(only for G code)
The positions refer to the center point:
Reference point X – (for single position only)
Reference point Y – (for single position only)
Reference point Z
mm
mm
mm
Z1
End point of the thread (abs) or thread length (inc)
mm
Table
Thread table selection:
● Without
● ISO metric
● Whitworth BSW
● Whitworth BSP
● UNC
Selection – (not
for table "without")
Selection of table value: e.g.
● M3; M10; etc. (ISO metric)
● W3/4"; etc. (Whitworth BSW)
● G3/4"; etc. (Whitworth BSP)
● N1" - 8 UNC; etc. (UNC)
P
Display of the thread pitch for the parameter input in the input field "Table" and "Selection". MODULUS
Turns/"
mm/rev
inch/rev
P
- (selection
option only for ta‐
ble selection "with‐
out")
Pitch ...
● in MODULUS: For instance, used for worms that mesh with a gearwheel.
● per inch: Used with pipe threads, for example.
When entered per inch, enter the integer number in front of the decimal point in the
first parameter field and the figures after the decimal point as a fraction in the second
and third field.
● in mm/rev
● in inch/rev
The tool used depends on the thread pitch.
MODUL
Turns/"
mm/rev
in/rev
∅
Nominal diameter
Example: Nominal diameter of M12 = 12 mm
mm
H1
Thread depth
mm
αS
Starting angle
Degrees
rev
Finishing allowance in X and Y - (only for ∇)
mm
* Unit of feedrate as programmed before the cycle call
Programming technological functions (cycles)
10.2 Milling
Milling
474
Operating Manual, 08/2018, 6FC5398-7CP41-0BA0