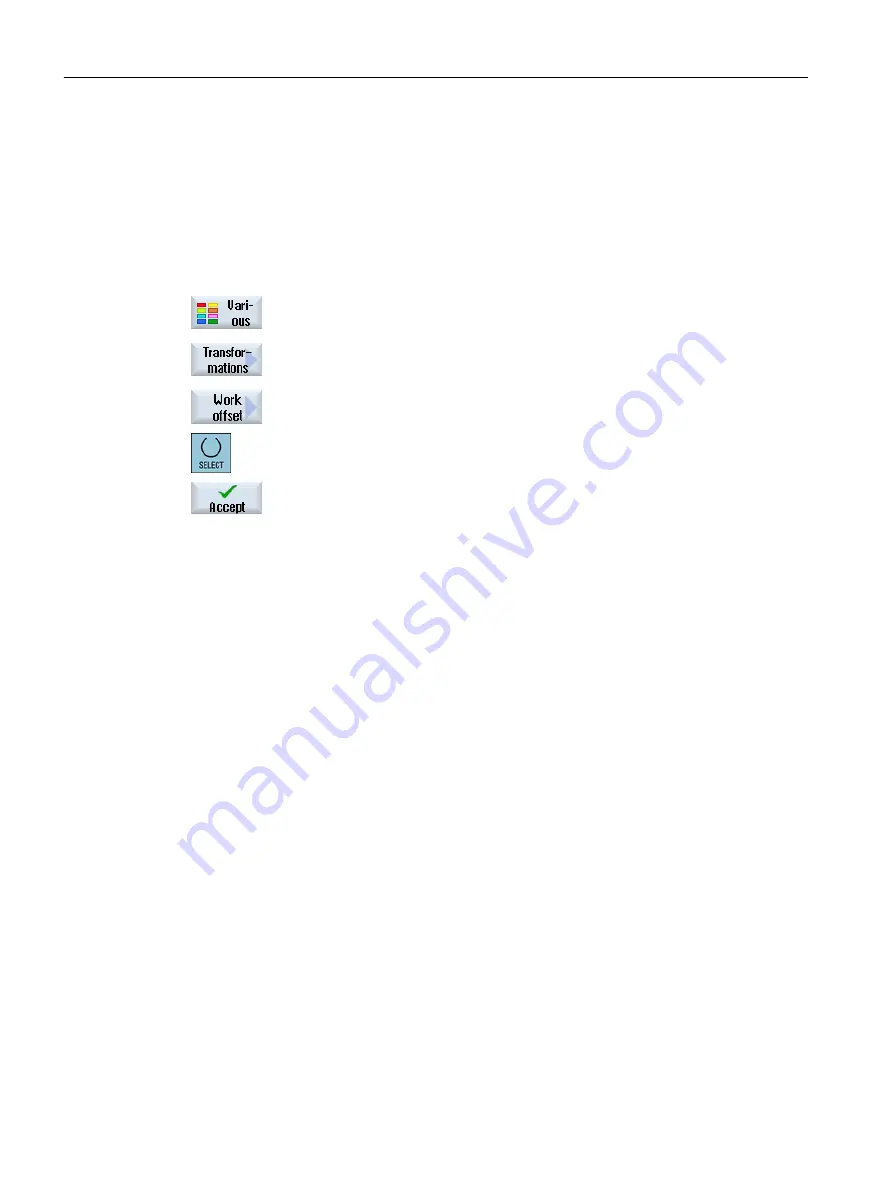
9.10
Call work offsets
You can call work offsets (G54, etc.) from any program.
You define work offsets in work offset lists. You can also view the coordinates of the selected
offset here.
Procedure
1.
Press the "Various", "Transformations" and "Work offset" softkeys.
The "Work offset" window opens.
2.
Select the desired work offset (e.g. G54).
3.
Press the "Accept" softkey.
The work offset is transferred into the work plan.
Creating a ShopMill program
9.10 Call work offsets
Milling
338
Operating Manual, 08/2018, 6FC5398-7CP41-0BA0