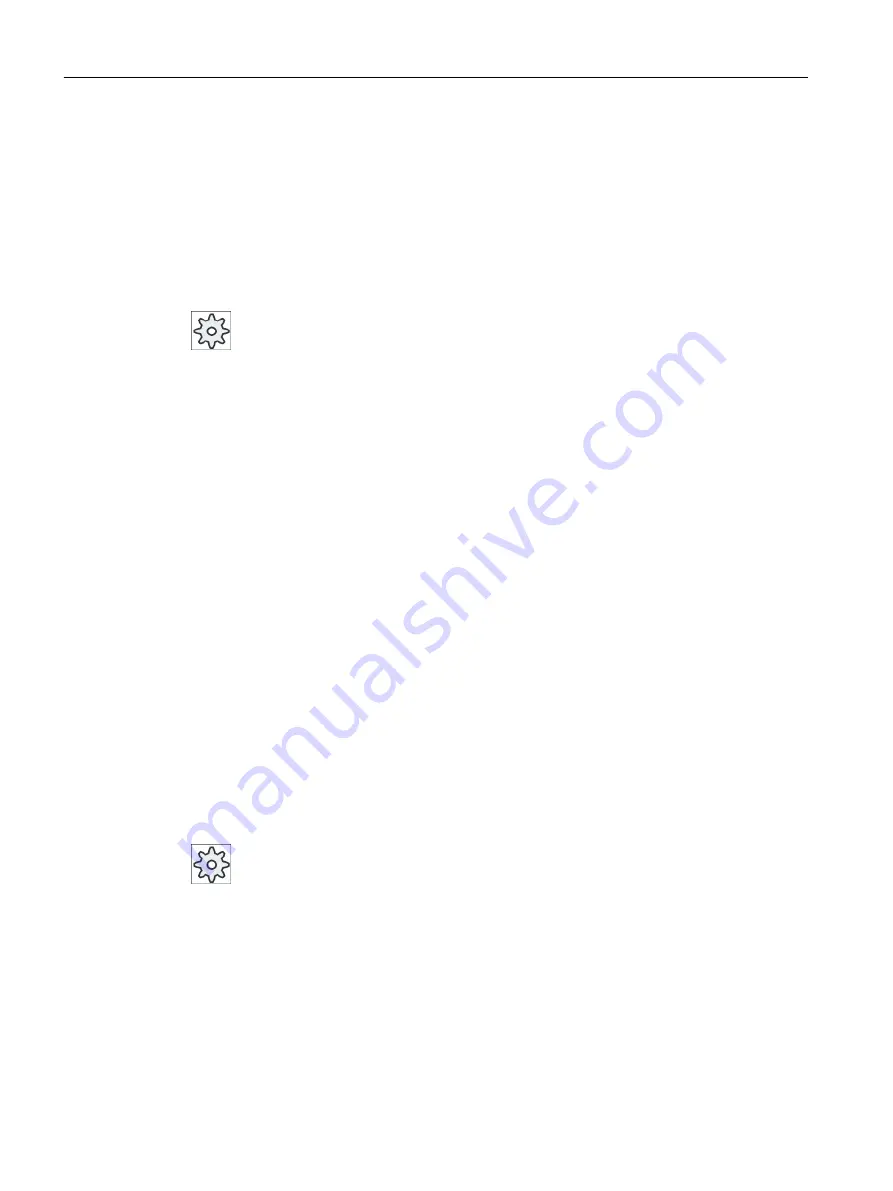
Tool
To avoid collisions, use 5-axis transformation (software option) to define the position of the
tool tip during swiveling.
● Correct
The position of the tool tip is corrected during swiveling (tracking function).
● No correction
The position of the tool tip is not corrected (not tracked) during swiveling.
Machine manufacturer
Please observe the information provided by the machine manufacturer.
Swivel plane (only for G code programming)
● New
Previously active swivel frames and programmed frames are deleted. A new swivel frame
is formed according to the values specified in the input screen.
Every main program must begin with a swivel cycle with the new swivel plane, in order to
ensure that a swivel frame from another program is not active.
● Additive
The swivel frame is added to the swivel frame from the last swivel cycle.
If several swivel cycles are programmed in a program and programmable frames are also
active between them (e.g., AROT ATRANS), these are taken into account in the swivel
frame. If a swivel data set is activated that was not previously active, the swivel frames are
not deleted.
If the currently active work offset contains rotations, e.g., due to previous workpiece measuring
operations, they will be taken into account in the swivel cycle.
Swivel mode
Swiveling can either be realized axis-by-axis, using the angle in space, using the projection
angle or directly. The machine manufacturer determines when setting up the "Swivel plane/
swivel tool" function which swivel methods are available.
Machine manufacturer
Please refer to the machine manufacturer's specifications.
Programming technological functions (cycles)
10.6 Further cycles and functions
Milling
634
Operating Manual, 08/2018, 6FC5398-7CP41-0BA0