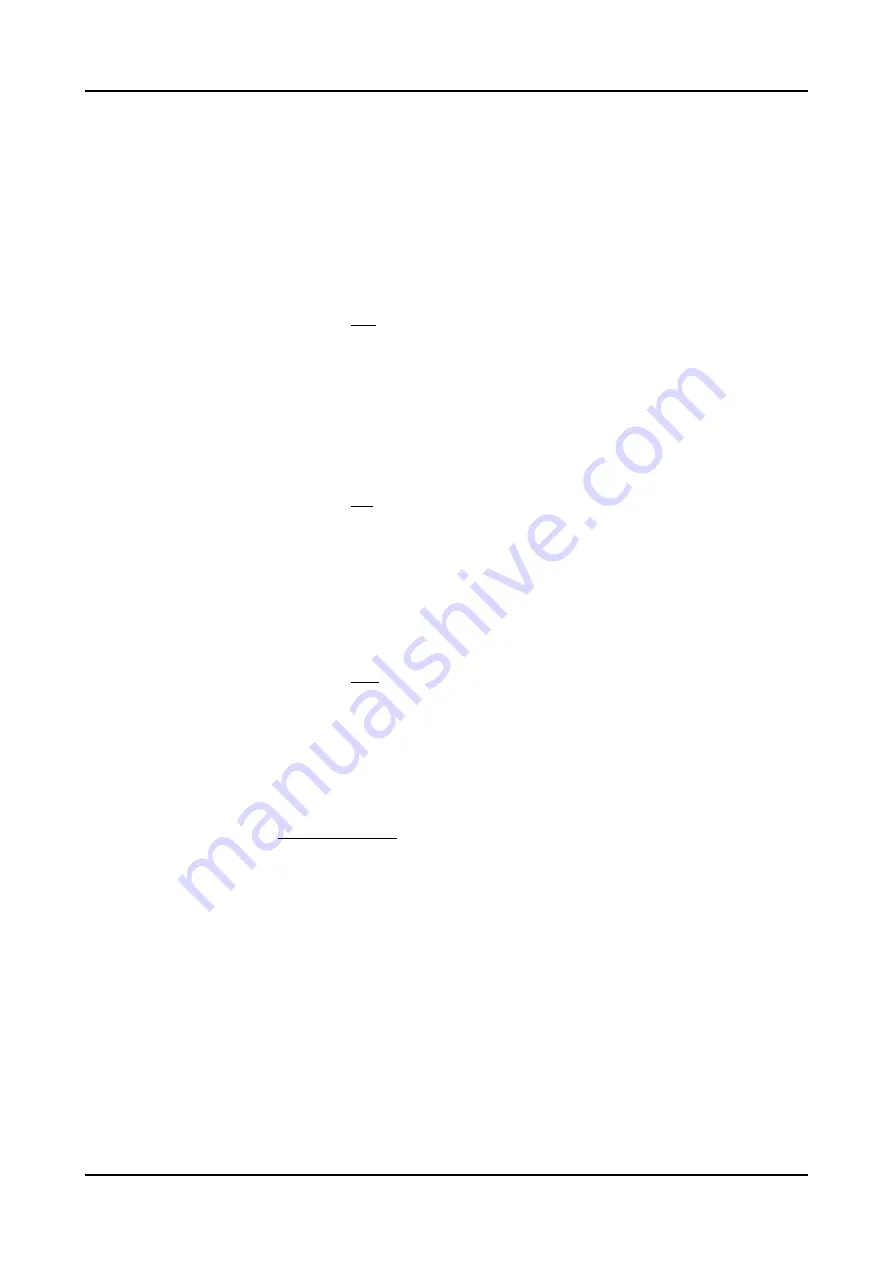
can be more severe than the heating effects and therefore a separate unbalance
protection is used.
Unbalances in other connected loads in the same busbar can also affect the motor.
A voltage unbalance typically produces 5 to 7 times higher current unbalance.
Because the thermal overload protection is based on the highest TRMS value of
the phase current, the additional heating in stator winding is automatically taken
into account. For more accurate thermal modeling, the
Negative Seq factor setting
is used for taking account of the rotor heating effect.
Negative Seq factor
R
R
R
R
=
2
1
(Equation 21)
R
R2
Rotor negative sequence resistance
R
R1
Rotor positive sequence resistance
A conservative estimate for the setting can be calculated:
Negative Seq factor
I
LR
=
175
2
(Equation 22)
I
LR
Locked rotor current (multiple of set
Rated current
). The same as the start-up
current at the beginning of the motor start-up.
For example, if the rated current of a motor is 230 A, start-up current is 5.7 x I
r
,
Negative Seq factor
=
=
175
5 7
5 4
2
.
.
(Equation 23)
Setting the thermal restart level
The restart disable level can be calculated as follows:
θ
i
startup time of the motor
operate time when no prior load
=
−
×
100
10
%
0
0%
+
margin
(Equation 24)
For example, the motor start-up time is 11 seconds, start-up current 6 x rated and
Time constant start is set for 800 seconds. Using the trip curve with no prior load,
the operation time at 6 x rated current is 25 seconds, one motor start-up uses 11/25
≈ 45 percent of the thermal capacity of the motor. Therefore, the restart disable
level must be set to below 100 percent - 45 percent = 55 percent, for example to 50
percent (100 percent - (45 p margin), where margin is 5 percent).
Setting the thermal alarm level
Tripping due to high overload is avoided by reducing the load of the motor on a
prior alarm.
Protection functions
1MRS757644 H
372
620 series
Technical Manual