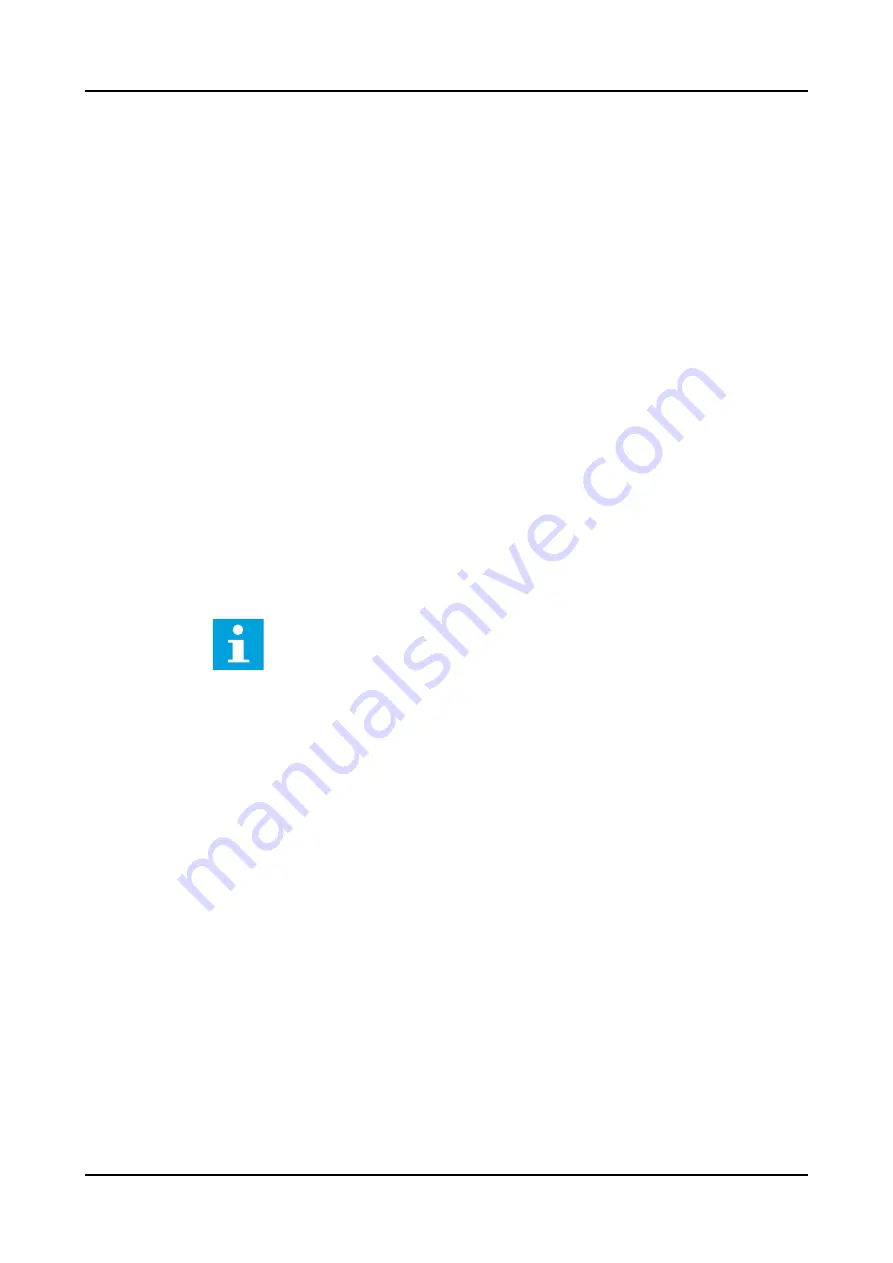
Operation time counter
This module counts the operation time. When
POS_ACTIVE
is active, the count is
continuously added to the time duration until it is deactivated. At any time the
OPR_TIME
output is the total duration for which
POS_ACTIVE
is active. The unit
of time duration count for
OPR_TIME
is hour. The value is available through the
Monitored data view.
The
OPR_TIME
output is a continuously increasing value and it is stored in a non-
volatile memory. When
POS_ACTIVE
is active, the
OPR_TIME
count starts increasing
from the previous value. The count of
OPR_TIME
saturates at the final value of
299999, that is, no further increment is possible. The activation of
RESET
can reset
the count to the
Initial value setting.
Limit Supervision
This module compares the motor run-time count to the set values of
Warning value
and
Alarm value to generate the
WARNING
and
ALARM
outputs respectively when the
counts exceed the levels.
The activation of the
WARNING
and
ALARM
outputs depends on the
Operating time
mode setting. Both
WARNING
and
ALARM
occur immediately after the conditions are
met if
Operating time mode is set to “Immediate”. If Operating time mode is set to
“Timed Warn”,
WARNING
is activated within the next 24 hours at the time of the day
set using the
Operating time hour setting. If Operating time mode is set to “Timed
Warn Alm”, the
WARNING
and
ALARM
outputs are activated at the time of day set
using
Operating time hour.
The
Operating time hour setting is used to set the hour of day in
Coordinated Universal Time (UTC). The setting has to be adjusted
according to the local time and local daylight-saving time.
The function contains a blocking functionality. Activation of the
BLOCK
input blocks
both
WARNING
and
ALARM
.
6.6.5
Application
The machine operating time since commissioning indicates the use of the machine.
For example, the mechanical wear and lubrication requirement for the shaft bearing
of the motors depend on the use hours.
If some motor is used for long duration runs, it might require frequent servicing,
while for a motor that is not used regularly the maintenance and service are
scheduled less frequently. The accumulated operating time of a motor together
with the appropriate settings for warning can be utilized to trigger the condition
based maintenance of the motor.
The operating time counter combined with the subsequent reset of the operating-
time count can be used to monitor the motor's run time for a single run.
Both the long term accumulated operating time and the short term single run
duration provide valuable information about the condition of the machine and
device. The information can be co-related to other process data to provide
diagnoses for the process where the machine or device is applied.
Supervision functions
1MRS757644 H
906
620 series
Technical Manual