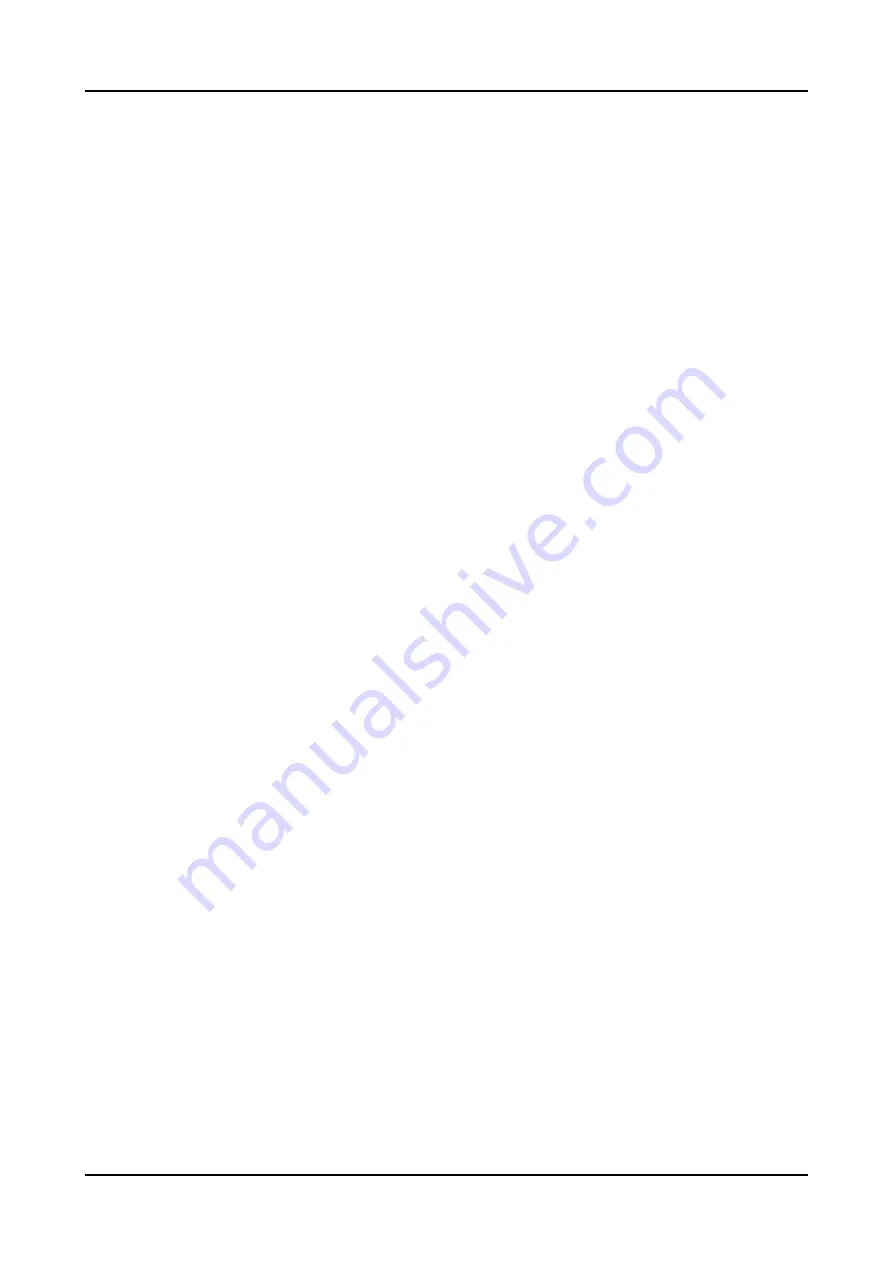
line voltage or single phasing. The protection of insulation failure by the
implementation of current sensing cannot detect some of these conditions, such
as restricted ventilation. Similarly, the protection by sensing temperature alone
can be inadequate in cases like frequent starting or jogging. The thermal overload
protection addresses these deficiencies to a larger extent by deploying a motor
thermal model based on load current.
The thermal load is calculated using the true RMS phase value and negative
sequence value of the current. The heating up of the motor is determined by the
square value of the load current. However, while calculating the thermal level, the
rated current should be re-rated or de-rated depending on the value of the ambient
temperature. Apart from current, the rate at which motor heats up or cools is
governed by the time constant of the motor.
Setting the weighting factor
There are two thermal curves: one which characterizes the short-time loads and
long-time overloads and which is also used for tripping and another which is used
for monitoring the thermal condition of the motor. The value of the
Weighting
factor p setting determines the ratio of the thermal increase of the two curves.
When the
Weighting factor p setting is 100 percent, a pure single time constant
thermal unit is produced which is used for application with the cables. As presented
, the hot curve with the value of
Weighting factor p being 100 percent
only allows an operate time which is about 10 percent of that with no prior load.
For example, when the set time constant is 640 seconds, the operate time with the
prior load 1 x FLC (full Load Current) and overload factor 1.05 is only 2 seconds, even
if the motor could withstand at least 5 to 6 seconds. To allow the use of the full
capacity of the motor, a lower value of
Weighting factor p should be used.
Normally, an approximate value of half of the thermal capacity is used when the
motor is running at full load. Thus by setting
Weighting factor p to 50 percent, the
protection relay notifies a 45 to 50 percent thermal capacity use at full load.
For direct-on-line started motors with hot spot tendencies, the value of
Weighting
factor p is typically set to 50 percent, which will properly distinguish between short-
time thermal stress and long-time thermal history. After a short period of thermal
stress, for example a motor start-up, the thermal level starts to decrease quite
sharply, simulating the leveling out of the hot spots. Consequently, the probability
of successive allowed start-ups increases.
When protecting the objects without hot spot tendencies, for example motors
started with soft starters, and cables, the value of
Weighting factor p is set to 100
percent. With the value of
Weighting factor p set to 100 percent, the thermal level
decreases slowly after a heavy load condition. This makes the protection suitable
for applications where no hot spots are expected. Only in special cases where the
thermal overload protection is required to follow the characteristics of the object to
be protected more closely and the thermal capacity of the object is very well known,
a value between 50 and 100 percent is required.
For motor applications where, for example, two hot starts are allowed instead of
three cold starts, the value of the setting
Weighting factor p being 40 percent has
proven to be useful. Setting the value of
Weighting factor p significantly below
50 percent should be handled carefully as there is a possibility to overload the
protected object as a thermal unit might allow too many hot starts or the thermal
history of the motor has not been taken into account sufficiently.
Protection functions
1MRS757644 H
370
620 series
Technical Manual