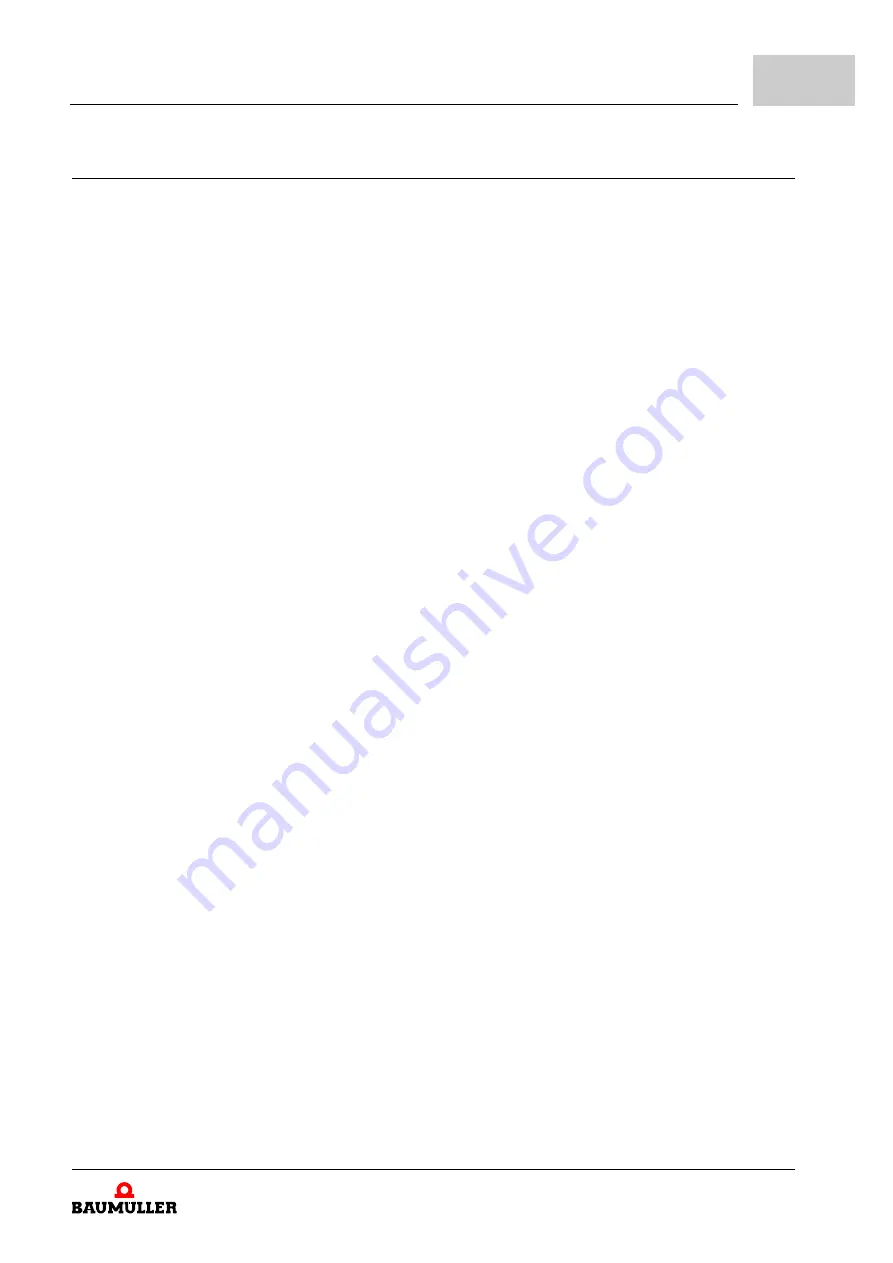
Description of the Software Modules and Parameters
Parameter manual
b maXX
BM5800
Document No.: 5.16029.03
607
3
3.8.7
Operating mode synchronous operation
The software module synchronous operation moves a slave axis in a synchronous angle
to a master axis. The set value for the slave axis may come from one of the two encoder
inputs (actual master axis). In addition, there is an option to count a virtual master axis in
the drive itself. In this case, speed set values will be specified.
The set value of the master axis serves as the input value for the electronic transmission.
The output value of the transmission is the position set value for the position control.
The following synchronous operation modes (
Mode; bit 0 to 3) are differentiated:
m
Bit 0-3 = 0000: Actual master axis in relative synchronized angles
The set value for the slave axis is specified in this mode directly through an encoder
input. The axis is located in the position control.
The set value for the slave axis can be calculated alternatively from the set value of the
master axis only at double axis units. Details see Other functions on
.
When enabling the drive in the operating mode synchronous operation or switching to
this operating mode during active operation, the angle will be permanently positioned
between master and slave axis. This means that the master axis and slave axis will
have an angle relation to each other from this point on that is permanent but not de-
fined. The existing angle relation will be lost in the event of a control block, change to
another operating mode, change of transmission factor or a Stop command to the
slave axis.
When the speed synchronization is ON (Mode bit 8 = 1), the angle relation will not be
specified until the synchronization has been established.
The set value of the master axis can be smoothed with the
w2-Feedforward
time constant. The differentiated required position (target speed) which yields the value
for the speed feedforward will be smoothed only. The required position for the position
controller remains unaffected thereof.
The acceleration feedforward (w3 acceleration feedfwd. act. value
) is calcu-
lated from the smoothed speed set value (
) without the
w2-Feedforward factor as in the other position controlled operating modes. The accel-
eration feedforward can be switched off with
and
if required. See
block diagram of the position / speed controller when in position control in
m
Bit 0-3 = 0010: Virtual master axis in relative synchronized angle
The set value for the slave axis is specified in this mode through Parameter
Virtual master speed set value. The axis is located in the position control.
A position set value for the virtual master axis is calculated in the drive from the speed
set value. The drive follows this virtual master axis synchronized.
This mechanism is purposeful when other axis are connected as slave axis. These
slave axes then receive the set value of the virtual master axis as input set value. Sub-
sequently, all other axes then follow the same set value including the axis that calcu-
lates the virtual master axis itself.
The input set value of the virtual master axis can be routed through a ramp generator
(ramp function generator) or have a direct effect. Refer to the related explanations of
bit 12 of the mode.
Содержание b maXX BM5800
Страница 10: ...Parameter manual b maXX BM5800 Document No 5 16029 03 Baumüller Nürnberg GmbH 10 of 814 Contents ...
Страница 724: ...Monitoring Parameter manual b maXX BM5800 Document No 5 16029 03 Baumüller Nürnberg GmbH 724 of 814 3 11 ...
Страница 756: ...Error descriptions Parameter manual b maXX BM5800 Document No 5 16029 03 Baumüller Nürnberg GmbH 756 of 814 4 5 ...
Страница 800: ...Parameter manual b maXX BM5800 Document No 5 16029 03 Baumüller Nürnberg GmbH 800 of 814 ...
Страница 808: ...Parameter manual b maXX BM5800 Document No 5 16029 03 Baumüller Nürnberg GmbH 808 of 814 ...
Страница 814: ...Parameter manual b maXX BM5800 Document No 5 16029 03 Baumüller Nürnberg GmbH 814 of 814 Notes ...
Страница 815: ......