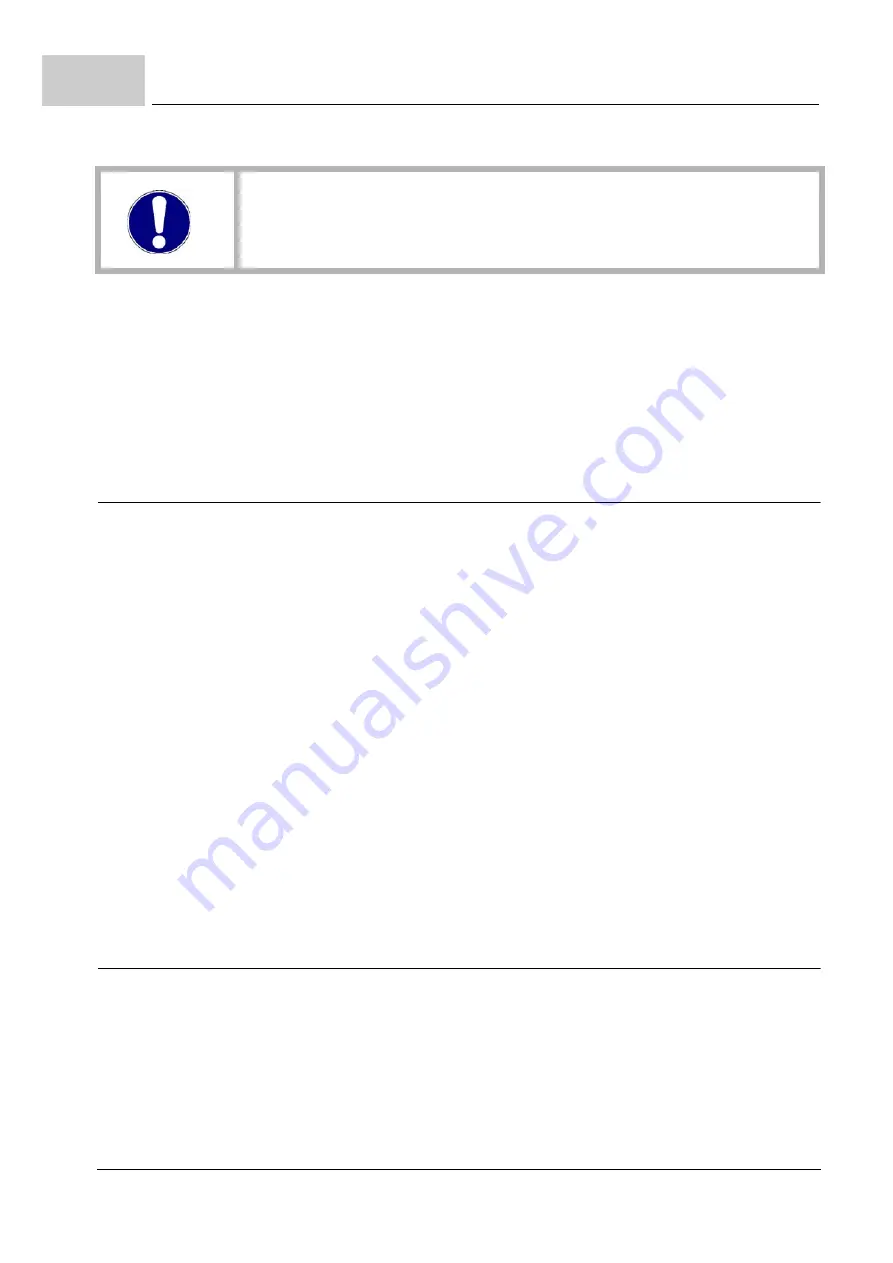
Motor Operating Mode
Parameter manual
b maXX
BM5800
Document No.: 5.16029.03
Baumüller Nürnberg GmbH
662
3.9
On principle the dead time compensation should be used at the sensorless control, so
that the non-linearity of the power unit can be compensated, in order to improve the ex-
actness of the voltage model. However the dead time compensation can affect the injec-
tion procedure. This must be tested in each case.
The torque display requires an exact dead time compensation at low speeds in the con-
trolled operation. In order to improve the accuracy of the torque, a fine adjustment of the
dead time compensation can be carried out at speed 0 via bit 9 of parameter
3.9.1.1 General constraints of sensorless control with the injection procedure
The injection procedure for the sensorless control of the SM can only be operated, if
m
the energy transducer possesses an iron-core magnetic with pronounced saturation ef-
fects (it cannot be used on rotating and linearly ironless machines) and
m
the magnetic symmetry of the three phases is existent
Because of the constraints, which are listed above, the operation of sensorless control of
the SM, as well as the use of method 2 of notch position search is only then possible, if
the machines have been tested successfully.
Constraints of the sensorless control at very low speed
The operation is also possible at very low speed and at standstill. Because of the higher
torque ripple, however, the motor may run irregularly.
Switch on / Enable at rotating machine
At first there is no speed or position information available, when enabling the drive in the
sensorless operation. At each switching on of the drive the initial rotor position is deter-
mined on the basis of the HF-injection. Additionally there is the option to synchronize to
the moving motor.
3.9.1.2 Commissioning at the sensorless operation of the synchronous machine
1
Selection of the motor from the motor database of ProDrive or the setting of the data
with the help of the motor type plate. The following values are necessary: nominal cur-
rent, nominal speed, pole pair number, EMF-constant. The DC link nominal value also
must be conforming to the actual DC link value.
2
Execute measurement of stator resistance and Lq-inductance of the motor as well as
the dead time of the power unit with the help of the function self-optimization.
3
Calculate the current controller parameters with the measured values for stator resis-
tance and the Lq-inductance.
CAUTION!
If there is a faulty parameterization, it cannot be guaranteed, that the motor reaches
the desired speed!
Содержание b maXX BM5800
Страница 10: ...Parameter manual b maXX BM5800 Document No 5 16029 03 Baumüller Nürnberg GmbH 10 of 814 Contents ...
Страница 724: ...Monitoring Parameter manual b maXX BM5800 Document No 5 16029 03 Baumüller Nürnberg GmbH 724 of 814 3 11 ...
Страница 756: ...Error descriptions Parameter manual b maXX BM5800 Document No 5 16029 03 Baumüller Nürnberg GmbH 756 of 814 4 5 ...
Страница 800: ...Parameter manual b maXX BM5800 Document No 5 16029 03 Baumüller Nürnberg GmbH 800 of 814 ...
Страница 808: ...Parameter manual b maXX BM5800 Document No 5 16029 03 Baumüller Nürnberg GmbH 808 of 814 ...
Страница 814: ...Parameter manual b maXX BM5800 Document No 5 16029 03 Baumüller Nürnberg GmbH 814 of 814 Notes ...
Страница 815: ......