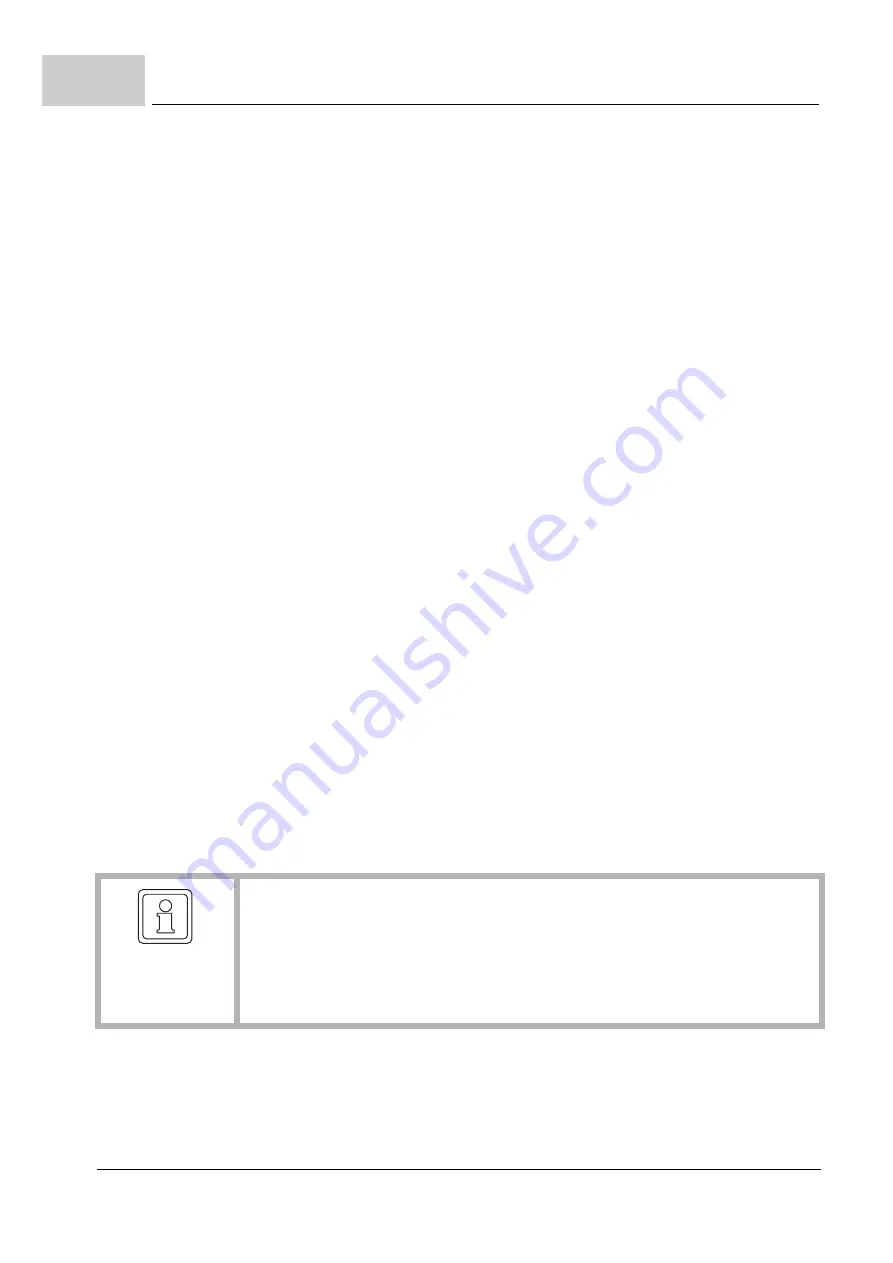
Management
Parameter manual
b maXX
BM5800
Document No.: 5.16029.03
Baumüller Nürnberg GmbH
332
3.5
The following recommendation applies for setting the delay to the start of the movement,
T
B
):
1
If the state monitoring is switched off (
Bit 1 = 0):
T
B
> T
1)
SignalCom
+ T
2)
mech
2
If the state monitoring is switched on (
Bit 1 = 1) and the response signal is
reporting the state of the current through the brake:
T
B
> T
mech
– T
3)
SignalFB
3
If the state monitoring is switched on (
Bit 1 = 1) and the response signal is
reporting the mechanical state of the brake:
T
B
= 0
1)
Processing time for the command in the controller, max. 2 ms
2)
Operating time of holding brakes depends on type, approx. 75-350 ms
3)
Duration of current buildup in brake coil (depends on type, approx. 30 ms) + processing time for response in
controller: max. approx. 32 ms.
The following must apply for a correct error reaction:
timeout check-back signal > T
SignalCom
+ T
SignalFB
Applying the
brake
When applying the brake, account is taken of whether the drive is still under torque or
whether the pulses are inhibited.
Pulses are enabled (drive is under torque)
If the drive is being actively braked (response to QUICK STOP/SHUT-DOWN/INHIB-
IT/drive error) and if the torque is to be reduced after the end of the braking procedure
(pulse inhibit), the brake is applied when a presettable speed threshold is reached. The
subsequent pulse inhibit can also be delayed if this is required to compensate for a me-
chanical dead time.
If the activated state monitoring detects that the brake could not be applied, the drive re-
mains under torque in the "Quick Stop active/drive shut-down active/inhibit operation ac-
tive" state in order to prevent sagging of a suspended axis. Error messages 1102/1103
indicate this state. The user can still move the drive into a torque-free position and then
shut off the drive torque (pulse inhibit or inhibit voltage). The conditions and events re-
quired for the transition to the "Enabled" state can be found in the description of the state
transitions in the device control system (
ff).
In the "Error response active" state, this check is not carried out, i.e. even with the state
monitoring activated and the brake not applied, the transition to the "Error" state takes
place. The drive will consequently be without torque.
NOTE!
The following must be observed to prevent a suspended axis from sagging after an
active braking procedure at the end of which the brake could not be applied:
The responses to Errors 1102/1103 must be set to "No response" and Errors
1102/1103 may only be reset after the enable is repeated, otherwise the drive will be
without torque before it can be enabled.
Содержание b maXX BM5800
Страница 10: ...Parameter manual b maXX BM5800 Document No 5 16029 03 Baumüller Nürnberg GmbH 10 of 814 Contents ...
Страница 724: ...Monitoring Parameter manual b maXX BM5800 Document No 5 16029 03 Baumüller Nürnberg GmbH 724 of 814 3 11 ...
Страница 756: ...Error descriptions Parameter manual b maXX BM5800 Document No 5 16029 03 Baumüller Nürnberg GmbH 756 of 814 4 5 ...
Страница 800: ...Parameter manual b maXX BM5800 Document No 5 16029 03 Baumüller Nürnberg GmbH 800 of 814 ...
Страница 808: ...Parameter manual b maXX BM5800 Document No 5 16029 03 Baumüller Nürnberg GmbH 808 of 814 ...
Страница 814: ...Parameter manual b maXX BM5800 Document No 5 16029 03 Baumüller Nürnberg GmbH 814 of 814 Notes ...
Страница 815: ......