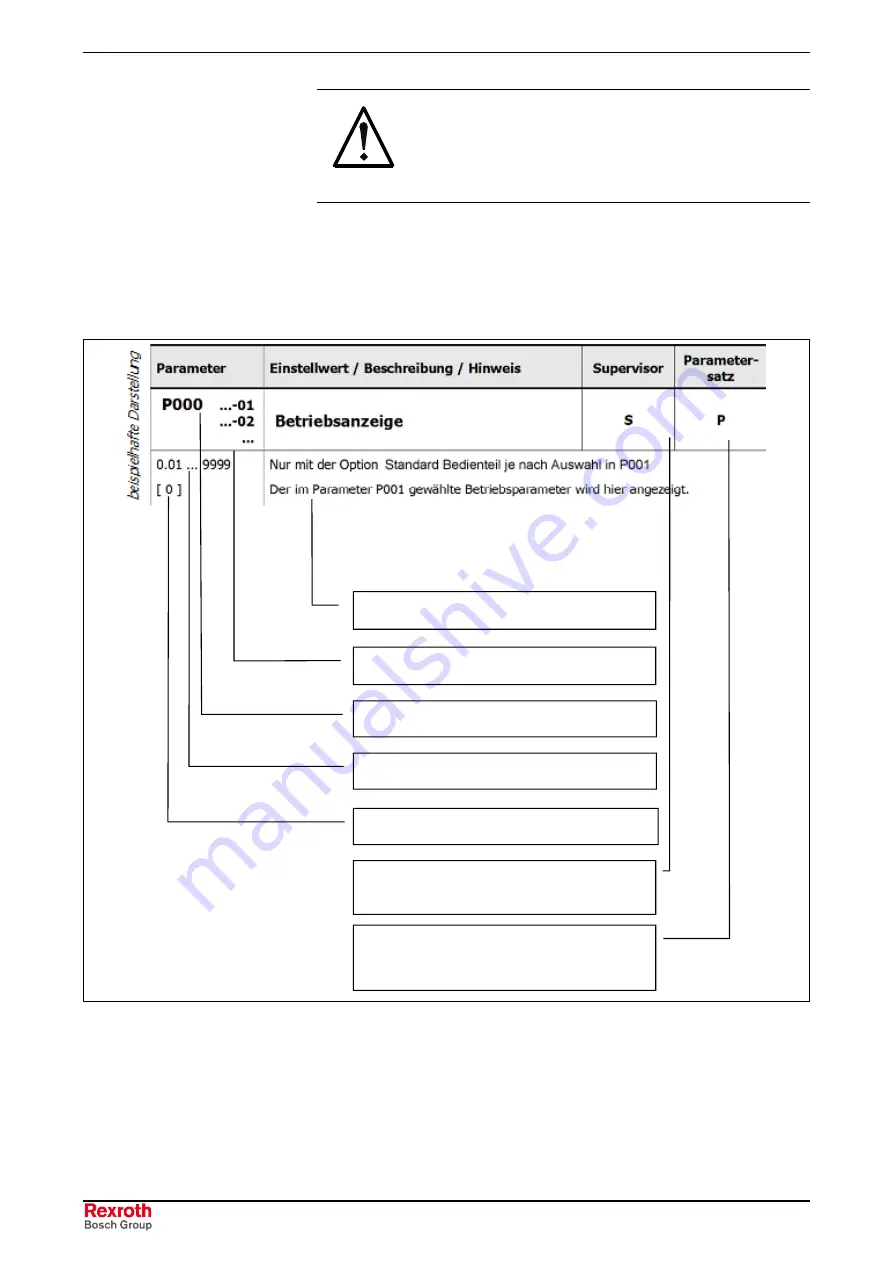
11-2
Parameterization
Rexroth IndraDrive FCS01.1
DOK-INDRV*--FCS01*****-IB01_EN-P
CAUTION
⇒
All current parameter setting will be lost if P523 = 1 is
set and confirmed with "ENTER". To save current
settings, they can be transferred to the memory of
the control panels.
Availability of Parameters
Depending on the respective configurations, the parameters are subject
to certain conditions. In the following table pages (from Chapter 11.1
Status Indication), all parameters are listed with the respective
information.
Supervisor parameter depend upon the
setting in P003
Parameter number
Parameter text
Parameter record dependent parameter
selection in P100
Array values
Value range of the parameter
Factory setting of the parameter
Fig. 11-2:
Availability of parameters
Summary of Contents for IndraDrive Fc FCS01
Page 28: ...5 2 Delivery Rexroth IndraDrive FCS01 1 DOK INDRV FCS01 IB01_EN P ...
Page 34: ...6 6 Certifications and Types Rexroth IndraDrive FCS01 1 DOK INDRV FCS01 IB01_EN P ...
Page 56: ...8 20 Installation Rexroth IndraDrive FCS01 1 DOK INDRV FCS01 IB01_EN P ...
Page 88: ...10 4 Commissioning Rexroth IndraDrive FCS01 1 DOK INDRV FCS01 IB01_EN P ...
Page 237: ......