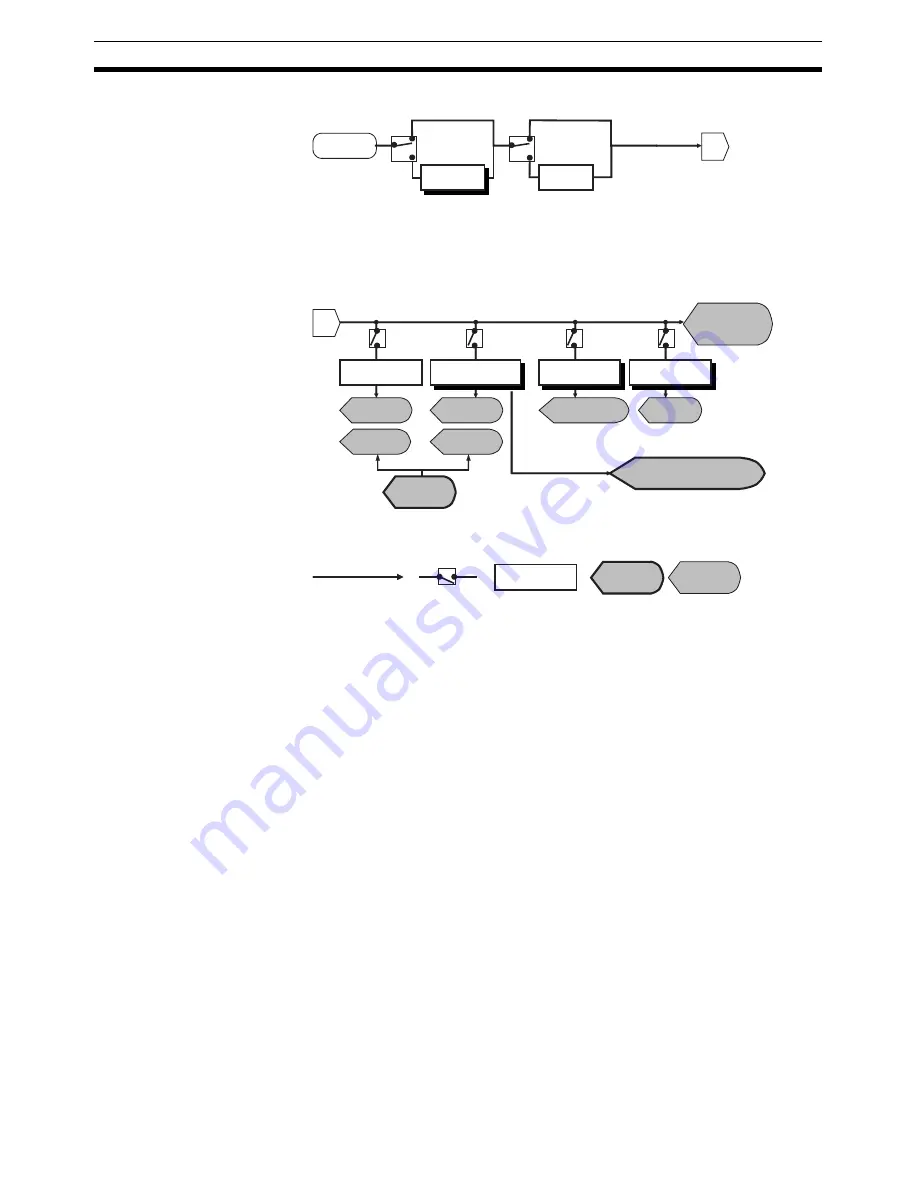
288
Overview of Analog I/O Slave Units
Section 6-1
Analog processing is performed according to the following flowchart.
6-1-4
Selecting Data for Analog Input Slave Units
After performing math operations, select one out of the six resulting values to
allocate in the Master Unit, from the analog input value, peak value, bottom
value, top value, valley value, and rate of change. The selected data is
referred to as “analog data” and can be allocated in the Master Unit individu-
ally or in combination with Status Flags. The data is selected using the CX-
Integrator. For Analog Data, comparator operations with four alarm set values
can be performed (comparator function).
Input
Moving
average
Scaling
A
A
Analog input
value 1
Peak/Bottom
Top/Valley
Rate of change
Cumulated
value
Peak
value 2
Top
value 4
Rate of change
value 6
Cumulated
value
Hold Flag
Top/Valley detection timing
(allocated I/O data)
Data Flow
Selection
Conversion
processing
Allocated
I/O data
Processing
results
Bottom
value 3
Valley
value 5
Summary of Contents for CRT1 - 10-2008
Page 2: ...CRT1 Series CompoNet Slave Units and Repeater Unit Operation Manual Revised October 2008...
Page 3: ...iv...
Page 5: ...vi...
Page 9: ...x...
Page 15: ...xvi...
Page 23: ...xxiv Conformance to EC Directives 6...
Page 51: ...28 Slave Unit Models Section 1 2...
Page 123: ...100 Connecting External I O for Slave Units Section 3 6...
Page 365: ...342 Temperature Input Units Section 7 5...
Page 381: ...358 Expansion Unit Specifications Section 8 2...
Page 418: ...395 Repeater Unit Section 10 2 Dimensions 42 3 50 3 1 27 5 95 mm...
Page 419: ...396 Repeater Unit Section 10 2...
Page 424: ...401 CX Integrator Section 11 1...
Page 575: ...552 Current Consumption Summary Appendix D 552...
Page 581: ...558 Index...
Page 583: ...560 Revision History...