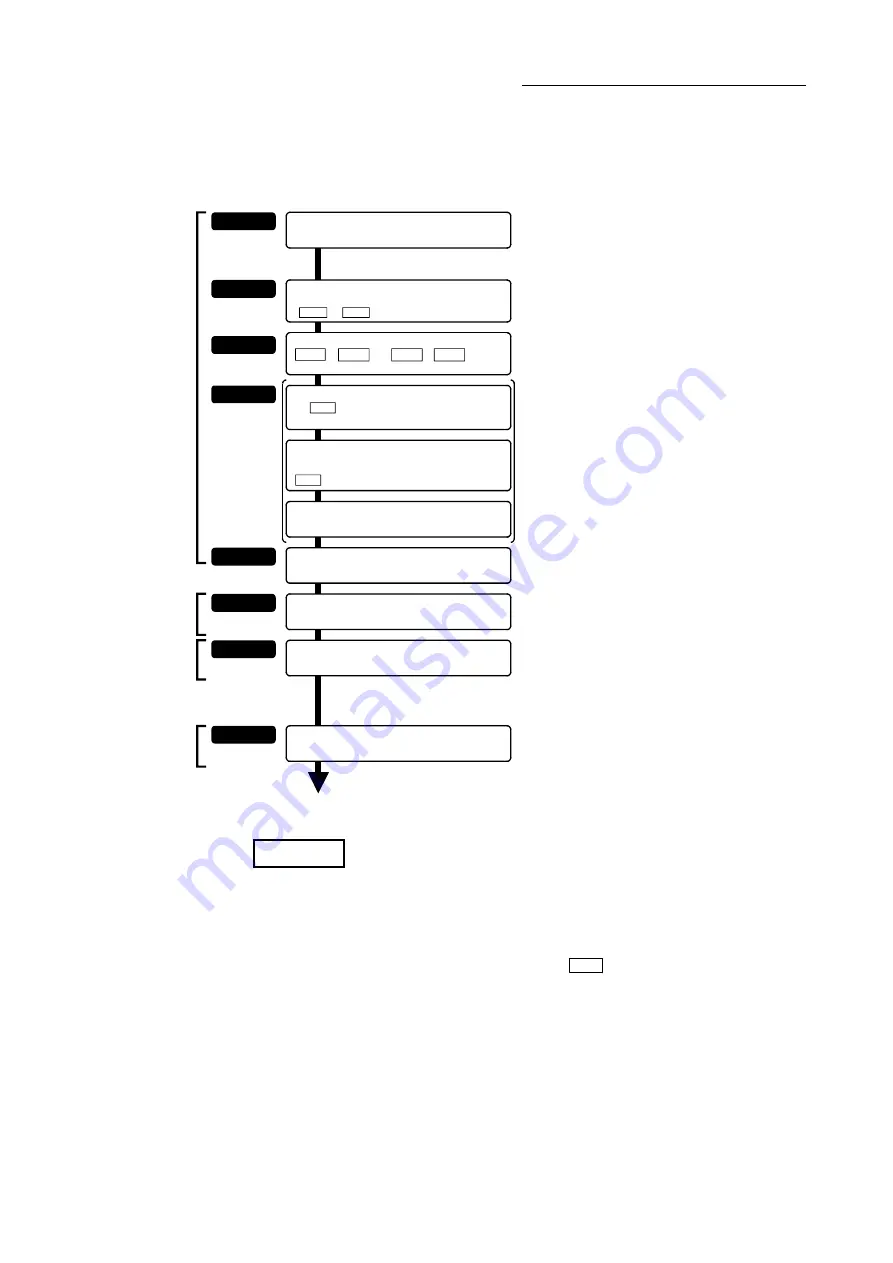
10 - 6
Chapter 10 High-Level Positioning Control
10.2 High-level positioning control execution procedure
High-level positioning control is carried out using the following procedure.
STEP 1
Preparation
Refer to Chapter 9
Carry out the "major positioning control" setting.
"High-level positioning control" executes each control
("major positioning control") set in the positioning data
with the designated conditions, so first carry out
preparations so that "major positioning control" can be
executed.
STEP 2
The "block start data" from 1 to 50 points can be set.
Set the "block start data" corresponding to each
control
(Note-1)
.
( Da. 11 to Da. 14 ) × required data amount
Refer to Section 10.3
STEP 3
STEP 4
Refer to Section 10.6
Refer to Section 10.4
Create a sequence program in which block No. is set in
the
"
Cd. 3 Positioning start No.
"
(Note-1)
(Control data setting)
Starting the control
Monitoring the control
Control termination
STEP 5
Refer to Chapter 6
STEP 6
STEP 7
Create a sequence program in which the "positioning
start signal" is turned ON by a positioning start command.
Write the sequence programs created in STEP4
to the PLC CPU.
Turn ON the "positioning start command" of
the axis to be started.
Stopping the control
STEP 8
Stop when control is completed
Monitor the high-level positioning control.
Refer to Section 6.5.3
Refer to Section 6.5.6
Create a sequence program in which the "block start
data point No. to be started" (1 to 50) is set in the
" Cd. 4 Positioning starting point No.
"
Set the "condition data" for designation with the
"block start data". Up to 10 condition data items
can be set.
The Simple Motion module recognizes that the control
is high-level positioning control using "block start data"
by the "7000" designation.
Use GX Works2 to create a sequence program
to execute the "high-level positioning control".
Write the sequence program created in STEP 4 to the
PLC CPU using GX Works2.
Same procedure as for the "major positioning control"
start.
Monitor using GX Works2
.
Same procedure as for the "major positioning control" stop.
Set the "condition data"
(Note-1)
.
( Da. 15 to Da. 19 and Da.23 to Da.26 ) ×
required data amount
REMARK
(Note-1): Five sets of "block start data (50 points)" and "condition data (10 items)"
corresponding to "block No. 7000 to 7004" are set with GX Works2 or
sequence program.
When those are set with GX Works2 and written to the Simple Motion
module, "7000 to 7004" can be set in "
Cd.3
Positioning start No.
" on STEP4
when the above is set.
Summary of Contents for MELSEC-L Series
Page 2: ......
Page 30: ...MEMO ...
Page 70: ...2 10 Chapter 2 System Configuration MEMO ...
Page 83: ...3 13 Chapter 3 Specifications and Functions MEMO ...
Page 103: ...3 33 Chapter 3 Specifications and Functions MEMO ...
Page 107: ...3 37 Chapter 3 Specifications and Functions MEMO ...
Page 111: ...3 41 Chapter 3 Specifications and Functions MEMO ...
Page 115: ...3 45 Chapter 3 Specifications and Functions MEMO ...
Page 140: ...4 22 Chapter 4 Installation Wiring and Maintenance of the Product MEMO ...
Page 253: ...5 113 Chapter 5 Data Used for Positioning Control MEMO ...
Page 342: ...5 202 Chapter 5 Data Used for Positioning Control MEMO ...
Page 438: ...7 20 Chapter 7 Memory Configuration and Data Process MEMO ...
Page 440: ...MEMO ...
Page 485: ...9 25 Chapter 9 Major Positioning Control MEMO ...
Page 594: ...9 134 Chapter 9 Major Positioning Control MEMO ...
Page 624: ...10 30 Chapter 10 High Level Positioning Control MEMO ...
Page 656: ...11 32 Chapter 11 Manual Control MEMO ...
Page 690: ...12 34 Chapter 12 Expansion Control MEMO ...
Page 798: ...13 108 Chapter 13 Control Sub Functions MEMO ...
Page 866: ...14 68 Chapter 14 Common Functions MEMO ...
Page 884: ...15 18 Chapter 15 Dedicated Instructions MEMO ...
Page 899: ...16 15 Chapter 16 Troubleshooting MEMO ...
Page 1036: ...Appendix 88 Appendices MEMO ...
Page 1039: ......