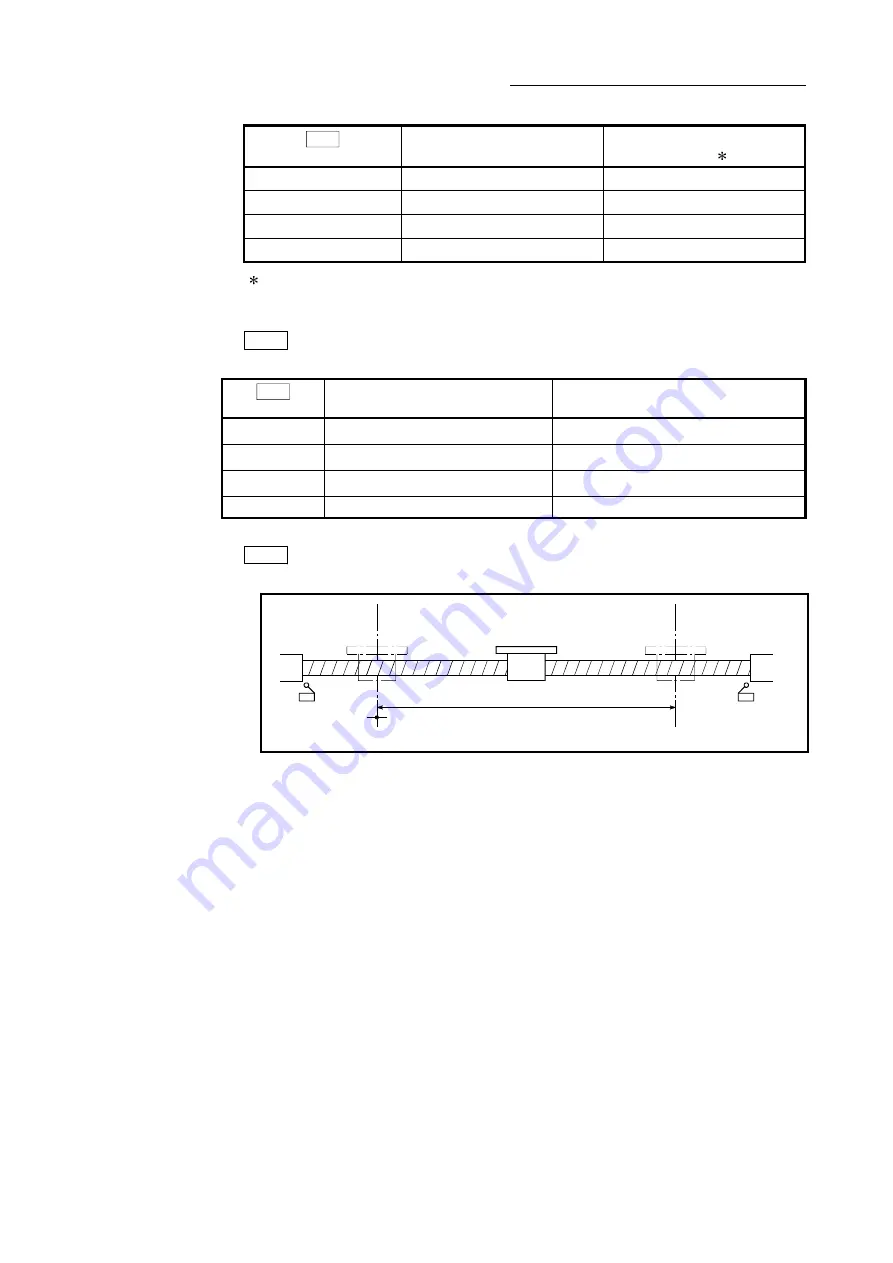
5 - 32
Chapter 5 Data Used for Positioning Control
Pr.1
setting value
Value set with GX Works2
(unit)
Value set with sequence program
(unit)
0 : mm
0 to 6553.5 (
m)
0 to 65535 (
10
-1
m)
1 : inch
0 to 0.65535 (inch)
0 to 65535 (
10
-5
inch)
2 : degree
0 to 0.65535 (degree)
0 to 65535 (
10
-5
degree)
3 : PLS
0 to 65535 (PLS)
0 to 65535 (PLS)
0 to 32767
: Set as a decimal
32768 to 65535 : Convert into hexadecimal and set
Pr.12
Software stroke limit upper limit value
Set the upper limit for the machine's movement range during positioning control.
Pr.1
setting value
Value set with GX Works2
(unit)
Value set with sequence program
(unit)
0 : mm
-214748364.8 to 214748364.7 (
m)
-2147483648 to 2147483647 (
10
-1
m)
1 : inch
-21474.83648 to 21474.83647(inch) -2147483648 to 2147483647 (
10
-5
inch)
2 : degree
0 to 359.99999 (degree)
0 to 35999999 (
10
-5
degree)
3 : PLS
-2147483648 to 2147483647(PLS)
-2147483648 to 2147483647 (PLS)
Pr.13
Software stroke limit lower limit value
Set the lower limit for the machine's movement range during positioning control.
Software stroke
limit lower limit
Software stroke
limit upper limit
OP
(Machine movement range)
Emergency stop
limit switch
Emergency stop
limit switch
1) Generally, the OP is set at the lower limit or upper limit of the stroke limit.
2) By setting the upper limit value or lower limit value of the software stroke limit,
overrun can be prevented in the software. However, an emergency stop limit
switch must be installed nearby outside the range.
To invalidate the software stroke limit, set the setting value to "upper limit
value = lower limit value". (If it is within the setting range, the setting value can
be anything.)
When the unit is "degree", the software stroke limit check is invalid during
speed control (including the speed control in speed-position and position-
speed switching control) or during manual control.
Summary of Contents for MELSEC-L Series
Page 2: ......
Page 30: ...MEMO ...
Page 70: ...2 10 Chapter 2 System Configuration MEMO ...
Page 83: ...3 13 Chapter 3 Specifications and Functions MEMO ...
Page 103: ...3 33 Chapter 3 Specifications and Functions MEMO ...
Page 107: ...3 37 Chapter 3 Specifications and Functions MEMO ...
Page 111: ...3 41 Chapter 3 Specifications and Functions MEMO ...
Page 115: ...3 45 Chapter 3 Specifications and Functions MEMO ...
Page 140: ...4 22 Chapter 4 Installation Wiring and Maintenance of the Product MEMO ...
Page 253: ...5 113 Chapter 5 Data Used for Positioning Control MEMO ...
Page 342: ...5 202 Chapter 5 Data Used for Positioning Control MEMO ...
Page 438: ...7 20 Chapter 7 Memory Configuration and Data Process MEMO ...
Page 440: ...MEMO ...
Page 485: ...9 25 Chapter 9 Major Positioning Control MEMO ...
Page 594: ...9 134 Chapter 9 Major Positioning Control MEMO ...
Page 624: ...10 30 Chapter 10 High Level Positioning Control MEMO ...
Page 656: ...11 32 Chapter 11 Manual Control MEMO ...
Page 690: ...12 34 Chapter 12 Expansion Control MEMO ...
Page 798: ...13 108 Chapter 13 Control Sub Functions MEMO ...
Page 866: ...14 68 Chapter 14 Common Functions MEMO ...
Page 884: ...15 18 Chapter 15 Dedicated Instructions MEMO ...
Page 899: ...16 15 Chapter 16 Troubleshooting MEMO ...
Page 1036: ...Appendix 88 Appendices MEMO ...
Page 1039: ......