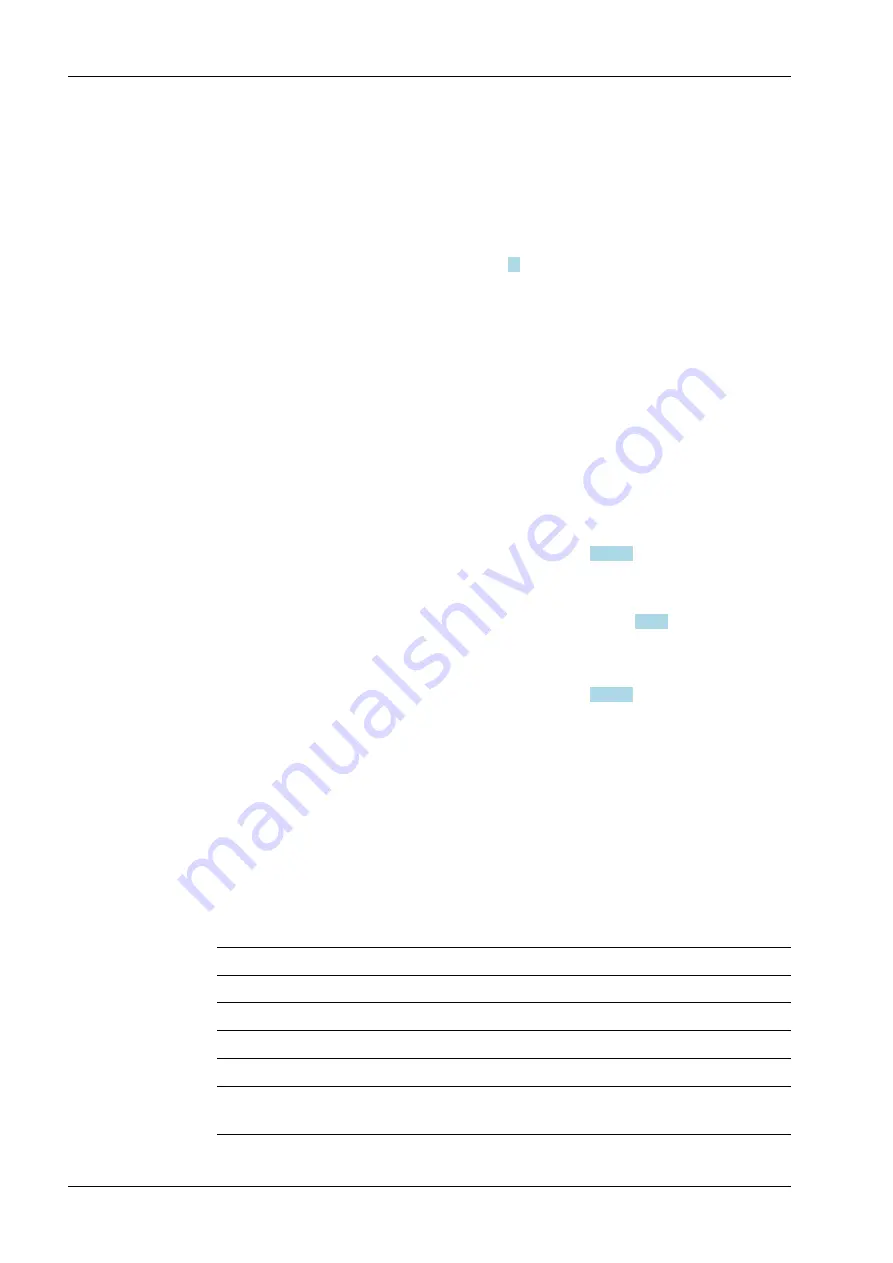
10.12 Brands (Products)
Brand comparison values can be set for individual brand numbers.
Weighing is controlled using the various brand settings to ensure the target (OK) weight
is achieved.
The CSD-903 can save up to 8 brands.
For details of brand settings, refer to Chapter
10.12.1 Brand changeover
The brand number can be changed by function, external control input or communication.
The changeover method is enabled when brand number switching is selected using
function F-51.
To change the brand number in EzCTS mode, set function F-51 to [0: Changeover by
function]
Setting range: 0 to 3
0: Changeover by function
The brand number can be changed by the function F-52 setting.
To change the brand number using standard RS485, RS-232C and RS-422/485, use
communication command [@007052].
For details of communication commands, refer to Chapter
1: Changeover by external control input
Brand number changeover can only be enabled using external control input. If
changeover by external control input is selected, refer to Chapter
2: Changeover by communication
This enables brand number changeover using communication command [@0069].
For details of communication commands, refer to Chapter
The default is [Changeover by key operation].
10.12.2 Brand number
The brand number enabled by measurement control is selected using function F-52.
Brand numbers 0 to 7 can be selected.
Default is set to [Brand No. 0].
10.13 F key settings
F key operation is selected by function F-55.
Setting range: 0 to 9
0: OFF
No setting
1: Print
Inputs the print signal
2: Hold
Inputs the hold signal
3: Inlow start
Inputs the inlow start signal
4: Emergency stop
Inputs the emergency stop signal
5: Zero clear
After zero set and zero tracking are executed, the display
returns to its former status.
Weight indicator CSD-903
10 Various operations by function data
EN-84
Minebea Intec
Summary of Contents for CSD-903
Page 243: ......