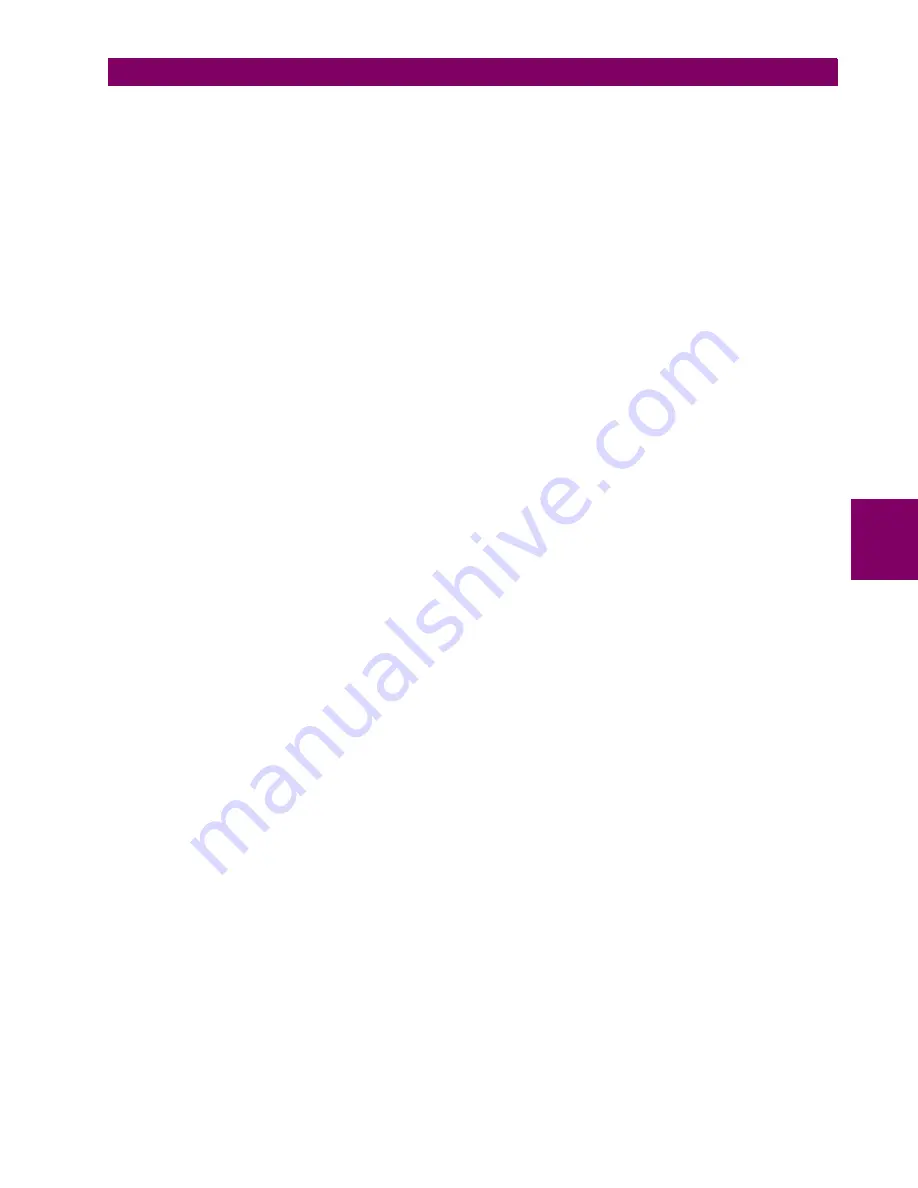
GE Multilin
T60 Transformer Protection System
5-203
5 SETTINGS
5.6 GROUPED ELEMENTS
5
The power swing detect element asserts two outputs intended for blocking selected protection elements on power swings:
POWER SWING BLOCK
is a traditional signal that is safely asserted for the entire duration of the power swing, and
POWER
SWING UN/BLOCK
is established in the same way, but resets when an extra disturbance is detected during the power swing.
The
POWER SWING UN/BLOCK
operand may be used for blocking selected protection elements if the intent is to respond to
faults during power swing conditions.
Different protection elements respond differently to power swings. If tripping is required for faults during power swing condi-
tions, some elements may be blocked permanently (using the
POWER SWING BLOCK
operand), and others may be blocked
and dynamically unblocked upon fault detection (using the
POWER SWING UN/BLOCK
operand).
View the operating characteristic and logic figures along with the following discussion to develop an understanding of the
operation of the element.
The power swing detect element operates in three-step or two-step mode:
•
Three-step operation:
The power swing blocking sequence essentially times the passage of the locus of the positive-
sequence impedance between the outer and the middle characteristic boundaries. If the locus enters the outer charac-
teristic (indicated by the
POWER SWING OUTER
FlexLogic operand) but stays outside the middle characteristic (indi-
cated by the
POWER SWING MIDDLE
FlexLogic operand) for an interval longer than
POWER SWING PICKUP DELAY 1
, the
power swing blocking signal (
POWER SWING BLOCK
FlexLogic operand) is established and sealed-in. The blocking sig-
nal resets when the locus leaves the outer characteristic, but not sooner than the
POWER SWING RESET DELAY 1
time.
•
Two-step operation:
If the two-step mode is selected, the sequence is identical, but it is the outer and inner character-
istics that are used to time the power swing locus.
The out-of-step tripping feature operates as follows for three-step and two-step power swing detection modes:
•
Three-step operation:
The out-of-step trip sequence identifies unstable power swings by determining if the imped-
ance locus spends a finite time between the outer and middle characteristics and then a finite time between the middle
and inner characteristics. The first step is similar to the power swing blocking sequence. After timer
POWER SWING
PICKUP DELAY 1
times out, latch 1 is set as long as the impedance stays within the outer characteristic.
If afterwards, at any time (given the impedance stays within the outer characteristic), the locus enters the middle char-
acteristic but stays outside the inner characteristic for a period of time defined as
POWER SWING PICKUP DELAY 2
, latch
2 is set as long as the impedance stays inside the outer characteristic. If afterwards, at any time (given the impedance
stays within the outer characteristic), the locus enters the inner characteristic and stays there for a period of time
defined as
POWER SWING PICKUP DELAY 3
, latch 2 is set as long as the impedance stays inside the outer characteristic;
the element is now ready to trip.
If the "Early" trip mode is selected, the
POWER SWING TRIP
operand is set immediately and sealed-in for the interval
set by the
POWER SWING SEAL-IN DELAY
. If the "Delayed" trip mode is selected, the element waits until the impedance
locus leaves the inner characteristic, then times out the
POWER SWING PICKUP DELAY 2
and sets Latch 4; the element is
now ready to trip. The trip operand is set later, when the impedance locus leaves the outer characteristic.
•
Two-step operation:
The two-step mode of operation is similar to the three-step mode with two exceptions. First, the
initial stage monitors the time spent by the impedance locus between the outer and inner characteristics. Second, the
stage involving the
POWER SWING PICKUP DELAY 2
timer is bypassed. It is up to the user to integrate the blocking
(
POWER SWING BLOCK
) and tripping (
POWER SWING TRIP
) FlexLogic operands with other protection functions and out-
put contacts in order to make this element fully operational.
The element can be set to use either lens (mho) or rectangular (quadrilateral) characteristics as illustrated below. When set
to “Mho”, the element applies the right and left blinders as well. If the blinders are not required, their settings should be set
high enough to effectively disable the blinders.
Summary of Contents for T60
Page 6: ...vi T60 Transformer Protection System GE Multilin TABLE OF CONTENTS ...
Page 14: ...xiv T60 Transformer Protection System GE Multilin TABLE OF CONTENTS ...
Page 34: ...1 20 T60 Transformer Protection System GE Multilin 1 5 USING THE RELAY 1 GETTING STARTED 1 ...
Page 490: ...5 344 T60 Transformer Protection System GE Multilin 5 10 TESTING 5 SETTINGS 5 ...
Page 522: ...6 32 T60 Transformer Protection System GE Multilin 6 5 PRODUCT INFORMATION 6 ACTUAL VALUES 6 ...
Page 536: ...7 14 T60 Transformer Protection System GE Multilin 7 1 COMMANDS 7 COMMANDS AND TARGETS 7 ...
Page 568: ...10 12 T60 Transformer Protection System GE Multilin 10 6 DISPOSAL 10 MAINTENANCE 10 ...
Page 596: ...A 28 T60 Transformer Protection System GE Multilin A 1 PARAMETER LISTS APPENDIX A A ...
Page 716: ...B 120 T60 Transformer Protection System GE Multilin B 4 MEMORY MAPPING APPENDIX B B ...
Page 762: ...E 10 T60 Transformer Protection System GE Multilin E 1 IEC 60870 5 104 PROTOCOL APPENDIX E E ...
Page 774: ...F 12 T60 Transformer Protection System GE Multilin F 2 DNP POINT LISTS APPENDIX F F ...